Scan by Hand
Creaform's Handyscan 3D facilitates scanning in tight spaces.
Latest News
September 1, 2006
By Marco St-Pierre and Jean Francois Marchand
Reverse engineering a car interior or an airplane cockpit presents multiple challenges. One of the more limiting is the time-consuming aspect of collecting accurate data in a confined space because of the scanner’s, or its operator’s, inability to easily move within the space. Whether you need to reverse engineer for ergonomic studies, competitive analyses, or to design aftermarket parts, picking the right scanning tool can make all the difference.
Creaform, a company specializing in optical scan and inspection devices and software in Levis, Quebec, was asked to cooperate in a competitive analysis study for a car manufacturer. The task was to scan the dashboard, steering wheel, seats, and door interiors of a competitor’s automobile for an ergonomic study.
The goal was to cut the time it took to acquire data from the passenger compartment by more than 50 percent compared to the customer’s previous process. And, this had to be done while maintaining high data accuracy. In order to comply, Creaform used the Handyscan 3D device: a compact, hand-held, accurate, and fast scanner. Portability, ease of use, and short setup time were also considerations as the project involved multiple trips from one plant to another.
|
Scan by Hand |
> > Figure 1: A laser-generated cross enables the system to build a surface in real time. This surface is displayed on the computer screen and calculated to optimize an STL file.
In its previous workflow, the car manufacturer used a laser scanner mounted on a measuring arm. Since tripods and such arms are bulky, they limited the ability to move the scanner in the tight space of a car’s interior—and productivity suffered. Laser scanners mounted on arms or on bulky coordinate measuring machines (CMM), as well as scanners using white light technology are referenced by the origin of the structure supporting them. Therefore, the part being scanned has to be fixed as well. For this reason, there is a high risk of losing accuracy when moving in and out of a car to collect data. Worse than that, if you lose your reference by jostling the part or tripod, the relationship between the scanner and the part will change and you must start your scan over—another waste of precious time and resources.
New hand-held optical scanners use the object being scanned to establish their reference. Because these scanners are self-positioning, they do not need an external tracking device like a CMM or measuring arm to establish their locations in relation with the object. This ability affords a compact design, which makes such scanners truly portable, often able to fit in a case the size of a carry-on suitcase.
Positioning
The Handyscan 3D uses reflective targets applied to the surface of the part to be scanned to position itself. Those reflective targets can be quickly and randomly applied. The only other setup involves connecting a cable to the computer, which takes all of two minutes or less.
|
Scan by Hand |
< < Figure 2: VXScan is constantly updated to show a normal representation of the surface being scanned.
Using this approach, Handyscan 3D technology allows end-users to move the part and the scanner independently without losing track of the scanner’s position in reference to the part. For these reasons, the scanning team at the car manufacturer was able to jump in and out of the car to collect the data. The targets were attached to the car so movements did not affect the quality of the data. It was also possible to scan with the door open for the comfort of the technician as well as scan with the door closed to gather additional data for the analysis.
During the scanning process, the reflective positioning stickers are found and captured by the system in real time. Their respective positions are calculated in reference to the scanner and recorded. The targets on the object create patterns recognized by the scanner. Patterns of positioning features do not repeat because of the random method of application. The pattern recognition allows the scanner to position itself, just like a GPS uses known satellites to establish its position on Earth.
Scanning
Because the Handyscan 3D system uses targets that are fixed on the part, it is possible to scan partially, stop to visualize the STL file, and then resume scanning. This is useful to acquire data where data might not have been collected on the first pass.
Instantly, the scanner positions itself in relation to the part. Using VXScan, software developed for the Handyscan 3D, it tracks positions and scans in real time. When in scanning mode, a laser cross is projected on the part (see Figure 1, above). The cross enables the system to build a surface in real time. This surface is displayed on the computer screen and calculated to optimize an STL file. Real-time surface reconstruction allows users to immediately see on the computer monitor areas of the part that still need to be scanned. With traditional laser scanners, the viewer displays a point cloud that does not give as much information.
|
Scan by Hand |
> > Figure 3: This closeup view of the scan of the dashboard demonstrates VXScan’s ability to perform multi-resolution scans. Flat sections can be scanned in lower resolution, while detailed areas can be scanned at a higher resolution. It enables high accuracy in a small file.
