Mojo 3D Printer Winner Reaches New Heights

Jacob Skaggs with the Stratasys Mojo 3D printer he won as part of the Rapid Ready Tech Sweepstakes.
Latest News
December 19, 2014
Mechanical engineers generally consider themselves experienced after they’ve designed hundreds of parts and brought them from initial concept into final manufacturing. Gaining that experience often takes years to achieve, but Jacob Skaggs, a recent college graduate and project engineer at Century Elevators in Houston, TX, got an accelerated start. While on a manufacturing engineering internship at Invent-a-Part, a Utah service bureau, he did CAD designs for a wide range of prototypes and saw them produced on various models of Stratasys Fused Deposition Modeling (FDM) and PolyJet equipment.

This familiarity with 3D printing systems and their usefulness put Skaggs in the perfect position to appreciate winning his own Stratasys Mojo 3D printer in the third annual Desktop Engineering and Stratasys Rapid Ready sweepstakes. The Mojo system and its WaveWash 55 support-removal system now sit side-by-side in his office with a CAD workstation on which he designs typically one-of-a-kind machined parts for industrial elevator installations.
The Mojo unit arrived two days before Thanksgiving, so Skaggs downloaded some appropriate holiday-motif 3D CAD files for an initial test. “I was actually surprised at how easy [the Mojo] was to set up,” says Skaggs. “In a couple of hours, I was ready to print.”
His first 3D print run quickly produced sample table place-card holders shaped as — what else — a turkey and a classic Pilgrim hat. From there he was ready to try the system on a real part, figuring it would help him speed up manufacturing parts he commonly designs. It’s actually helped do much more.
Creating Better Designs
Projects at Century Elevators can be an interesting challenge because every installation is different. Focused on industrial and commercial lifting systems for construction sites, refurbishments and maintenance jobs, the company works on everything from power plants and petrochemical facilities to bridges and commercial buildings. While the elevators themselves are self-contained units, the company must design custom tie-in brackets and struts to connect the units to steel truss setups reminiscent of giant-sized Erector-brand toy sets. Each tank, silo or building framework is constrained by different geometry and space limitations.
Oftentimes, a customer will provide basic project descriptions over the phone, saying the elevator needs to run a certain number of stories tall, transport so many pounds of materials and personnel, and fit into a footprint of x square feet. Skaggs, along with colleague Erik Nordfelth, lead engineer and project manager, must translate those specifications into detailed designs and define the connecting hardware. Machining a basic prototype can take several days, and the part may need several revisions after site visits highlight further requirements.
On his second day of Mojo ownership, Skaggs designed and printed a two-part prototype eyebolt bracket based on a verbal description. The 4 x 3 x 2 in. sections took about eight hours to print and easily fit into the Mojo’s 5 x 5 x 5 in. build envelope. “I was able to design something based on what they told me, and then I was able to check my design and make sure we were on the same page, that my concept would work,” he said.

Skaggs says the Mojo will help him manufacture everything from prototype brackets to a missing knob on an in-house machine.
“When you have this technology, it changes the way you think about projects and what you can do,” he says. “Before, we were always trying to think of the simplest way to take care of something. Now you can change your mindset to think of the best way.”
Read about the 2013 Rapid Ready Sweepstakes winner.
Read about the 2012 Rapid Ready Sweepstakes winner.
Below is a video produced by Stratasys to introduce the Mojo 3D printer:
Subscribe to our FREE magazine,
FREE email newsletters or both!Latest News
About the Author

Pamela Waterman worked as Digital Engineering’s contributing editor for two decades. Contact her via .(JavaScript must be enabled to view this email address).
Follow DE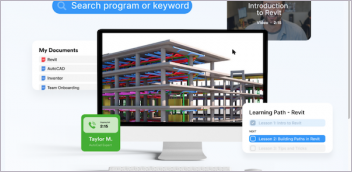

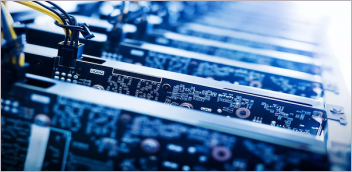
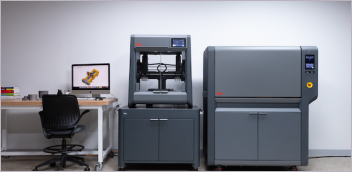