Formlabs Introduces Form 4 Resin 3D Printer
Form 4 and its biocompatible version, Form 4B, represent the next advances in stereolithography (SLA) 3D printing technology, Formlabs reports.

This large airflow test snout was printed in Grey Resin V5 on Form 4 in two hours and 56 minutes, compared to almost nine hours on Form 3+. Image courtesy of Formlabs.
Latest News
April 17, 2024
Formlabs unveils Form 4, its next-generation resin 3D printer.
Form 4 and its biocompatible version, Form 4B, represent the next advances in stereolithography (SLA) 3D printing technology, Formlabs reports. Form 4/B delivers the majority of parts in under two 2hours, in all materials.
Form 4 combines a new print engine with updates to the Formlabs materials library—23 resins on Form 4 and 37 on Form 4B available at launch—as well as new accessories and postprocessing solutions, and an improved user experience.
The company reports that the Form 4 fabrication tool offers print speeds of up to 100 mm per hour, a 30% larger build volume, new advanced materials.
Prints on Form 4 are completed two to four times faster than with any other Form Series resin 3D printer, even for tall parts or batch printing, according to Formlabs. Form 4’s speed is driven by the new Low Force Display print engine, a combination of high-power LEDs and masking lenses that cure each layer of resin instantly—regardless of part size or quantity. Print speeds are no longer affected by how much of the build platform is covered, so multiple parts can print at once without extending your print time, Formlabs explains.
With repeatable tolerances, parts printed in every resin on Form 4 will match your design parameters, each time, Formlabs claims. Form 4’s Light Processing Unit (LPU) delivers a 50 µm XY resolution so that multi-part assemblies glide together without friction, manufacturing aids integrate into the workflow, and end-use parts match the repeatable precision of mass-produced plastics made through injection molding, Formlabs adds.
With repeatable tolerances that match initial designs, parts can remain the same through each stage of product development. Quickly printed as a mockup, functionally tested as a later-stage prototype, or produced as a stop-gap option, the appearance and performance of every part will stay the same.
For more product details, click here.
Sources: Press materials received from the company and additional information gleaned from the company’s website.
More Formlabs Coverage
Subscribe to our FREE magazine,
FREE email newsletters or both!Latest News
About the Author

DE’s editors contribute news and new product announcements to Digital Engineering.
Press releases may be sent to them via [email protected].
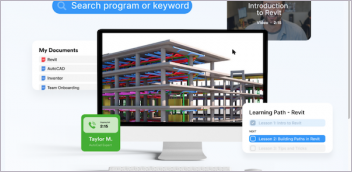

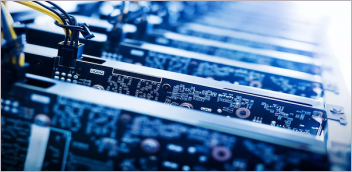
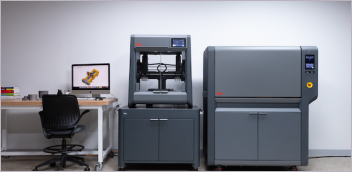