FDM Helps UCF Win Best New Design
Based on redesign of third-generation underwater vehicle.
Latest News
August 1, 2008
By Stratasys Inc.
|
Real Challenge
Each year the Association for Unmanned Vehicle Systems International (AUVSI) challenges students to design and produce underwater vehicles that operate without any human control. University of Central Florida (UCF) accepted the challenge and entered the ninth annual Autonomous Underwater Vehicle Competition. Leveraging the advantages of fused deposition modeling (FDM®), the university’s robotics laboratory manufactured “Scout” and walked away with the honor of best new design.
Scout is the third generation underwater vehicle for UCF. Building on the experience of past competitions, the team undertook a complete redesign and found that it needed an advanced tool that could make complex structures with high accuracy and mechanical strength.
UCF’s previous entry featured a flooded hull design with a vacuum molded, spherical shell. “The problem with this approach was that the spherical shape wasted a considerable amount of space and weight,” said Christopher Sprague, Universityof Central Florida Robotics Laboratory team member. “The use of vacuum molding also made it impossible to provide brackets and compartments. As a direct result, many additional components were required.”
Scout’s design features a space frame that serves as the primary structural member and provides a waterproof environment for sensitive components. The frame encloses a small amount of air while allowing water to flow through the bulk of its volume. This reduces the buoyancy of the frame and the weight needed for diving. However, the sophisticated design created manufacturing challenges.
Real Solution
“We sent the design to several machine shops but were told that the geometry was so intricate that it would be impossible or prohibitively expensive to machine it,” Sprague said. He searched for an alternative that could produce very complex geometry while providing the strength and durability needed for load-bearing parts. Sprague commented, “Direct digital manufacturing seemed to provide a promising method of producing the frame.” After further investigation, he selected the FDM process.
“The advantage of manufacturing with FDM is that you can produce components with the thermal and mechanical properties and dimensional accuracy needed for full functionality,” Sprague said. “FDM enabled us to manufacture a frame with complex geometry, from thermoplastic, in a quantity of one.”
“The FDM frame gives our craft important competitive advantages such as fewer components, lighter weight, higher strength and lower cost,” says Sprague. It was these attributes that garnered a second place in subjective judging — based on criteria such as craftsmanship and technical accomplishment — and a best new design award.
More Info:
Stratasys Inc.
7665 Commerce Way
Eden Prairie,MN 55344
T: 888.480.3548, F: 952.937.0070
[email protected]
stratasys.com
Subscribe to our FREE magazine,
FREE email newsletters or both!Latest News
About the Author

DE’s editors contribute news and new product announcements to Digital Engineering.
Press releases may be sent to them via [email protected].
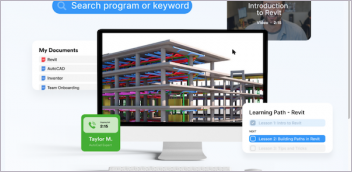

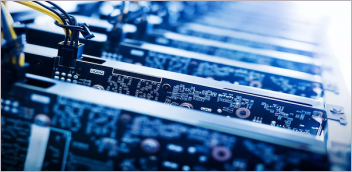
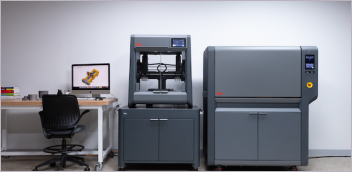