No Salt Required. 3D Printing is Key to Desalination

GE engineers pose in front of a full-scale turbine with a 3D printed miniature version. Courtesy of GE Global Research.
Latest News
April 20, 2016
No matter market forecasts or financial prophecies of doom, use of additive manufacturing (AM) continues to grow and expand. When companies the likes of GE continue to invest in something, the shrill cries coming from investors seem less significant.
The latest use for AM comes from GE Global Research. It’s no secret parts of the US and the rest of the world are desperately in need of fresh water, and desalination offers a potential solution. The US Department of Energy tasked GE with the job of figuring out a workable solution, and the results have ties to both 3D printing and the roots of the company.

Part of GE’s early success was a result of collaboration with Thomas Edison. The famed inventor helped the company design steam turbines, which formed the backbone of America’s industrial revolution. Coincidentally, it turns out that building functional desalination systems relies largely on the same set of principles as those behind steam turbines.
The key difference between modern desalination systems and steam turbines is temperature. Researchers use the basics of steam to drive a combination of salt water and air through a hyper-cooling loop that freezes the water. As it freezes, the salt naturally separates from the water, leaving behind chunks of pure water in the form of ice.
“97.5% of the Earth’s water supply is virtually inaccessible because water desalination is still too expensive and difficult to deploy at a large scale. By putting desalination ‘on ice,’ we hope to change that dynamic,” said Vitali Lissianski, a chemical engineer and project leader at GE Global Research’s Energy Systems Lab. “Freezing seawater to treat it is nothing new, but the way we are doing it is very different. We’re tapping into our wealth of technical knowledge in turbomachinery to devise a cost-effective solution.”
As is the case for many modern research projects, AM enters the scene when practical testing begins. Rather than build full-scale desalination systems, engineers build scale prototypes that rely on 3D printed parts. In this particular case, GE researchers used AM to construct miniature turbines that could be relied upon to perform in a fashion nearly identical to a full-scale version. Without access to AM, researchers would be left with computer simulations or hand-crafted prototypes.
Below you’ll find a video from Bill Nye that explains the benefits of large-scale desalination.
Source: GE Global Research
Subscribe to our FREE magazine,
FREE email newsletters or both!Latest News
About the Author
John NewmanJohn Newman is a Digital Engineering contributor who focuses on 3D printing. Contact him via [email protected] and read his posts on Rapid Ready Technology.
Follow DE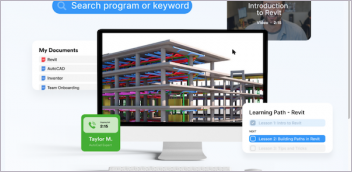

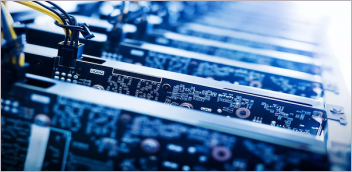
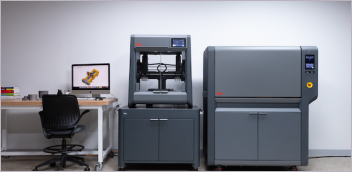