
An eigenvalue analysis of an engine subassembly created with MSC Apex is pictured. Image courtesy of MSC Software.
Latest News
May 4, 2016
Apex Eagle is the name of MSC Software Corp.‘s fifth edition of its Apex CAE platform. This release, says the company, delivers innovative solutions for modeling and validating complex assemblies with the introduction of new part representations and connection types. MSC says that early users report that the enhancements in Apex Eagle can accelerate complex assembly layout modeling and validation by up to 10x compared to previous versions of the platform.

The Apex Eagle release introduces updates to Apex Modeler, the platform’s CAE-specific direct modeling and meshing solution, says MSC. Additionally, Apex Eagle also marks the debut of the third release of the platform’s fully integrated and generative structural analysis solution module, Apex Structures.
MSC Apex Eagle’s new part representations and connection types features are all fully integrated in the Apex generative framework, which supports the automatic regeneration of simulation results when users make changes to a part’s geometry or an assembly’s layout.
New features include support for shell elements (2D), and tetrahedral and hexahedral meshing (3D) now support discrete mass and rotary inertia (0D) as well as beam elements (1D). New connection types include rigid links, springs and mesh-dependent tie connections, which extend the software’s existing mesh-independent “glue” technology for connecting regions of a finite element mesh.

Beginning with the Apex Eagle release, users can now create assemblies that support the rapid conceptual design of subassemblies and vehicle-level assemblies. Chassis frames for automotive, reinforced fuselage and wings structures for aerospace, welded assembly structures for shipbuilding as well as large fastened assemblies for heavy machinery and equipment companies are a few of the potential applications that MSC cites.
All rigid links, springs and discrete mass attachment regions automatically incorporate distributed coupling in their definitions. MSC explains that, as such, they are presented to the user in the form of an engineering abstraction rather than as individual finite element entities. The company adds that this helps boost assembly modeling productivity and ease of use. Furthermore, the new connections are integrated into the Apex generative framework and regenerate when users modify parts or change their relative spatial position.
Additional new features include a new Edge Tie tool that allows users to create a continuous mesh topology across parts without altering the product parts and assembly structures, the ability to define gravity loads and new vector plots. Enhanced existing features include the ability to map mesh multi-edge faces (five and more), incremental mid-surfacing face pair and offset definition are now persisted, and left and right offsets are visually identifiable.

“Eagle Beta testers have told us they were able to accelerate their productivity by a factor of 10x,” said Hugues Jeancolas, MSC Apex senior product manager, in a press statement. “Incremental changes to the design, whether on parts, attribution, but also assembly layout are captured in a dependency chain that allows the user to automatically regenerate the model and visualize simulation results at a click of a button, giving users a unique flexibility to rapidly iterate on design alternatives early in the design process.”
With the Apex Eagle release, MSC also released its first MSC Apex Student Edition as a complimentary download for students currently working towards a degree in the engineering field. Also available is a complementary, no-cost MSC Apex Curriculum Kit for professors and students. It provides eight walk-through examples and assignments, covering such topics as stress, strain and Poisson’s Ratio; stress and deformation of a solid beam; and circular beams in torsion. MSC says that the kit is ideal for engineering students currently enrolled in a course focusing on the mechanics of materials or the strength of materials.
For more information on the MSC Apex CAE platform, visit MSC Software.
Watch a webinar on MSC Apex Eagle highlights.
Access the MSC Apex on-demand webinar library.
View a sampling of MSC Apex’s 100 embedded help videos.
Download a 30-day free trial license and the MSC Apex installer.
Download an MSC Apex Modeler solution brief.
Download an MSC Apex Structures solution brief.
See why DE‘s editors selected the MSC Apex Eagle release as their Pick of the Week.
Sources: Press materials received from the company and additional information gleaned from the company’s website.
Subscribe to our FREE magazine,
FREE email newsletters or both!Latest News
About the Author

Anthony J. Lockwood is Digital Engineering’s founding editor. He is now retired. Contact him via [email protected].
Follow DE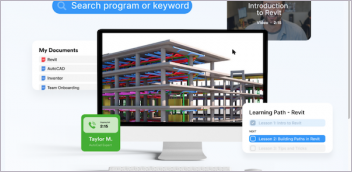

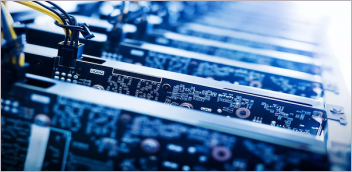
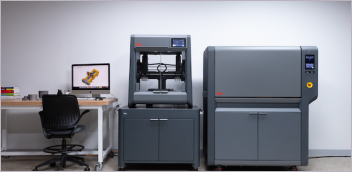