Markforged and MSC Software Pursue Partnership
In other MSC Software news, the company unveiled at Formnext 2019 its MSC Apex Generative Design, a new design optimization solution.

MSC Apex Generative Design is designed specifically to generate the detailed and highly complex structures that only additive processes can manufacture. Image courtesy of MSC Software.
Latest News
November 21, 2019
Markforged and MSC Software Corporation (MSC) announced a technology partnership to deliver process simulation, performance modeling and material analysis tools for Markforged 3D printers.
Customers can already implement material analysis for the Markforged continuous carbon fiber and Onyx materials within MSC’s Digimat materials modeling software, and the cooperation will soon extend to provide full-process simulation and part performance with Finite Element Analysis (FEA) within a common CAE environment.
“Markforged is a pioneer in the 3D printing space, and its continuous carbon fiber material is so strong, it’s replacing aluminium in factories across the globe,” says Olivier Lietaer, business development engineer for Additive Manufacturing at e-Xstream Engineering, part of MSC. “This shift in design and manufacturing requires new analysis capabilities that can validate customer designs with the same confidence as traditionally manufactured parts. Together, Markforged and MSC enable customers to guarantee the performance of a part from its material properties through to final part strength and weight.”
Partnership Features
- Material Engineering—MSC and Markforged clients can access digital material cards that capture the mechanical and material properties of Markforged’s continuous fibers and chopped fiber-filled plastics.
- Process Simulation—Clients will be able to model 3D printing within the MSC software. They will also be able to establish print calibration standards, ensure each machine is optimized for the part,= and make sure each part is printed accurately the first time.
- Part Performance—Customers will be able to connect the Markforged material and print information with FEA simulation from MSC. They can run simulations on proposed designs containing continuous fibers and printed thermoform plastics to predict the parts’ mechanical and structural performance.
“We’re thrilled to work with a leading provider of composite modeling and simulation software to provide this service to our customers. MSC’s best-in-class composites FEA will be critical in helping our customers identify the right design for their carbon fiber parts,” says Jon Reilly, VP of Product, Markforged. “3D printing is transforming the factory floor, and with MSC as our partner, we can ensure all parts made with Markforged will perform at their peak potential.”
In other MSC Software news, the company unveiled at Formnext 2019 its MSC Apex Generative Design, a new design optimization solution that aims to improve quality through automation of design processes with embedded manufacturing knowledge.
MSC Apex Generative Design software produces a part design that is ready for additive manufacturing (DfAM) within a few hours—a fraction of time usually required.
Re-thought Design Optimization
In MSC Apex Generative Design, the designer only needs to specify the boundary conditions and design objective. Multiple lightweight design candidates that explore the possibilities of the design space will be produced that provide optimal stress distribution and minimize weight. The software's intelligent smoothing technology ensures that every candidate has a finish that is ready for print.
“New design freedoms in additive manufacturing require a new generation of software solutions that take full advantage of the new DfAM possibilities. We make the generative design process smarter by producing design candidates that both satisfy the engineering criteria and look as the designer intended when 3D printed,” says Dr. Thomas Reiher, director of Generative Design.
Fully Integrated Design Optimization Process
Conventional topology optimization workflows require manual work and multiple tools to achieve production-ready results. MSC Apex integrates all relevant steps within one computer-aided engineering (CAE) environment to improve productivity with a single user experience from design to additive manufacturing preparation.
The design process is workflow-oriented, providing easy and fast model setup from existing geometries or mesh in common CAD, STL or MSC Nastran BDF formats. Designers can find optimized design candidates and perform design validation within the same CAE environment, simplifying the work process and reducing design iterations. The result is a fully integrated, automated optimization process.
Validated for Additive Manufacturing
The MSC Apex Generative Design for Additive Manufacturing solution combines print-ready geometries with metal (Simufact) and polymer (Digimat) build process simulation from Hexagon's additive manufacturing portfolio. Designers only generate part designs that can be manufactured using their chosen material and print process to eliminate costly prototyping.
MSC Apex Generative Design is available now. Learn more here.
Sources: Press materials received from the company and additional information gleaned from the company’s website.
More Hexagon MSC Software Coverage
More Markforged Coverage
Subscribe to our FREE magazine,
FREE email newsletters or both!Latest News
About the Author

DE’s editors contribute news and new product announcements to Digital Engineering.
Press releases may be sent to them via [email protected].
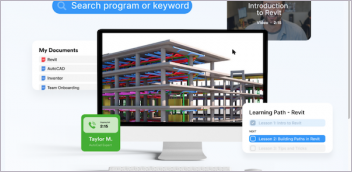

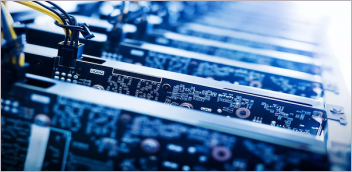
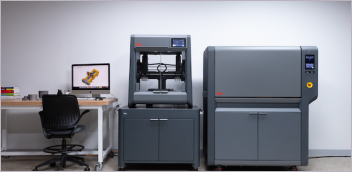