How to Validate Machines With Virtual Simulation and Commissioning
The need for high-level customization with superior machine complexity drives manufacturers to support a global machine design to implement manufacturing strategies.

Latest News
November 5, 2021
Industrial machinery end-customers want customized products delivered quickly. To meet this demand requires sophisticated machine designs. The need for high-level customization with superior machine complexity drives manufacturers to support a global machine design to implement manufacturing strategies. In addition, manufacturers can enhance their machine validating process with technological innovations like virtual simulation and commissioning to address complex customer demands efficiently.
Defining Virtual Simulation and Commissioning
Virtual machine simulation and commissioning is the process of validating the software code (PLC/HMI/SCADA) in the virtual world before it deploys on the factory floor. As software drives machines, it becomes even more complex. Therefore, it is essential to simulate the code running on a machine's virtual twin to generate substantial dividends in time and resources. Virtual simulation and commissioning validate the PLC (programmable logic controller) software in a managed environment, an integral part of the modular product development strategy. Then machine builders can perform the simulation upfront and link the software to the modules, merging the final code seamlessly on an individual customer-specific machine.
Many software integrations and safety factors are essential to run a machine, so a customer must test it physically. Accordingly, virtual simulation and commissioning are ideal for turning a machine on and performing real commissioning. Then there is significantly less pressure for the machine builder and its customers. In addition, this process collaborates the engineering upfront in the design process to further reinforce the interdependency of all virtual simulation and commissioning disciplines.
Virtual Simulation and Commissioning Essentials
Critical elements of the virtual simulation and commissioning process include the following:
- Upfront automation is linked to machine behavior—Virtual simulation and commissioning begin with a vision of the desired machine behavior and the sequence of operation. Preferably, a systems model defines the machine behavior in electrical and fluid domains. In addition, physics-based kinematic model introduces forces on sliding or rotating components at various times, providing an outstanding visualization tool to communicate between the mechanical, electrical and control engineers.
- Behavior model drives code generation—The machine behavior model, which is a physical demonstration of the machine operation sequence, identifies the logical devices in the design attributes essential to the PLC and HMI (human-machine interface) code development. For example, suppose we have a motor with an integral encoder. In that case, the visual behavior model describes a process in which the motor is energized for a particular number of rotations, stops and reverses. Thus, the PLC code must know essential information about the motor or encoder and the expectations for application use.
- Closed-loop feedback visualization—The upfront simulation of the desired machine behavior is only valuable when validated after the finished code loads into a virtual PLC, showing machine operation in the digital twin when driven by the code, not the predictive machine behavior model.
- User experience implementation—The user experience conveys how the digital twin demonstrates the machine's response to user-initiated commands—indicating that the operating parameters display appropriately on the HMI and whether the touchscreen and other interface devices operate correctly. Similarly, the virtual machine must respond correctly during an e-stop or normal shut-down and simulate faults and other use cases where safety is crucial.
Virtual Simulation and Commissioning Benefits and Challenges
These essential processes foster an environment that results in considerable benefits. Consequently, the demand for virtual simulation and commissioning, in combination with the digital twin, provides substantial advantages:
- Compressing time: Caters to customers that continually make changes, driving a reciprocal need to respond rapidly
- Saving costs: Reduces time to physically debug the design and its associated controls
- Minimizing risk: Provides virtual testing, so evolutions present theoretical issues with no PLC program issues
Additionally, virtual simulation and commissioning benefits create outstanding efficiency on the shop floor to achieve higher speeds and excellent reliability—a 20% improvement in machine shop or operations capacity. This efficiency saves valuable time previously spent in physical validation, verification and commissioning.
However, the positive aspects of innovative technologies come with their accompanying challenges, including validating third-party equipment integration, which requires the need to bring disparate systems and code together cohesively. Secondly, robotic integrations require connecting that code into the PLC for better efficiency. Lastly, logistics automationprovides substantial proficiency by orchestrating multiple interfaces simultaneously.
Many use cases detail the benefits of virtual simulation and commissioning. As a result, some noteworthy companies are witnessing notable improvements.
Virtual Simulation and Commissioning Use Cases
Tronrud Engineering develops, manufactures and supplies innovative machines and equipment to users. Using a new machine's digital twin allows the designers, engineers and programmers to work concurrently while continuously sharing their knowledge. This process substantially compresses commissioning and engineering time.
“By working on the design, mechanical components and programming simultaneously, we can drastically reduce the time to market. In another project, this approach allowed us to save about 20 percent or two months,” says Erik Hjertaas, General Manager Packaging Technology at Tronrud Engineering.
In response to the parallel execution of development steps in an interdisciplinary team, Tor Morten Stadum, PLM Manager at Tronrud Engineering, states, “We shortened the design phase by about 10 percent and commissioning by 20 to 25 percent.”
Also, Eisenmann, a leading global provider of industrial solutions in southern Germany, plans and builds made-to-measure manufacturing, assembly and enterprises worldwide. They have deployed highly flexible distribution plants that are energy- and resource-efficient for more than 65 years. Also, they’re gaining the benefits of virtual modeling, simulation and commissioning.
“The simulation model we create with Plant Simulation is often part of the deliverable to our customers. Many of them also use Plant Simulation themselves, so they know how to run the simulation and change the needed parameters. This is a big benefit for them because they get a virtual model of the physical line,” says Dr. Heiner Träuble, Simulation Expert Automotive Paint Systems Eisenmann.
“We are very pleased with the discrete event simulation capabilities we have developed in Eisenmann throughout the years, especially our use of Plant Simulation,” says Sebastiano Sardo, Senior Vice President, Eisenmann Conveyor Systems.
Software to Adapt Machines for the Future
Using the Xcelerator portfolio, a suite of services from Siemens Digital Industries Software Solutions helps manufacturers create a comprehensive digital twin. It also integrates simulation within the machine design to be flexible, capable and adaptable. Connected machines, which can communicate with other machines, extend their capabilities through software-driven changes. This value is essential for modern manufacturers to maximize the productivity of the end-user environment.
Companies need a digital solution that crosses all aspects of a machine manufacturer’s product and production process to connect, adapt, predict and extend the machines of tomorrow, today.
About the Author:
Rahul Garg is the Vice President for Industrial Machinery & SMB Program, responsible for defining and delivering key strategic initiatives and solutions and global business development. He and his team are responsible for identifying key initiatives and developing solutions for the industry while working closely with industry leading customers and providing thought leadership on new and emerging issues faced by the machinery industry. Rahul’s experience and insight are derived from 25-year career delivering software-based solutions for product engineering and manufacturing innovation for the global manufacturing industry, spanning a career in R&D to program management, sales and P&L management and having focused exclusively on the industrial machinery and heavy equipment industry since 2007.
More Siemens Digital Industries Software Coverage
Subscribe to our FREE magazine,
FREE email newsletters or both!Latest News
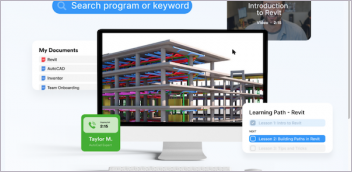

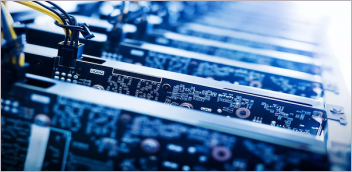
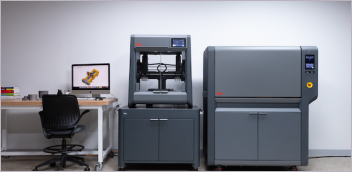