Latest News
August 1, 2005
By Ann Mazakas
This is the sixth in a series of interviews with leaders in the CAM industry.DE
Alan Levine joined OPEN MIND in 2003 after 20 years of involvement withmanufacturing and CAM software in the turbomachinery and gas turbinesector. Over the course of those two decades he held various positionsand developed broad viewpoints on customer support, applications,product development, and eventually management, sales, and marketing.Currently the managing director of OPEN MIND Technologies USA, Levineis responsible for sales and service of OPEN MIND’s hyperMILL productin North and South America, and also leads a product strategy committeeof key OPEN MIND staff at headquarters in Munich, Germany, to helppromote and guide the direction of hyperMILL for the turbomachineryindustry.
What is your development strategy for hyperMILL?
Levine: Our focus at OPEN MIND is on milling and streamlining the CNCprogramming process. We put a lot of thought into understanding whatour customers go through with cost pressures and competitive pressures.They need to be quick and the software interface needs to be seamlessand helpful, and the machining processes have to be efficient. Moreorganizations are investing in multiaxis and high-performance machines.For multiaxis applications, we need to solve problems in a way that isfairly easy for the user. If 5-axis programming is too complex theywon’t do it. Machinists need to work in a system they have confidencein; confidence that they can use it and confidence in their results. Wealso try to give our users several different approaches to machining,which is somewhat in contrast with making it easy to use. Some peoplewant a high level of detail, while others are looking for somethingsimpler. When we design our interfaces, a lot of thought goes into itand a lot of auditing of users. You don’t want the software to dictatehow a part is machined by offering only a limited number of machiningstrategies. You want the user’s creativity to be the guiding force. Thesoftware should be a tool that enables their vision of the finalresults to shine through.
How does OPEN MIND address the increase in multiaxis programming?
Levine: The new multiaxis milling machines have incredible performancegains over their predecessors. This may be measured through dynamicperformance of the machines, or by increased controller processingspeed or functional capability. There really is no other choice todayin machining technology. The markets are good and the solutions need tomatch. From a customer and user point of view, the machine tool markethas more multiaxis choices and capabilities, and better prices than inthe past. OPEN MIND has a long history in providing multiaxis CAMsolutions. We approach multiaxis work with multiple levels oftechnology. It’s exciting and interesting and we work hard to presentthat technology in a step-by-step process.
Do you also streamline programming with features?
Levine: Several years ago we adopted feature technology and we continueto develop much more technology in that area. Initially, featuretechnology looked at a design model and recognized holes, planes,pockets, and some standard geometry in order to save the programmersome time. We’ve already covered that baseline geometric recognitionissue, and have also applied that technology to surfaces on arbitraryorientations. The next step is to build in process knowledge. Once yourecognize pockets, there are certain ways you want to machine them.Each shop may do this differently and we want to capture thatinformation. We can store macros and machining processes without thegeometry and link that information to a feature. The next time you havea new job, you just define the geometry and attach the machiningprocess in order to save time and also build in knowledge and machiningstandards.
I recently visited a customer who was growing rapidly and hiring kidsout of trade school. They don’t want to overwhelm these kids by havingthem run the machinery and do all the programming. This customer usesour technology to standardize the parameters for the differentoperations they perform in the shop. The new employees can use thisacquired knowledge as a database so they can learn how to use thesoftware without becoming a process engineer from day one. Over timethey learn and will ultimately be involved in the process developmentthemselves. However, the immediate priority for this company is to pushwork out the door. The ability to train and educate new employeesquickly pays back big dividends and feature technology enables them todo that.
How do you see features evolving?
Levine: The next step we’re looking at in feature technology is calledan application feature. This new type of feature is dedicated not justto a geometric entity or a cutting process but involves a much morecomplex application such as a turbocharger compressor or a tire mold.Often, these application features are applied to a “family of parts"and generally have multiaxis machining requirements.
Sometimes these machining approaches are specific to a particularindustry. While a usual feature is a hole or a plane, an applicationfeature is an industry-specific geometric and process knowledge that wedevelop or enable the user to develop, store, and use. By setting theparameters and storing them they can customize it to their company andindustry.
What exactly is an application feature?
Levine: In some industries such as turbomachinery there have beensingle-point solutions that focus solely on that industry. Thesesolutions tend to be useful, but they are also expensive and somewhatlimited in their scope.
So now we’re taking a CAM system and keeping all its wonderful generalfeatures but also applying that technology to specific industries in away that is competitive with these single-point solutions. We giveusers the tools to customize their solution without requiring that theyhave programming knowledge. It is still a matter of working with theCAD/CAM tool, but the user is not a programmer. In the turbomachinerysolution there are a handful of named entities that an industry insiderwould expect to see. The user will select the surfaces and otherimportant descriptors such as the blade count, load them into ourfeature definition, and the system can proceed. You only need to selectit once, and the system stores it for you.
