Editor’s Pick: Real-time Process Monitoring for Metal Additive Manufacturing
Sigma Labs PrintRite3D Version 5 offers real-time analysis of metal 3D printing quality.

Sigma TED: 3D thermal emission densite mapping and imaging used in Sigma Labs. PrintRite3D. Image courtesy of Sigma Labs.
Latest News
May 22, 2019
Dear DE Reader:
Additive manufacturing (AM) has turned a corner. The long-sought goal of printing production parts in volume is becoming a reality. For metal AM specifically, the inability to analyze part structure during the manufacturing process has been a key factor limiting mainstream adoption. Thanks to a significant update, Sigma Labs now offers an independent solution for real-time structure analysis during metal AM part production; it’s why PrintRite3D Version 5.0 is our Editor’s Pick of the Week.
PrintRite3D is an in-process quality control platform for metal additive manufacturing. It combines inspection, feedback, data collection and critical analysis. The platform is hardware and software, with multiple sensors and an integrated set of applications.
PrintRite3D gives manufacturers the ability to monitor and analyze key metal AM processes and to identify melt pool disturbances and other discontinuities as they happen. A recent DARPA study says PrintRite3D technology “has been shown to ensure process consistency and product quality in metal additive manufacturing.” The final project for the study was validation of a challenging metal component being manufactured by Honeywell Aerospace using laser bed powder fusion. The conclusion: “This work has demonstrated that a combination of physics-based modeling and experimental verification and validation can enable early-stage identification and elimination of potential problems.”
PrintRite3D is platform independent, it can work with most existing metal AM systems. Using it means you gain an independent third-party source for Quality Assurance. You can retrofit PrintRite3D to existing AM installations or integrate it into new purchases, and the platform is compatible with existing OEM supplied sensors.
Here’s how the process works. The software modules acquire and organize sensor data as the AM build is happening. That data is mined and processed by the onboard analytics engine, providing cross-build correlation and trend charting. The results allow you to make well-informed predictions about process results across machines, plants, and suppliers.
PrintRite3D offers a graphical user interface for real-time display of live part quality results. There is automated anomaly detection on thermal mapping images. Data is collected with fixed X/Y spatial resolution but variable height resolution depending on the manufacturing process. Co-Axial Planck Thermometry is one of several processes used to gather and interpret build data.
We go into much more detail about this breakthrough technology in this week’s Product Brief. Thanks for reading; we’ll see you next week with another Editor’s Pick of the Week.
—The DE Editors
Subscribe to our FREE magazine,
FREE email newsletters or both!Latest News
About the Author

DE’s editors contribute news and new product announcements to Digital Engineering.
Press releases may be sent to them via [email protected].
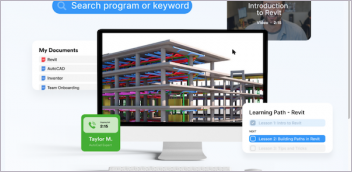

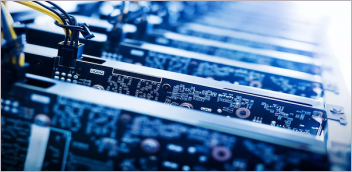
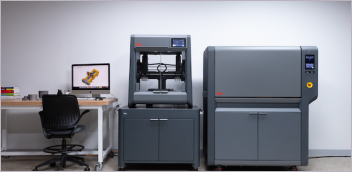