MAXOS Noncontact Measurement System Reduces Inspection Time by 83 Percent
Inspecting and measuring steam turbine blades got quicker, easier and more accurate using the MAXOS system.
Latest News
September 11, 2008
By DE Editors
![]() The MAXOS uses five axes to reach every point on the blades and also generates specific and accurate measurements of critical areas. |
The MAXOS non-contact measurement system from Steintek GmbH (Greding, Germany) and their distributor NVision Inc. (Southlake, TX and Wixom, MI) has reduced the time it takes for Toshiba GE Turbine Components (TGTC) to inspect and measure steam turbine blades from 280 minutes to 45 minutes. The MAXOS uses five axes to reach every point on the blades and also generates specific and accurate measurements of critical areas. The resulting measurements are reported immediately, eliminating the need for additional manual inspection. In the past, a coordinate measuring machine (CMM) was to inspect the blades but was found to be slow and unable to access hard-to-reach areas such as dovetail hooks and fillets.
TGTC reported that the MAXOS optical scanner integrates easily with their engineering and production processes and eliminates the need for matt coating.
TGTC is actually a joint venture between Toshiba and General Electric to produce large blades ranging in size from 26-52 inches (660 to 1320 mm) for steam turbines at cutting-edge manufacturing facilities. The equivalent of eight to ten gigawatts of electricity can be generated by TGTC’s annual production of these blades.
For more information, visit Steintek GmbH or NVision, Inc.
Sources: Press materials received from the company and additional information gleaned from the company’s website.
Subscribe to our FREE magazine,
FREE email newsletters or both!Latest News
About the Author

DE’s editors contribute news and new product announcements to Digital Engineering.
Press releases may be sent to them via [email protected].
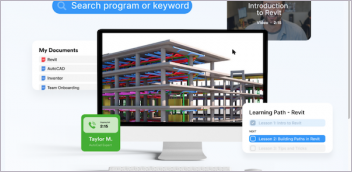

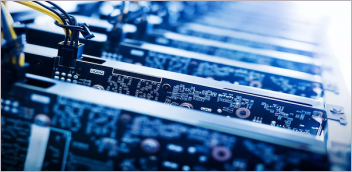
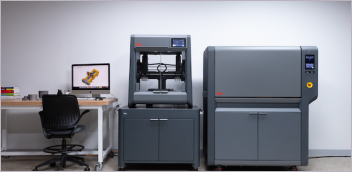