Lightweighting and Topology Optimization Roundtable: Audience Questions and Panelist Answers

This Airbus partition is conceived using custom algorithms that generate cellular structures and bones. The structure is stronger and more light-weight than would be possible using traditional processes, according to the joint announcement by Autodesk and Airbus (image courtesy of Autodesk).
Latest News
January 29, 2016

Last week, I moderated a roundtable talk on topology optimization and lightweighting, part of the DE webcast series. (The recorded webcast is now available online. To listen, please press the button below.)
The panelists were:
- Keith Meintjes, Practice Manager, Simulation and Analysis, CIMdata
- Andreas Vlahinos, Principal, Advanced Engineering Solutions
- Alan Taub, Chief Technology Officer, LIFT
To set the scope and define the term, Keith Meintjes said, “The best way to think of topology optimization is as a layer placed on top of finite element analysis (FEA). One of the variables in FEA is material density. So the [topology optimization algorithm] helps you decide where materials need to be added, where it can be removed.”
The desire to remove every excess gram from the vehicle is prompted not just by profit margins and fuel economy. Alan Taub pointed out, “Weight is also responsible for the performance of the vehicle. Weight distribution drives rollover tendencies and handling. The lighter the car, the easier it is for the vehicle dynamics engineer to tune the ride and handling.”
Keith said, “The topology optimization software is not easy to use, so you need an FEA expert. The sculpted surfaces that come out of the optimization is difficult to interpret, so you need a freeform CAD surfacing expert. You also need someone who understands the product requirements—loads, stresses, and so on. And you also need someone who understands manufacturing requirements.” To assemble four such experts from four different parts of an organization is, Keith added, “a very big deal.”
Along the same line, Alan Taub said, “It’s one thing to say the manufacturing engineer is there. But true concurrent engineering means meshing the topology optimization code with the manufacturing code. From my perspective, that’s one of the hardest challenges to take on.”
The so-called optimized shapes are algorithm-driven; therefore, they often include jagged edges, vine-line structures, and asymmetrical features that cannot be made in standard manufacturing methods. Some look to additive manufacturing—especially metal-based 3D printing—as a way to overcome the hurdle.
Andreas Vlahinos, who has been closely watching the trend, predicted that in the future, when optimization software are capable of generating optimized lattice structures, “We will have a portion of the design in lattice structure, a portion in solids, all covered in skin”—the best of both worlds for lightweighting. He observed, “In the past, we were able to design parts we couldn’t produce; now, we have parts that we could make, but cannot design in the CAD system.”
We also collected a number of questions from the audience who tuned in. Here are the panelists’ responses to them, along with mine.
Q: I´d like to know why every topology optimization presentation just exposes Altair’s OptiStruct? Why not other tools?
- Andreas’ reply: I exposed not only OptiStruct from Altair but the following codes: TOSCA from Dassault Systèmes; Genesis from VRAND; ProTop from CAESS that runs within PTC CREO; and GTAM from VRAND that runs within ANSYS.
- Keith’s reply: It just so happens that I was customer 1 for OptiStruct when I was at GM Powertrain in the 1990s. In terms of usability, I would point now to Altair SolidThinking Inspire, and to Autodesk’s efforts to embed this technology in their design tools.
- Kenneth’s reply: Though not mentioned during our discussion by name, I have covered optimization technologies from Autodesk. Autodesk Shape Generator is a CAD-embedded optimization solution; Autodesk Within is intended for optimizing lattice structures.
- Andreas’ reply: The aerospace and automotive industries are using it routinely. It has not been widely used since the generated shapes are hard to manufacture. The 3D printing is a game-changing technology that will increase the topology optimization usage.
- Keith’s reply: I think it is lack of understanding on the side of the users, and lack of effort on the side of the software providers. The software is just too difficult to use.
- Andreas’ reply: Yes, ProTop from CAESS adds and subtracts material to and from lattice structures.
- Keith’s reply: That is what “shape optimization” (as opposed to “topology optimization”) is supposed to do. I would look to VR&D Genesis and Altair for this technology. MSC is a pioneer of this technology, but seems to have been unable to exploit it.
- Kenneth’s reply: While Autodesk Shape Generator primarily works by removing materials, Autodesk Within optimizes structures by growing membrane- or vine-like geometry where the design needs reinforcement.
- Andreas’ reply: The benefits of topology optimization have been harvested by the sheet metal manufacturing and recently by the Additive Layer Manufacturing
- Keith’s reply: Yes, optimization can benefit from any understanding of the manufacturing process. 3D printing has its own constraints.
- Andreas’ reply: There are a lot of efforts underway to used other physics in topology optimization. An example is TOSCA flow.
- Keith’s reply: They should be coupled.
- Andreas’ reply: In my personal opinion Genesis from VRAND is the best since it has manufacturing constraints and coupled size optimization.
- Keith’s reply: Best technology? Dassault TOSCA. Most usable? Altair SolidThinking Inspire.
Subscribe to our FREE magazine,
FREE email newsletters or both!Latest News
About the Author

Kenneth Wong is Digital Engineering’s resident blogger and senior editor. Email him at [email protected] or share your thoughts on this article at digitaleng.news/facebook.
Follow DE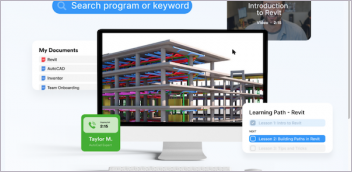

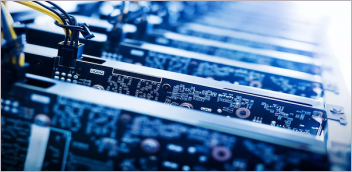
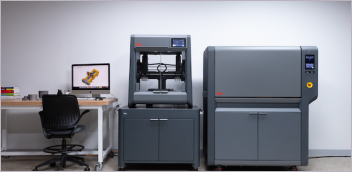