High-Performance Concept Car Uses 3D Printed Components
TAFNEX CF/PP and 3D-printed components developed by the Mitsui Chemicals Group find application in Toyota Fortuner-based car designed by TCD ASIA.

TAFNEX CF/PP and 3D-printed components find application in the TOYOTA Hyper-F CONCEPT. Image courtesy of Business Wire.
June 26, 2024
Materials developed by Mitsui Chemicals and subsidiary ARRK Corp. have been used in a high-performance concept car based on the Toyota Fortuner. Direct pellet-fed 3D-printed components jointly developed by Mitsui Chemicals and ARRK, and TAFNEX CF/PP*2 —a unidirectional carbon fiber-reinforced polypropylene resin sheet developed by Mitsui Chemicals‚ have found application in the TOYOTA Hyper-F CONCEPT, which has been designed by TCD ASIA Co.
TAFNEX CF/PP and the newly developed direct pellet-fed 3D-printed components will be exhibited at Bangkok Auto Salon 2024, a custom car show taking place in the Thai capital June 26–30, and at Bangsaen Grand Prix 2024, a car race that will be held on the outskirts of Bangkok July 3–7.
The TOYOTA Hyper-F CONCEPT is a high-performance concept model with a styling design that incorporates the road handling and aerodynamic performance cultivated in the racing field by TCD ASIA’s motorsport business. The new materials have enabled the company to reduce the concept car’s weight.
TAFNEX CF/PP has been used for decorative components on part of the front bumper and the hood air vents, while the direct pellet-fed 3D-printed components are fitted to the hood air duct bezels.
In 2020, Mitsui Chemicals launched an investment and business alliance with Dreams Design Corp., an engineering service provider focused on automobile development. Then, in 2023, Mitsui Chemicals embarked on a similar investment and business alliance with ExtraBold Inc., a manufacturer of direct pellet-fed 3D printers.
The 3D-printed components fitted to the concept car bring together the auto part design technology of Dreams Design and ExtraBold’s EXF-12 3D printer, which delivers high-speed printing of large parts; the 3D printing and post-processing technologies of ARRK, one of Japan’s largest product development support companies in this industry, offering everything from prototyping to mass production; and the polyolefin-based composite technology being developed by Mitsui Chemicals for use in 3D printing.
Applying mechanisms used in injection molding, direct pellet-fed 3D printers form structures directly from plastic pellets. The advantage of this approach over conventional 3D printers is a stable increase in the quantity of plastic discharged, enabling large structures to be formed quickly. When used in the high-mix, low-volume mass production of 3D-printed items, the moldless technique helps to reduce development lead times and the initial investment required, including mold costs. In addition, the technology is expected to contribute to the circular economy, as the 3D-printed items can be crushed into pellets and recycled as raw materials for further 3D printing.
TAFNEX CF/PP is a unidirectional tape (UD tape) made from a carbon fiber (CF) and polypropylene (PP) composite using Mitsui Chemicals’ technologies. As well as being lightweight and highly rigid with good moldability, it has features that can be altered to suit a range of designs, such as marble-like patterns. TAFNEX is designed to be adapted for use in automobiles and drones, along with a range of other applications in the industrial and consumer sectors. Such applications include local reinforcement of injected or pressed molded parts, and the material can also be processed into parts in the form of tubes or laminated sheets.
Sources: Press materials received from the company and additional information gleaned from the company’s website.
Subscribe to our FREE magazine,
FREE email newsletters or both!About the Author

DE’s editors contribute news and new product announcements to Digital Engineering.
Press releases may be sent to them via [email protected].
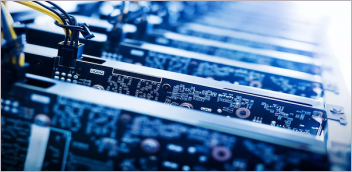
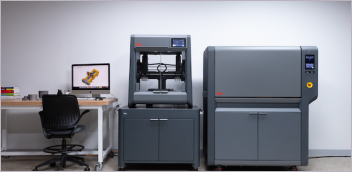
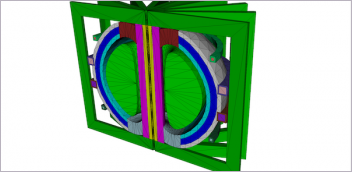
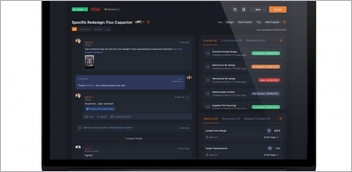