Fast App: Testing Seals with Prototyped Parts
Testing the next generation of a product can be difficult if build costs are too high or build times too long. Here's how one company created an inexpensive way to work out the kinks of their latest design.
Latest News
June 14, 2011
By DE Editors
Eric Schneider is a design engineer who took on the job of producing a generation of handheld devices for a new client. He works for Key Tech, Inc., a Baltimore consulting firm known for its clever designs of medical devices, instruments and consumer electronics. Because the company hires top engineers with various types of expertise, they are able to provide innovation to their global clients. They’ve worked on everything from climate-controlled pet carriers to spa circuit boards to devices that measure red blood cells.
A 3D CAD model of the seal test for the enclosure pieces needed for
the functional testing of a newly designed handheld device.
Seal test fixture.
Schneider’s latest project was a challenge because the handheld needed to be waterproof, operating in up to a meter of water. After researching materials and costs, he selected several seals with various cross sections that he thought would do the job. But he still needed to test them to be sure they’d hold up. If the test proved unsuccessful, he’d have to either redesign the enclosure or go for more expensive seals, which could push the project outside its cost estimate.
The PolyJet Process Acquiring accurate, high-resolution prototypes from a variety of materials has been the mainstay of the PolyJet rapid prototyping process. Using ink-jet technology combined with UV curable materials, the process quickly and economically produced highly detailed and accurate physical prototypes. With a layer thickness as small as 16 microns (0.00063 in.), the process is ideal for producing detailed parts for a variety of industries.
The PolyJet process produces prototypes without support vestiges, and with up- and down-facing surfaces. A variety of materials, including clear, Shore A and Shore D materials are available. These prototypes are best suited for applications where accuracy, detail and surface finish are important. Typical applications include electronic components and connectors, electronic packaging, knobs, buttons, medical devices, fittings, valves and parts with complex interior features.
|
In the past, Schneider would have to design the enclosure and outsource it to a model shop. This could take several weeks, and costs could go way over budget really fast. If he had to redesign the enclosure and go through the same process again, things could get even worse. Then Schneider had another idea.
“I only had a few hundred dollars to spend on the test prototype,” he recalls. While searching for a way to keep costs down, he ran across ZoomRP. “Not only was the company able to produce the parts I needed at a cost that saved me money, but I was able to get the seal test components overnight. This severely reduced my design time, as well.”
Because color was not an issue at the time, there was no need to sand or paint the components. Plus, all the key features came out highly accurate, which made them fit the waterproofing test perfectly.
“The resolution of the prototype was well within the +/- 0.005 that I required, plus the smooth surfaces were perfect “something I couldn’t have gotten with selective laser sintering (SLS) or fused deposition modeling (FDM),” Schneider says. “Ultimately, this also meant that I’d only need one version of the test enclosure.”
To test the operation, Schneider fashioned a PVC pipe into a water chamber over a meter deep, the specified depth the handheld was required to withstand.
“It was quite simple, really,” he adds. “I placed the seals into the prototype from ZoomRP, screwed it together, and submerged it into the make-shift test fixture.”
The seals held: “I had my answer that day, and could continue on with the rest of the project,” Schneider says.
ZoomRP produced the enclosure from standard VeroWhite material using one of its PolyJet systems. The company’s PolyJet product offers high-resolution prototype models with excellent feature definition, ideal for smaller parts fitting within about a 5-in. cube (see “The PolyJet Process.”) The company is equipped to handle hundreds or more prototypes a day, which allows it to guarantee overnight delivery if the design is downloaded by 5 p.m. Eastern Standard Time.
Subscribe to our FREE magazine,
FREE email newsletters or both!Latest News
About the Author

DE’s editors contribute news and new product announcements to Digital Engineering.
Press releases may be sent to them via [email protected].
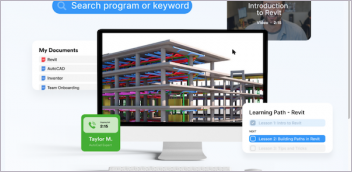

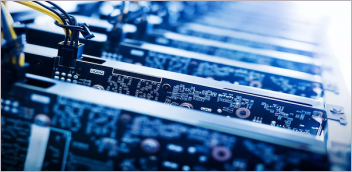
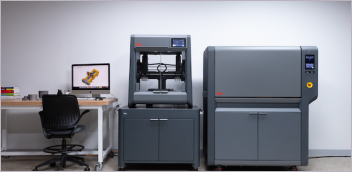