Fast App: NVIDIA Maximus Makes ‘Design Clinic’ a Success for Cleat Inc.
Latest News
January 11, 2012
By DE Editors
![]() Kensuke Yamashita, President and CEO of Cleat Inc. |
Cleat was founded by Kensuke Yamashita in 1990, following his experience as a car designer at Honda R&D Co., Ltd. Over the last two decades, the company has landed a number clients, including Giant, a global sports bicycle manufacturer, Nike Japan, and Square Enix, a Japanese video game and publishing company.
During the recent economic downturn, competitors went on the offensive in all areas, armed with large-scale operations and low prices—creating competitive challenges for Cleat. It was in that environment that Yamashita conceived Design Clinic, a company initiative using 3D CG.
The initiative is offered as a supplement to a manufacturer’s product development process—something that has historically been hard for major production companies and publishers to break into. However, as a former industrial designer, Yamashita had a lot of expertise and personal contacts in this area that helped ease Cleat’s entry into engaging in it with clients.
“We provide customers with consultants who develop a methodology for better product design, which can be a competitive advantage,” he explains. “This approach is easily understood by clients who are trying to rise above the competition. However, they couldn’t sacrifice the speed of delivery, even for an improved design methodology. As soon as our Design Clinic was presented, manufacturers then demanded more precision and speed.”
The recent emergence of HP Z800 workstations with NVIDIA Maximus technology gave Cleat an opportunity to accelerate its Design Clinic approach.
A rendering by Cleat, Inc., with 3D Design by Jiro Katayama, CGI Direction
by Takuma Hashimoto (Cleat) and CGI design by Shunsuke Nakauchi (Cleat).
Accelerating Turnaround
In 2000, Cleat began receiving requests from manufacturers for advice on how to introduce 3D CAD into the field of industrial design. Yamashita initially responded to these requests for free; however, the demand grew into a specialized consulting business of its own. Today, it’s a fundamental part of the company’s operations.
“We transfer the images formed in our customers’ minds into pictures, which we call ‘image pictures,’” he says. “That is the core of our Design Clinic business.”
Back in 2004, after hearing Yamashita speak at a public forum, Yamaha Motor Co., Ltd struck up an affiliation with Cleat and its Design Clinic. At the time, Yamaha was looking for competitive advantages in the European market. Competition was growing, and Cleat’s Design Clinic idea sparked its interest. Yamashita surmised that customers seeking large motorcycles might have been compelled as much by the immediate attraction of the look of a product as they were to its quality.
“Previously, manufacturers concentrated on quality, cost and delivery,” he explains. “Today, as performance and quality are commoditized, emotion has become an essential factor in the purchase process.”
As Yamaha started to engage with Cleat’s Design Clinic service, the team at Cleat faced a number of challenges in producing high-quality 3D graphics that would evoke emotion and reflect features consumers found “necessary” in market research. The single biggest challenge Cleat faced in doing this for Yamaha was long rendering times, which made reviews nearly impossible. Yamaha would need to review the shape and color of the product in real time, and Cleat would need to vary and change it in real time, and rotate the product image 360 ° to review all sides. Unlike marketing/advertising work, which can be rendered as a back-room process, manufacturing work requires near-real time processing.
“It was simple,” says Yamashita. “We needed tools that would increase our work speed while preserving the quality of our work.”
Cleat’s Shunsuke Nakauchi uses an NVIDIA Maximus-powered HP Z800
workstation and Autodesk 3ds Max 2012 software with NVIDIA iray.
Faster and Better
In October 2011, Cleat installed an NVIDIA Maximus-powered HP Z800 workstation. The configuration at Cleat consists of an NVIDIA Quadro 6000 ultra high-end professional graphics card and an NVIDIA Tesla C2075 companion processor. They use Autodesk 3ds Max 2012 Subscription Advantage Pack software that includes the ActiveShade real-time rendering application featuring NVIDIA iray rendering software. With these new tools, the company was able to provide high-quality 3D graphics, while also reducing rendering times from 10 minutes to 30 seconds, according to NVIDIA.