With tires it’s the same thing. We can define a tire feature by itsbasic geometry and some pattern-spacing parameter, and then we entermachining parameters that make sense for that tire feature.
These industries use specialized design approaches, and the applicationfeatures let them use specialized machining approaches. The industry asa whole is happier with letting people drive their own solutions up toa certain level. If they want to completely control their destiny, theyget into the programming business themselves.
How else does hyperMILL streamline programming?
Levine: We have a series of cycles generically called cavity cycles, orsurface-independent cycles. The x, y, z movement of the tool is drivenoff the surfaces, and a guide curve is used to orient the cutter inspace using a very flexible method where the tool leans toward it butnever past it. We also have automatic indexing. The user can choosedifferent numbers of sectors around the entire part, and the systemwill develop a fixed inclination for each sector. In between theseinclinations you’ll get a 4- or 5-axis move while the tool is in air.This provides a big benefit because it cuts faster and the cutter wearsdown incrementally so you don’t see mismatches between areas like youdo with traditional index milling.
We also have rework machining, a fairly interesting process where oursystem detects interference areas in a 3-axis or 5-axis cut. You cantell the software to stop when interference is detected or create twoseparate programs, one for the regular toolpath and one for theinterfering. The idea is to take an existing toolpath as a referenceand, without too much work, add your tool orientation to that. Ourrework cycle lets you try different scenarios very quickly because thetoolpath doesn’t have to be recalculated.
What can we expect in your recent release of hyperMill 9?
Levine: The big effort in hyperMILL 9 is an in-process stock modelmanagement system and stock-model based roughing. The benefits of aprocess-oriented system are good record keeping, an organized system,and tracking. This is step one in the development of a whole new way torough parts and by version 10 it will be our only roughing cycle.Basically, you tell the system what your final part looks like, tell itthe stock you’re starting from, add some parameters, and hyperMILL willmachine it from there. Based on different step overs, we will recognizethe difference between your first and second roughing cutter, where thematerial is, when you’re in air, when to cut at rapid feedrates, andwhen there are chips to pull out. This can also be done in multiaxis.It’s quick, usable, and can be applied in different situations andsaved in different formats. A lot of people really like that. You cansee the results graphically step-by-step in order to make yourdecisions on what to do next.
Version 9 also allows the user to enter a generalized description of acutter holder or the spindle head, and to use this information incutter path interference detection calculations. To enable thisgeneralization, we simultaneously increased the robustness of thesecalculations and greatly improved the processing speed. Plus, thefeature technology will be available in our hyperMILL in AutodeskInventor product for the first time.
How does OPEN MIND decide what to include in each software release?
Levine: We have a major release of our software once a year, withinterim solutions in between. Ideas for enhancing our software are madeby a product management team in our home office. They work very closelywith our key customers and machine tool partners. We recognize that theneeds in the US are different than in Germany or China. Along with thiscommittee, there are also opportunities for the engineers andsalespeople working in foreign offices to offer their input and wishlists. We have internal technical conferences where people can explainwhat they are running into in their markets. In the end, the process isdetermined by input from every office and a very dynamic and livelydiscussion about what will be a good investment for the product. It’simportant to us that all our customers feel they get value from theproduct year after year.
For future development, we have a long-term planning committee that Imanage. This has been a good step for us. Previous generations of thisplanning process helped to identify important CAD platforms and featuretechnology before they ever came to market. We consistently grow aheadof market averages, and we want to identify a future where we cancontinue to be a leader.
Ann Mazakas is a long-time writer on CAM and manufacturing industryissues. Send your feedback on this article via e-mail by clicking here.Please reference QandA, September 2005 in your message.
Company Highlights
Company: OPEN MIND Technologies USA, Inc.
Headquarters: Wellesley Hills, MA
Founded: 1994
Product: hyperMILL, hyperCAD
Subscribe to our FREE magazine,
FREE email newsletters or both!Latest News
About the Author

DE’s editors contribute news and new product announcements to Digital Engineering.
Press releases may be sent to them via [email protected].
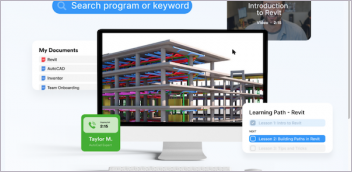

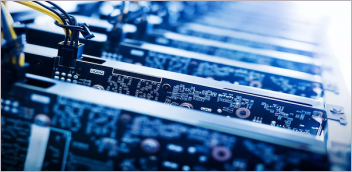
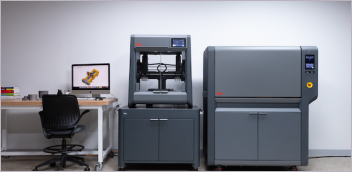