Metal Mania in the Rapid Tech World
When plastics just won't do, explore more hefty manufacturing options.
Latest News
August 1, 2011
By Pamela J. Waterman
![]() A bone rasp under development by Within Technologies for manufacture on an EOS laser-sintering system. The part represents a particular challenge for AM building, because the surface is covered with 2x2mm pyramids whose orientation keeps changing to match the overall shape of a helix. Image courtesy EOS and Within Technologies. |
As quickly as cars morph into robots in this summer’s Transformer 3 movie, new options in rapid metal technology continue to transform the world of manufacturing.
When a part’s end-use requirements call for metal, many factors determine the best material and process. High strength, excellent thermal conductivity, machinability/weldability, corrosion resistance and the ability to create extremely smooth surfaces may all be on the list. Beyond that, design complexity, a need for customization, and control of such properties as material density may point directly to using one of today’s “rapid” technologies. Add in the cost of materials, equipment, training and operations, and designers can face a complex array of options—but with potentially stunning results.
From machined aluminum and stainless steel to formed parts crafted in exotic titanium alloys, metalworking in recent decades has drawn upon an increasing range of rapid manufacturing technologies and raw materials. These choices continue to expand, thanks to the ingenuity in worldwide R&D.
DE helps you sort through the possibilities, from build materials and systems to service bureaus and value-added processing.
![]() This Direct Metal Deposition rebuilt turbine blade squealer-tip was done on a POM Group system. Sizes vary from 50mm to 600mm (H). Image courtesy POM Group. |
Direct Metal Manufacturing
A Big Three group dominates the industry of creating parts directly in metal: 3D Systems, Arcam and EOS. Not surprisingly, 3D Systems, the 25-year-old pioneer of additive manufacturing (AM), plays a strong role with its Selective Laser Melting (SLM) systems. (See “Additive Manufacturing 101,” DE November 2010, for additional AM acronym definitions.)
However, Arcam and EOS, with their Swedish and German headquarters, respectively, have enjoyed the advantage of European medical regulations that historically permit much broader use of AM parts than Food and Drug Administration (FDA) regulations in the United States. That acceptance has boosted medical and dental applications to form the largest segment of direct metal production parts.
Finishing Touches
|
Sinterstation Pro DM125 and DM250 SLM systems (differentiated mainly by their build volumes), both from 3D Systems, produce fully dense end-use parts by laser-melting a powdered version of steel, aluminum or titanium alloys. System specifications list excellent surface finish, feature detail and tolerances as attributes of final parts that make them suitable for a wide range of use.
3D Systems’ SLM applications include lightweight aerospace and motorsports parts, custom medical implants, efficient heat sinks, dental caps and crowns, and injection-mold inserts with conformal cooling channels. The last example highlights one of the distinct capabilities of additive manufacturing: achieving internal geometry in a single piece that, if traditionally machined, would otherwise require an assembly of multiple parts.
Arcam, founded in 1997, employs Electron Beam Melting (EBM) technology to create parts from powdered metals, primarily titanium Ti6Al4V (Grade 5). This biocompatible alloy has served as the foundation of the company’s extensive market in orthopedic implants. The Arcam A1 system is designed to produce custom and standard medical implants in both titanium and cobalt chrome alloys, while the Arcam A2 is optimized for producing large, complex metal parts for the aerospace and defense industries.
Since 2007, Arcam’s European customers have used EBM technology to produce and implant more than 10,000 CE-certified advanced orthopedic implants. Until recently, any such parts produced by U.S. customers were limited to patient-specific implants. However, in February 2011, Arcam announced a significant marketing development: U.S. manufacturers have received FDA clearance to broadly market Arcam EBM products in the states. Arcam says that the U.S. market represents about half of the worldwide implant market.
Metal parts made on EOS’ direct-metal laser sintering (DMLS) systems run the gamut from aerospace (turbines) and automotive (custom race-car parts) to jewelry (custom titanium pendants) and tooling (inserts). EOS DMLS ductwork can be shaped exactly to fit an optimum air flow path, instead of having the design be driven by cutting paths or limited by minimum draft angles. Plus, EOS medical applications include custom knee joints and dental crowns and bridges.