“Our previous workstation took about 10 minutes to change the color of a wheel. In the new NVIDIA Maximus environment, iray runs smoothly, and at a high speed—improving our workflow. It can complete rendering in about 30 seconds; the amount of speed increase is overwhelming,” Yamashita notes. “Before utilizing NVIDIA Maximus technology, producing and rendering a movie in which the product could be rotated 360 ° was an overnight job. Now we can complete the entire movie in 30 minutes.
“The most important part of our work is to express the ‘ambience’ of the products,” he continues. “Our previous workstation technology allowed instant preview, but the quality was unsatisfactory and didn’t deliver the right ambience. NVIDIA Maximus technology has finally given us both the quality and speed to achieve this.”
NVIDIA Maximus technology has also helped Cleat improve the experience of its other clients who use tablets to show images and movies of objects from various angles to test subjects in surveys. When rendering was performed on Cleat’s previous workstation, it would take two to three minutes for an image to appear, compared to the 30 seconds it now takes using NVIDIA Maximus technology. Also, because the workstation can now be used to perform other tasks while rendering, time can be used more effectively overall.
The Autodesk 3ds Max 2012 Subscription Advantage Pack software includes
the ActiveShade real-time rendering application featuring NVIDIA iray
rendering software.
Improved Work Environment
Shunsuke Nakauchi is a creative artist at Cleat who’s in charge of producing visual images for product advertising and market survey purposes.
“I often am asked to start working on another job while my workstation is already rendering a project,” he says. “With NVIDIA Maximus, the workstation can now render a job and prepare for the next job at the same time. This means I can work more quickly and efficiently than I was able to before. It’s great for me and, ultimately, for our clients.”
Before Cleat installed NVIDIA Maximus-powered HP Z800 workstations, Nakauchi worked on two workstations simultaneously via a server connection: one for the rendering scene and the other for editing the original data for the rendering. This use of two workstations required data sharing, meaning repeated uploading and downloading of data—a cumbersome and time-consuming process. Cleat’s new NVIDIA Maximus systems have since eliminated this process, because all work can be performed on a single workstation.
“The stress of working with two pieces of reference data at more than 1GB in size, with a rendering scene going on at the same time, has been eliminated,” says Nakauchi. “The data read and write speeds have also improved immensely. Prior to working with the NVIDIA Maximus system, rendering speeds decreased noticeably when data exceeded 1GB in size, but that’s no longer a problem.”
Continuing to Innovate
Cleat Inc. is now working to establish “communication CAD,” a new service that acts as a bridge linking engineering, design and sales locations. It will enable Cleat and its clients to view the same picture at the same time, with the ability to change colors and viewing angles. The NVIDIA Maximus-powered HP Z800 workstations are playing an active role in this project.
Before embracing NVIDIA Maximus technology, design processes took many hours, and changing designs to improve their overall quality and satisfy Cleat’s clients added even more time to project schedules—resulting in increased client costs. By establishing an NVIDIA Maximus-enabled production environment, Cleat has improved its customer service and production capabilities, and the company now expects to expand its business.
“Since our NVIDIA Maximus-powered production environment now drastically reduces rendering times, our fees charged to clients can now be reduced,” Yamashita concludes. “Lower fees enable our clients to place more orders and get the most accurate, best images that suit their needs faster than ever before.”
MORE INFO
NVIDIA Maximus
HP
Subscribe to our FREE magazine,
FREE email newsletters or both!Latest News
About the Author

DE’s editors contribute news and new product announcements to Digital Engineering.
Press releases may be sent to them via [email protected].
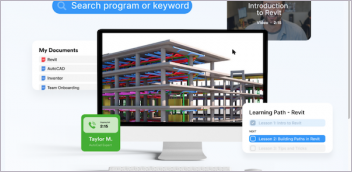

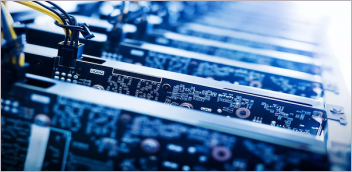
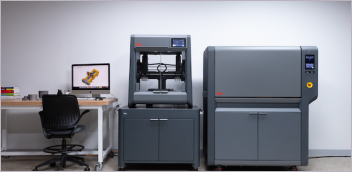