MapleSim Handles Multidomain Modeling & Simulation
Model diagrams look real using Maplesoft's new modeling and simulation tool.
Latest News
January 21, 2009
By Margaret S. Gurney
![]() The Foucault Pendulum, modeled here in MapleSim, is used to demonstrate the Earth’s rotation. |
Maplesoft says its new high-performance multidomain modeling and simulation tool, MapleSim, will revolutionize how new products are brought to market. By combining its symbolic computing engine with traditional numeric solvers, model creation time and associated costs are reduced in the simulation and modeling process.
The company says that MapleSim, after months of pilot testing and feedback from approximately 1500 organizations spanning 85 countries, is ready for engineers to shorten their product development cycle with increased efficiency. Plus, MapleSim brings its symbolic computing engine to the mix. With the Maple computation engine at its core to provide the automatic generation of equations, model simplification, and analysis tools, considerable efficiency is gained in the design process, according to the company.
“With MapleSim, users can simply re-create a system diagram on a screen and the equations of the model are automatically generated. With savings of anywhere from weeks to months, MapleSim marks the beginning of a new era.” — Jim Cooper, Maplesoft, CEO and president |
MapleSim applies symbolic preprocessing techniques to model equations, creating simplified and highly efficient models. Code generated from these simplified models can be exported to real-time applications as well as other applications. Because of the symbolic preprocessing, this code runs 10 to 100 times faster for complex models, says the company.
“In MapleSim, the world’s most advanced symbolic computing engine — Maple — comes together with traditional numeric solvers to supercharge the simulation and modeling process,” says Jim Cooper, Maplesoft’s CEO and president. “With traditional techniques, modeling even simple systems is arduous and time consuming; with MapleSim, users can simply re-create a system diagram on a screen and the equations of the model are automatically generated. With savings of anywhere from weeks to months, MapleSim marks the beginning of a new era,” he adds.
![]() A model of a 3D Pendulum created using MapleSim’s multibody components. |
Physical Modeling
Maplesoft says that MapleSim offers numerous advantages over traditional tools. It allows users to mix physical components with traditional signal-flow blocks, making the model diagram look like the real system being modeled.
Multidomain models are easily assembled from pre-built components and units management removes potential errors in conversion and consistency. Plus, live design documentation captures the analysis behind the model because systems of equations representing the model are automatically generated. Complex models are automatically simplified using symbolic techniques the company describes as sophisticated.
With MapleSim, you recreate the system diagram on your screen using components that represent the physical model — you don’t have to translate your design into equations and manipulate them into signal-flow block diagrams. You’ll notice that components look the same as if you drew them by hand, says the company, plus the easy and intuitive model creation speeds up model entry. The model validation takes less time because the model so closely resembles the system diagram.
|
System equations are generated automatically. Since MapleSim is built on Maple, the same powerful symbolic computation abilities are at its core. Unlike purely numeric calculations, symbolic technology has the ability to directly convert a physical system representation to mathematical equations.
Analysis
Natural multidomain modeling is easily assembled from pre-built components. MapleSim ships with more than 300 components from more than 10 domains, including continuous and discrete signals; rotational and translational mechanics; analog, digital, and multiphase electric circuits; and more. It uses standard symbols and notation, making it easy to find the components you need. It also lets you mix traditional signal-flow blocks with physical components and easily design controller and physical models in one environment.
Plus, the company says MapleSim’s model design and analysis offer dynamic analysis, control design, and optimization tools; easy creation of custom components; advanced units management; and live design documentation.
The Math Engine
In addition to physical modeling being faster and more intuitive, MapleSim builds on Maple’s extensive numeric and symbolic computational abilities — garnered from more than 20 years of R&D — to perform high-speed simulations of very complex models. Features such as equation generation, symbolic simplification, and units management are all possible using the Maple mathematical engine.
MapleSim capabilities provided by Maple include elimination of redundant equations, separation of independent systems, large-scale symbolic simplification, efficient equation management, application of hybrid numeric-symbolic algorithms, and advanced high-index DAE solving.
With physical modeling techniques in MapleSim, users can recreate a system diagram on a screen using compact and intuitive components that represent a physical model, making it easier to build and understand. MapleSim has components for electrical, mechanical, control design, and thermal, organized into easy-to-navigate palettes.
In addition, many components in MapleSim are from the Modelica Standard Library. Single user professional licenses of MapleSim are available for $2,995. Volume and academic discounts apply.
Read more about MapleSim.
Read why DE’s editors chose this as a Pick of the Week.
Evaluate MapleSim.
See a demo on MapleSim.
View the MapleSim movie.
Access Maplesoft’s International Sales and Support.
Margaret S. Gurney is new products editor at Desktop Engineering.
Subscribe to our FREE magazine,
FREE email newsletters or both!Latest News
About the Author

DE’s editors contribute news and new product announcements to Digital Engineering.
Press releases may be sent to them via [email protected].
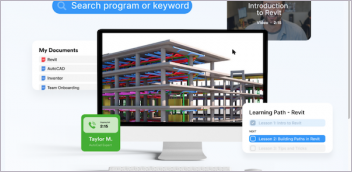

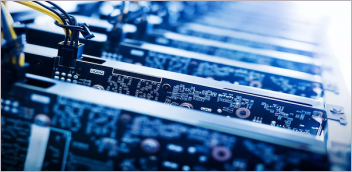
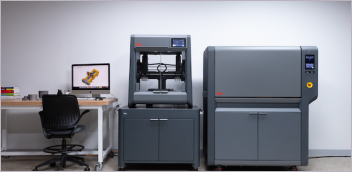