
Wave6 is able to account for installation effects in aero-acoustic applications to account for the way the sound is modified by the presence of nearby structures and acoustic treatments. Images courtesy of Dassault Systèmes.
Latest News
February 1, 2018
When the Briggs & Stratton Q6500 QuietPower Series Inverter Generator was introduced at the Green Industry & Equipment Expo in November, dealers were impressed with the generator’s sound—mostly because they couldn’t hear it running.
The generator is more than 60% quieter, 30% lighter and 45% more compact than standard portable generators. Briggs & Stratton, like many product designers, has a rigorous process for testing noise, vibration and harshness (NVH), an area that is becoming increasingly important in product design for many industries.
Noise Abatement
Understanding noise and vibration performance is a key starting point in designing for improvement. Loudness may be a disruptive feature in many products, but the type of sound that is made can really irk users—sometimes quite negatively.
“Noise and vibration analysis is becoming increasingly important for our clients,” says Phil Shorter, senior director, Dassault Systèmes SIMULIA R&D. “The need to understand noise and vibration performance can arise for many reasons. The way that noise and vibration affect perceived product quality—and the related field of ‘sound quality,’ [or] relationship between how humans perceive certain sounds and certain objective measures of those sounds—is certainly one of the reasons that our clients have an interest in noise and vibration. For example, our clients are sometimes concerned with issues such as the sound that a golf club driver makes when it hits a ball, the sound of an elevator door closing and the annoyance caused by squeaks and rattles in complex assemblies with many fasteners and whether this will affect industry standard Initial Quality Study (IQS) surveys for their products. However, perceived product quality, and the separate field of sound quality, are not the only reasons that our clients are interested in noise and vibration performance.”
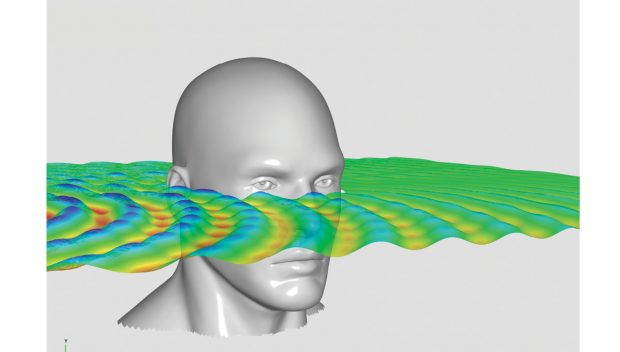
Shorter says that one of the big challenges when designing a product is that you often have a limited amount of time to make design decisions because of schedule and cost constraints.
“The earlier in the design cycle that you can make design decisions, the more likely it is that these design changes will have an influence on the final product,” he says. “If you find a noise and vibration problem late in the design cycle you’re often constrained in how you can respond and you can often end up with expensive band-aid fixes that may not be optimal in terms of things like cost and weight.”
Design engineers are increasingly asked to answer questions about the expected noise and vibration performance of their products earlier and earlier in the product life cycle, Shorter says, often at the conceptual design stage. Those demands call for an increased use of noise and vibration simulation in the design of products, rather than at the prototype or testing stages.
NVH Testing with Real-Life Insights
NVH testing can be challenging for design teams of today. “Modern engineering challenges impact testing teams,” says Steve Dom, automotive solutions manager and simulation and test business segment manager for Siemens PLM Software. “The essence of testing today is to support the engineering process with real-life insights.” He identifies various needs that NVH testing teams need to address.
First, Dom sees a need for increased productivity: Testing teams today need to test more with less resources, while having fewer prototypes available. One test should deliver all of the necessary information on the first shot.
He also sees a need for more innovation: To remain competitive in the marketplace, manufacturers need to innovate. Tests remain an essential step of innovation and are mandatory to validate innovative designs—for example, to validate the acoustic properties of new materials.
Dom says NVH designs must deal with mission-critical safety and increased regulatory pressure. “In some industries, failures have dramatic consequences,” he says. “Test remains the only method to certify that the product will not fail and will behave according to specifications.