The EOSINT M 270 has been a metals workhorse for years. Now joining that system, the just-announced EOSINT M 280 offers more options than ever for material choice: Because the M 280 unit can operate with either nitrogen or argon protective atmospheres, users can elect to work with light metals, tooling steel and super alloys including titanium, aluminum, cobalt chrome and Inconel (an iron-nickel combination).
![]() The third-generation SLM 250 System from MMT Group (now part of Renishaw). Enhancements over previous models include variable powder delivery, ultra-low oxygen content in the build atmosphere, and a safe-change filter system to minimize user materials-contact. Image courtesy MTT/Renishaw. |
More Metal Methods
UK-based MTT Technologies is known for its broad range of vacuum-casting, tooling, molding and selective laser melting systems. In April 2011, parent company MTT Investments announced its acquisition by Renishaw, a global engineering company with products in metrology, medical CAD/CAM and optical spectroscopy products.
This broader corporate backing should help spread the use of the MTT SLM125 and 250 machines, both of which can process titanium, stainless steel, cobalt chrome and tool steel powders into fully dense parts. MTT/Renishaw has sold systems to several U.S. companies, and is currently looking here for additional demonstration partners.
Two other metal-oriented companies with laser-based systems are POM Group and Optomec. Their processes and applications take metal powders into somewhat different and innovative directions, such as repairing worn or damaged expensive metal parts (including tooling). Both companies have developed technologies that fuse new layers of metal onto the surface of existing steel, titanium and nickel parts. The concept has been used to repair turbine blades, and even applies to reworking new parts that display out-of-spec dimensions.
POM Group’s Direct Metal Deposition (DMD) 105D and Robotic DMD systems employ a fiber-coupled diode- or disc-laser to solidify injected metal powders, even combining metals for unique alloy properties. Typical markets include both part repair and the creation of conformal-cooling within injection molds. The company’s closed-loop feedback system is the key for producing a near-net-shape product, including the capability to vary the melt-pool temperature to manage dissimilar substrates. An unusual aspect of the Robotic DMD unit is its portability, allowing machine transport for in situ repairs of massive tooling.
Up-and-Coming Rapid Metal Developments At press time, various state-of-the-art commercial programs were being discussed at the Additive Manufacturing International Conference at Loughborough University (AM-Conference.com). A number of companies and industrial groups that participated also support metal-based efforts that deserve a close look. Check out the following:
|
Optomec developed the Laser Engineered Net Shaping (LENS) technology that uses a high-power laser (500W to 4kW) to fuse a stream of powdered metals into fully dense parts. Working with such commercially available powders as 316 stainless steel, Inconel 625 and Ti6Al4V titanium, the company says its LENS-made parts feature a microstructure that improves their mechanical properties over similar parts made on other AM systems.
As food for thought, if you’re willing to look abroad in your search, three additional European companies with laser/metal-powder systems are Phenix Systems in France and 3D-MICROMAC and Concept Laser in Germany. At press time, no U.S. distributors were listed on their websites.
The Ex One Co. may be the biggest U.S. rapid tech company you’ve never heard of. With 85% of its business in Europe—and much of it conducted through a service bureau program—Ex One comprises four divisions, including the industrial group ProMetal and its subdivision, Metaltec Innovations, which offers decorative hardware, tiles and art.
Ex One’s powder-based process goes back to the early days of MIT’s technology transfer program, when the company secured the license to use MIT’s 3D Printing process with metals. Using a spray binder to form and combine layers of powdered metal, the ProMetal R-1 Direct Metal R&D Printer lets users create some of the largest parts in the rapid tech industry. Currently offered metals include a stainless-steel-bronze alloy, a high noble gold, copper tungsten and nickel. Printed parts are heat-treated to achieve final density.
Variations on a Theme
Additive manufacturing via fused powdered metals, whatever the system used, presents challenges and trade-offs. Product designers and engineers should still consider two other approaches that put a twist on traditional metalworking: systems from Roland DGA and Solidica.
