Perfecting Wind Tunnel Balances

A Model position system. Image courtesy of Triumph Force Measurement Systems.
Latest News
June 1, 2016
Designers of devices ranging from aircraft to wind turbine blades to helmets must understand the effects of wind currents on performance and efficiencies. Smoke trails can illustrate how the wind passes over and around an object, but can’t determine the forces exerted by the wind on the object. For that, strain gage wind tunnel balances are required — extremely complex, six-degrees-of-freedom transducers to which models are mounted to determine behavior during wind tunnel testing. These transducers can cost as much as $40,000 and take up to a year to design, fabricate, and calibrate.
In wind balance tunnels, strain gages are used to translate forces into an electrical signal that can be measured and recorded for analysis. The locations where the strain gages are placed are typically very small and difficult to access, and the devices are extremely difficult to replace should the need for repair ever arise. Therefore, strain gages must not only be exceptionally small, but must also be robust and reliable once installed.
The Solution
To meet the needs of strain gage wind tunnel balances, Micro-Measurements’ Advanced Sensors Technology says it uses the finest materials and a patented manufacturing process to produce devices with extremely tight resistance tolerances that cannot be achieved with conventional strain gage manufacturing techniques. The result, according to the company, are exceptionally reliable and accurate strain gages. Additionally, these specialized manufacturing techniques make it possible for Micro-Measurements to deliver devices with very high resistances of 1 kΩ, 5 kΩ , and even 10 kΩ in very small footprints. This high resistance allows for increased excitation voltages and an improved signal-to-noise ratio.
The User Explains
A major challenge faced by strain gage wind tunnel balance manufacturers is sourcing high-performance strain gages with tight tolerances, long-term stability, and high reliability.
Wind tunnel testing continues to require increased loads per unit diameter from balances. The drive to improve balance performance and increase the operating envelope for high alpha and beta testing requires a change in the basic balance load range. Additionally, the aircraft’s exterior lines limit the ability to accommodate large diameter balances or balances with high deflections that are required to meet these higher loads. To test at these conditions, a wind tunnel balance must be capable of providing accurate model loads data under high combined loading conditions, while allowing the model to maintain its aerodynamic shape. The increased load and decreased deflection requirements have challenged us to develop our next generation of force type balance with an Advanced Sensors strain gage.
The flexure design permits a significant increase of roll movement by reducing allowable normal force. The balance can be characterized over multiple load ranges, while maintaining the high-accuracy performance. This would allow multiple balances covering separate load ranges to be replaced with one hybrid force balance.
Today, Micro-Measurements’ Advanced Sensors gages — when installed employing Micro-Measurements’ M-Bond 610 adhesive and other accessories — provide the reliability, durability and long-term stability necessary for this demanding application, according to the company. With the high cost of producing these devices, it is imperative that once assembled and calibrated, the balances provide long-term reliability.
More Info
Subscribe to our FREE magazine,
FREE email newsletters or both!Latest News
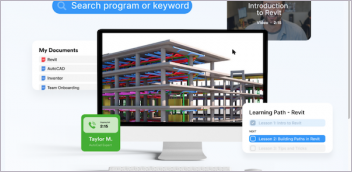

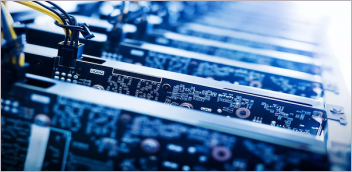
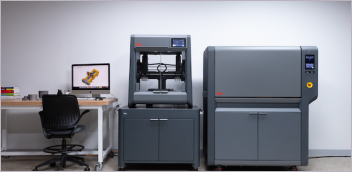