“Governments increase regulatory pressure and require test results as proof of compliance to the regulations. For example, in many industries, it is critical to quantify the sound power emitted by a machine so as to be able to limit the noise level. Sound power testing helps develop superior products that respond to the industry demands and the ISO certification while improving competitive advantage and supporting branding strategy.”
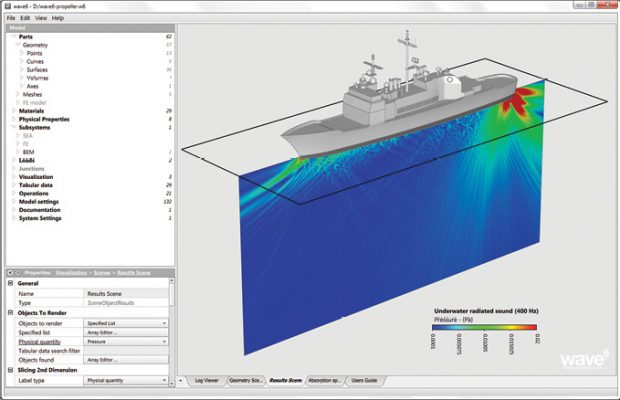
He continues, “In the transportation industry, pass-by noise testing measures vehicle noise emission levels on an exterior test track. Certification departments of vehicle manufacturers use the results of pass-by noise tests to confirm that vehicles comply with specific noise emission standards. This certification is required for all types of road vehicles—from trucks and buses to passenger cars and recreational vehicles.”
Brett Birschbach is the senior engineering manager of NVH for Briggs & Stratton in Wauwatosa, WI. The company uses state-of-the-art data acquisition and analysis software to efficiently test products and develop more effective noise reduction solutions.
“One area [where] we have spent a significant amount of time is utilizing sophisticated engine simulation and CFD (computational fluid dynamics) software to improve our muffler design,” he explains. “These tools provide greater insight during the muffler design process by proving the optimal trade-off between noise reduction and performance of the engine.”
User-Friendly NVH
Designing for noise, vibration and harshness suppression means putting the end user at the center of the product experience. What will they experience and how will they react? What can be done to accommodate their experience?
Designers need to incorporate these questions into their testing as well as materials selection and design.
To date, sound quality has generally been approached in one of two very different ways, according to David Bowen, director of the Noise and Vibration Group of Acentech in Boston.
“One way is to rely entirely on preexisting computational metrics such as loudness, sharpness, roughness, etc.,” he explains. “The other way is to incorporate the use of jury or listener panels as the ‘instrument’ to provide quantitative feedback on a range of possible product or device sounds to help guide design modifications.”
He says that the former is much simpler but has a distinct disadvantage in that it leaves out product context, which can often be very important in how users judge, what he calls “acceptability” of product sounds—when users are actually using these products.
Sound is a distinguishing feature that can be used to separate brands, and as such, manufacturers want to “design” preferable sound profiles for their products.
Product manufacturers and their designers must be well aware of the user’s experience and incorporate a rigorous testing program where NVH greatly influences product quality and the overall ownership experience.
“We believe that low noise and vibration are key drivers for product improvement that will differentiate our brand and provide a competitive advantage,” says Birschbach. “Driving to the lowest possible noise and vibration characteristics will improve the perception of both the product and brand quality resulting in a positive ownership experience.”
Subscribe to our FREE magazine,
FREE email newsletters or both!Latest News
About the Author

Jim Romeo is a freelance writer based in Chesapeake, VA. Send e-mail about this article to [email protected].
Follow DE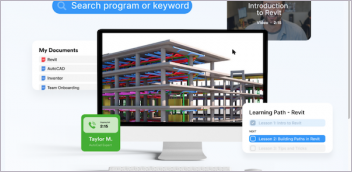

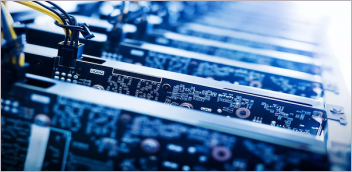
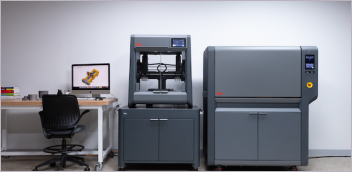