Latest News
January 2, 2018
Editor’s Note: Tony Abbey teaches both live and e-learning classes for NAFEMS. He provides FEA consulting and mentoring. Contact [email protected] for details.
The last few months of 2017 were busy. I taught live classes to Rolls-Royce in Derby, UK, at the NAFEMS aerospace event in Wichita, KS, and most recently at Autodesk University in Las Vegas, NV. I’ve also been teaching my regular e-Learning sessions. It’s nice to meet people face-to-face at the live events, and be able to talk about finite element analysis (FEA). It is surprising the topics that come up.
This month’s article is prompted by several of these conversations. Newcomers to FEA, and those wanting to polish up advanced skills, search for good examples that demonstrate specific technical areas. Two possible sources are software demonstrations, many of which are available on YouTube, and classical FEA benchmarks. However, there are some dangers in using these as best practice examples!
Software Demos
A YouTube search will reveal many demos using a variety of FEA software solutions. The objective of most of these is to demonstrate usage or techniques within the software. The problem is that, because this is the focus and time is limited, the demo may not be representing good FEA practice.
A frequent example of this occurs in demos using a simple link, for example. One end of the link is constrained, and the other end is loaded. Often, the constrained end is fully built in, all around the inside of the bearing face. The problem here is that stresses in the constrained region are extremely unrealistic. The model represents a component superglued to an infinitely rigid pin or other connection. There is often no mention of this in the example.
Similarly, the loading can be somewhat arbitrary. Demonstrations exist where the complete inside bearing face is subjected to an axial force distributed evenly over the full 360°. This implies a tensile load path across where gapping of a loaded pin would occur. It also means large tractions are being applied on surfaces tangential to the loading direction, where the real bearing pressure is zero.
The concern is that a new user will assume that that is normal engineering practice. If the presenter explains clearly that the loading is just an expedient way of providing a shortcut, then that’s OK. Otherwise, confusion will occur.
I often see assemblies frozen in place and arbitrary loading applied. If automatic bonded contact is used, then moments are created about hinge points that are unrealizable in practice. A simple free body diagram of each component would show that the boundary conditions are completely unrealistic.
Classical FEA Benchmarks
I use classical benchmarks in my own training, and many people develop them from textbooks. The motive is that if a classical solution can be emulated using FEA, then it’s a good check of the software and our analysis skills.
The problem is that many of the benchmarks are highly simplified configurations. Classical solutions are tough to produce and require very simple boundary conditions to stand any chance of being solved. They often do not represent the real world in any sense, but have interesting mathematical results that really stretch the FEA solutions.
My favorite example involves buckling of a simply supported plate under a constant end load. An elegant closed form solution predicts the critical buckling load and the center point deflection. The problem is that, for anybody carrying out an FE analysis, simply supported implies constraints in each of the three transitional directions along the edges. That immediately causes an issue as we cannot constrain the sides and loaded end axially, as the plate needs to deflect in that direction. We can overcome that by applying equal and opposite loads and a minimum constraint set, allowing the plate to shorten. If we now run the analysis, then unfortunately, we get the wrong answer compared with the classical solution.
In the classical buckling solution, the only degrees of freedom considered are the out-of-plane deflections. In-plane deflections simply do not exist in the problem. So, by constraining the plate laterally we have put in the wrong boundary conditions for the classical problem. To get the FEA solution to match the classical solution, we need to apply out-of-plane translational constraints to the periphery of the plate and apply a minimum constraint set to stop rigid body motions.
This is counterintuitive, as no real plate would ever be supported like this. The benchmark is used to achieve a mathematical solution, and the FEA can be verified against this. But that is about the limit of its practical usage.
I am currently teaching a non-linear FEA course online. I am using an example of a shallow roof that exhibits snap-through. This follows a classical benchmark and I apply a point load at the center. Throughout introductory FEA classes and all my online articles, I emphasize how we should never do this! The only reason we get away with it, in this example, is that the snap-through occurs at a low load level and the stress does not have a chance to build up to feature a significant singularity. If we were to apply an extraordinarily fine mesh, then we would see evidence of a singularity even at these low levels.
To compound the problem, the benchmark uses quarter symmetry and a 4x4 shell mesh. When the problems were first posed, this was about the limit of most FEA solvers! So, I have to turn this problem definition on its head and explain the historical background and emphasize how this is not an example of good modeling practice.
So be wary of where you get your guidance. That’s probably a familiar warning regarding anything you may find on YouTube, or the internet generally. However, it may be a bit of a surprise to find that some of our tried-and-trusted FEA benchmarks are also bad examples of engineering analysis. In defense of the benchmarks and all the extensive theoretical development behind them, they were never intended to be general engineering applications.
Subscribe to our FREE magazine,
FREE email newsletters or both!Latest News
About the Author

Tony Abbey is a consultant analyst with his own company, FETraining. He also works as training manager for NAFEMS, responsible for developing and implementing training classes, including e-learning classes. Send e-mail about this article to [email protected].
Follow DE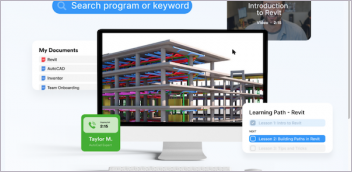

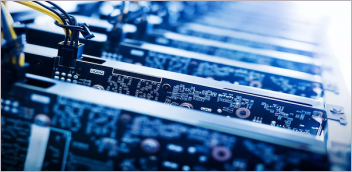
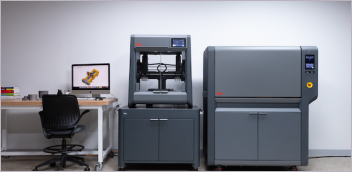