Latest News
June 1, 2010
By Steve Luby, Vistagy
![]() |
When high-performance composites first emerged several decades ago in the aerospace industry, the question was, “Can we make it and, if so, will it break?” But as more industries have adopted composites successfully, the questions have become more sophisticated. Now manufacturers must ask, “Can we increase the manufacturing rate while lowering the weight of the part? Can we use new materials to optimize part performance while reducing costs?”
While the use of composites is growing rapidly, even during the current economic downturn, this growth represents a small percentage of the potential. And it is a fragmented potential because materials and processes; shapes, sizes, and tolerances; part definitions; and outputs are becoming more industry-specific. In fact, composite parts and assemblies can be as different in shape, size, and make up as a two-inch long guiding vane for a jet engine or a 200-foot wind turbine blade. Clearly, one approach no longer fits all.
While there is overlap in engineering with composite materials among certain industries, the combination of unique business conditions and technical requirements means the optimal strategy and best methodologies will differ and must be taken into account.
Consider that the aerospace industry started with small, non-flight critical composite parts for fighter jets and helicopters, but now uses composites for everything from a commercial airliner’s entire wing and fuselage to landing gear struts. This requires figuring out how to integrate the design and manufacture of composites with the complexity of managing the development of the airframe. It also requires consolidating a huge number of parts and assemblies as well as design in an increasingly automated manufacturing process. Further, an airplane can be in use for 30 or 50 years, so the stakeholders must manage repair, maintenance, and upgrade issues.
While composites have been used on racing cars for some time, their adoption by the automotive industry is relatively new. Of course, this brings new challenges such as the need to simulate and pass crash tests in a high-volume production process. Additionally, it is critical that automotive firms use automated manufacturing to achieve optimum cost and rate goals as well as a reliable and repeatable process. The potential widespread adoption of composites by auto makers is also driven by multiple and conflicting environmental concerns, namely the quest for fuel efficiency and the viability of recycling huge amounts of materials.
Efficiency is also a concern in the wind turbine industry where blades are meant to last for 20 to 30 years under all kinds of weather conditions with minimum maintenance efforts and costs. As blade length grows, production efficiency increases. Unfortunately, blade weight grows even faster, and with turbine diameters currently topping out at about 400 feet, minimizing composite blade weight has become critical.
Other industries adopting or increasing use of high-performance composites are the marine, infrastructure, and consumer sectors for a variety of reasons. And while many industries are in the very early stages of using composites, this much is clear: As more designs are undertaken and more engineering software is used to understand these materials, the better the next effort will be. These successes will lead to cross-fertilization between industries and accelerate the continued expansion of composites.
Combine these factors with the availability of new materials, processes, and design and analytical tools, and perhaps it is time to examine the potential for composites in your industry.
Steve Luby is founder, president and CEO of VISTAGY, Inc. Send feedback about this commentary to [email protected].
Subscribe to our FREE magazine,
FREE email newsletters or both!Latest News
About the Author

DE’s editors contribute news and new product announcements to Digital Engineering.
Press releases may be sent to them via [email protected].
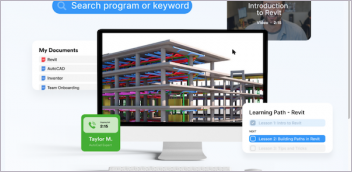

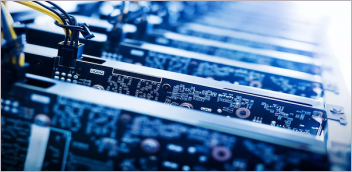
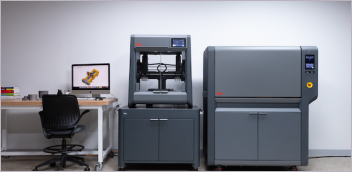