Lessons From the Titan
Simulation, testing and rapid prototyping aren’t enough—you need processes (and regulations) in place so that when engineers raise a red flag, those in charge have to listen and respond.
Latest News
August 25, 2023
When the OceanGate Titan submersible went missing (and as it turned out, imploded, killing all aboard) on a dive to visit the wreck of the Titanic, I just happened to be in Belfast, Ireland, visiting the Titanic museum. The museum is located at the shipyard where the Titanic was actually built, and exhibits focus as much on its construction as its eventual sinking in the North Atlantic.
The Titan accident, and my visit to Belfast, got me thinking about what lessons we can take from these tragedies a century apart.
The Titanic sank after famously running into an iceberg, but the impact itself was not the sole cause. The type of hull steel used at the time was susceptible to brittle fracture—on impact. Instead of deforming (like modern steel), it shattered like ceramic due to a combination of velocity, temperature and chemistry. There was also a design flaw (the height of the walls in the lower level watertight compartments) that accelerated the disaster once the hull was breached.
Like the Titanic, the Titan also appears to have suffered from materials issues and design troubles. There have been numerous articles about the design of the craft, criticizing everything from its off-the-shelf electronics to its shape (cylindrical, not spherical), and the epoxy joining the hull to the frame.
There were also concerns raised about the use of carbon fiber in the construction of the Titan, as opposed to the combination of steel and titanium that were used in other such craft, such as the Deepsea Challenger (the submersible used by filmmaker James Cameron to explore the wreck site).
At the depth of the wreckage of the Titanic, the submersible would have been under some 6,000 pounds of pressure. The repeated dives the vessel had already undertaken could have potentially weakened the hull. Carbon fiber is great for aerospace structures, but not really meant for applications with this type of external pressure.
There is also plenty of evidence that OceanGate knew about these risks and concerns, and simply pushed on ahead anyway. (You can read a good accounting in The New Yorker.) It wouldn’t be the first time a company chose expediency over safety. We have written about this issue before, and even dedicated a cover story to it in 2019 in the wake of fatal Boeing 737 Max crashes. Design flaws that cause these types of tragedies are rarely a surprise to engineers; in many cases, though, their warnings go unheeded.
We are in an age now where technology advancements make it possible to rapidly design, test and construct cars, aircraft, marine vessels and spacecraft at a much more rapid pace. This has also allowed entrepreneurs and billionaire technologists to pour a lot of money into superyachts, advanced race cars, rockets and deep-sea submersibles for their own personal use and to build new businesses around things like space tourism.
But when I think of people building private fleets of submarines and rocket ships, I don’t think of great innovators and explorers; the first people who come to mind are usually James Bond villains. And while I don’t think our current crop of tech billionaires share their villainy, they might suffer from a touch of their hubris.
That’s why advanced simulation, testing and rapid prototyping aren’t enough. You need processes (and regulations) in place so that when engineers raise a red flag, the people in charge have to listen and respond. Ambition and optimism can carry a project a long way, into the outer reaches of the atmosphere and the deepest parts of the ocean, but they cannot carry you past the laws of physics.
Subscribe to our FREE magazine,
FREE email newsletters or both!Latest News
About the Author

Brian Albright is the editorial director of Digital Engineering. Contact him at [email protected].
Follow DE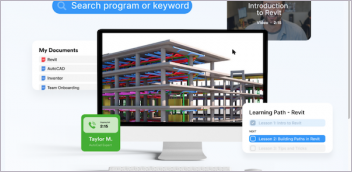

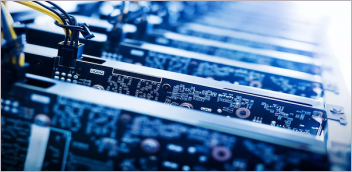
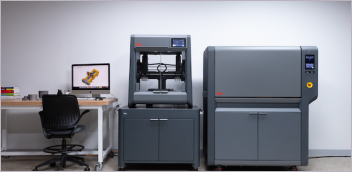