To facilitate this viewing, VXScan is constantly updated to show a normal representation of the surface being scanned. The data acquired is not being hidden by some data acquired on the other side of the part being scanned. By optimizing the STL, users can save post-treatment time because the system is not concerned with managing point clouds. A representation of the surface generated by the Handyscan 3D is shown in Figure 2 (below).
Data Quality
In addition to saving time during the scanning process, the manufacturer also wanted to ensure data quality for an efficient competitive analysis. With traditional scanners, it’s important to avoid overlaps between scanning strips. Adding layers of points would only serve to add noise to the model and affect the overall accuracy and quality of the scan. The Handyscan 3D, however, is able to overcome this challenge based on a surface optimization algorithm. By avoiding point clouds, the more you scan, the more accurate you get. Rather than adding noise to your model, you refine it.
|
Scan by Hand |
< < Figure 4: Traditional point cloud (left) vs. visualisation of surface. Click image to enlarge..
VXScan also offers the possibility to perform multi-resolution scans: Flat sections needing fewer details can be scanned in lower resolution, while sharp edges and more detailed areas can be scanned at a higher resolution. With this functionality it is possible to create a much smaller file with all the accuracy necessary. (See Figure 3, below.)
Another benefit of the handheld Handyscan 3D is that there is virtually no limit to the size of a part that can be scanned. As a result, the automobile’s dashboard can be captured in a single scan. This saves on computing resources and eliminates the need to search for the “best fit” of multiple scans, thereby optimizing accuracy.
|
Scan by Hand |
> > Figure 5: A detail of the visualization from Figure 4.
Another goal was to achieve good data acquisition and scan efficiently even if some of the parts were dark gray. Because dark colors absorb light, it is often difficult for a system to see the laser trace and to capture the shape. But the Handyscan was able to complete the task because the user can optimize the parameters of the handheld scanner beforehand. By pointing it at the surface to be scanned, the system will automatically adjust the laser intensity, and the trace will then be seen by the cameras.
The ability of the car manufacturer to complete this project with a handheld scanner made all the difference. In the end, the speed of acquisition, the compact design, the portability, and the ease with which engineers used the scanner on the project resulted in a total savings in time of more than 60 percent over the former process. Not only is this savings repeatable, but the Handyscan 3D’s self-positioning system generates a surface in real time, surpassing the customer’s objectives and clearly making the project a complete success.
Marco St-Pierre is product manager for the Handyscan 3D, developed and manufactured by Creaform. He has a bachelor’s degree in mechanics from the University Laval in Quebec. Jean Francois Marchand has a bachelor’s in mechanical engineering from the University of Sherbrooke in Sherbrooke, Quebec. He is a scan and inspection specialist at Creaform. Send your comments about this article through e-mail by clicking here. Please reference “Scan By Hand, October 2006” in your message.
Info
Handyscan 3D
Creaform, Inc.
Levis, Que, Canada
Subscribe to our FREE magazine,
FREE email newsletters or both!Latest News
About the Author

DE’s editors contribute news and new product announcements to Digital Engineering.
Press releases may be sent to them via [email protected].
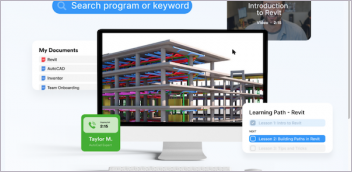

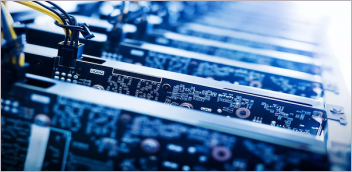
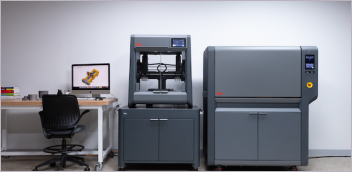