![]() Detail of hip-socket acetabular cup produced on a 3D Systems Sinterstation Pro SLM system. Image courtesy 3D Systems. |
Roland DGA takes classic subtractive machining operations and packages them into a full software/hardware solution that the company describes as combining the ease-of-use of 3D printers with the benefits of CNC-machined parts. No G-code (the common language for CNC programming) is required; tolerances and surface finish are excellent, and the Roland MDX 540 series handles machining standard materials from plastics to metals—including standard types of brass, aluminum and copper. The Roland website lists extensive data (under milling products), showing favorable ownership costs compared to those for a typical 3D AM system.
Solidica offers a very different approach to building parts. It uses an ultrasonic process to “consolidate” thin layers of metal drawn from featureless foil stock. The process produces true metallurgical bonds with full density, and can work with dissimilar metals. Solidica’s Formation machine combines additive and subtractive processing to create deep slots, hollow, latticed or honeycombed internal structures and other complex geometries. The approach even allows embedding fibers and active devices such as sensors and other electronics.
Rapid Service Bureaus
Designers considering metal part production, either one-off or production, should consider outsourcing to service bureaus that work with AM systems day-in and day-out. A sampling of companies with extensive metal-working experience includes Accelerated Technologies (now part of 3D Systems), Grow It 3D, Harvest Technologies, Integra, Morris Technologies, Scicon Technologies and Solid Concepts. Two good directories for additional service bureaus are listed at Additive3D.com and TenLinks.com. Working with these experts also serves as a great entry path to identifying which system you’ll purchase down the road.
![]() An overview of multiple parts milled on Roland MDX-540 during a two-week period at Cardiovascular Systems, Inc., a medical device company. Images courtesy Roland DGA and Cardiovascular Systems, Inc. |
Fabrication Considerations
No discussion of rapid metal-part production would be complete without mention of the impact that AM has had on casting techniques—and more specifically, on mold-making. The field widens to include quite a few more companies whose systems create parts useful as either direct, reusable injection molds (made of plastics or ceramics) or as intricate models for one-of-a-kind, lost-wax casting.
Depending on the surface finish you require, you may find the perfect match for these applications with equipment from 3D Systems, Envisiontec, ExOne, Objet Geometries, Sintermask Technologies, Stratasys (especially with its recent acquisition of Solidscape) and Z Corporation. The dental and jewelry businesses are extensively tapping AM systems for fast, cost-effective, custom-volume manufacturing, but automotive, aerospace and art customers are coming on strong, too.
This is a great time to investigate metal options. See what rapid metal technology can do to transform your business.
Contributing Editor Pamela Waterman, DE’s simulation expert, is an electrical engineer and freelance technical writer based in Arizona. You can send her e-mail to [email protected].
For More Information:
3D-MICROMAC
3D Systems
Accelerated Technologies
Arcam
Concept Laser
Envisiontec
EOS
ExOne
Grow It 3D
Harvest Technologies
Integra
Morris Technologies
Objet Geometries
Optomec
Phenix Systems
POM Group
Renishaw (MTT Technologies)
Roland DGA
Scicon Technologies
Sintermask Technologies
Solid Concepts
Solidica
Stratasys (Solidscape)
Z Corporation
Subscribe to our FREE magazine,
FREE email newsletters or both!Latest News
About the Author

Pamela Waterman worked as Digital Engineering’s contributing editor for two decades. Contact her via .(JavaScript must be enabled to view this email address).
Follow DE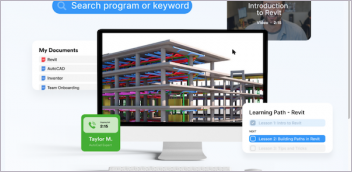

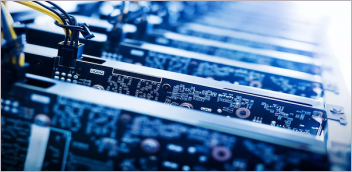
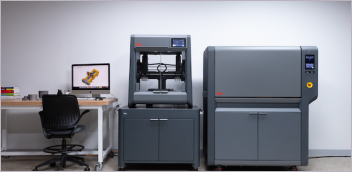