Latest News
March 22, 2011
By DE Editors
In 2009, Kirkland, WA-based Pathway Medical Technologies received the U.S. Food & Drug Administration (FDA) 510(k) clearance to market its JETSTREAM G3 peripheral atherectomy catheter for use in the treatment of peripheral arterial disease (PAD) in the lower limbs (below the knee).
JETSTREAM G3 is capable of treating the entire spectrum of disease found in the PAD patient, including hard and soft plaque, calcium, thrombus and fibrotic lesions. This technology, combined with national screening initiatives, is increasing the options for patients suffering from PAD and helping them avoid long-term complications of the disease.
Streamlining Research
Pathway Medical was using a paper-based system for managing all of its medical device documentation, part drawings and engineering changes. One room housed all of the company’s paper procedures and hard drawings, with a checkout system similar to how a library works.
“Because it was paper-based, you physically had to go to the vault to obtain any of Pathway’s product blueprints and drawings,” recalls Ken Perino, Pathway’s senior director of quality assurance and regulatory compliance. “If you found someone had checked out the documentation you were looking for, you had to go and find that person, which was a time-consuming effort.”
Perino spearheaded Pathway’s initiative to automate its product development process. He had worked in previous medical device start-ups, and was well versed in the benefits of a product lifecycle management (PLM) system to support his efforts. Perino was interested in bringing in a PLM system to streamline the entire engineering change process, implement better security with document vaulting, improve bill of material (BOM) management, and make product information—drawings, blueprints, revisions and supporting materials—easily yet securely accessible to appropriate team members.
Pathway selected the Empower PLM solution from Omnify Software because of its ease of use, fast deployment time and low cost, Perino says. Document control, engineering change, BOM and regulatory conformance processes are now managed via the Empower PLM system. All departments that have governing procedures are using the system, including design engineering, quality, regulatory, manufacturing engineering, purchasing operations, and even facilities management. Any changes made to any procedures are performed and managed within Empower PLM.
“Gone are the days that a physical folder is being passed around and emails flying around in regard to where the folder is, in terms of going through the different teams for an engineering change,” Perino says. “Because Omnify completely automates this process, when you submit your engineering change for review, the system sends it out to everyone who is a signer or observer in parallel—and the engineering team can view engineering changes in real-time.”
Easing the ISO Audit: Quality, Training and Validation
Pathway Medical is required to meet ISO certification (ISO 13485:2003 international standard). ISO auditors will check to see how Pathway (or any company they are auditing) manages its product documentation, change orders/change management, and engineering processes. Prior to automating with PLM, Pathway used to have to show and explain its manual process and walk an auditor through the vault that housed all of the company’s documentation. Now the Pathway team can show the ISO auditors how documentation is accessed online and tracked. Custom reports can now be easily generated to show specific information, as well.
For quality regulations and compliance, the company is implementing the Omnify Empower Quality Management module to document and track all non-conformances and customer complaints.
“There are some 15 to 30 non-conformances reported per week, depending on Pathway’s product volume,” Perino says. “These non-conformances typically occur on the production floor and during the inspection process, often due to a part failing a test or parts not matching up correctly.
“When parts come in, they are inspected, and if a part fails the inspection, it needs to be written up, documented and entered into the non-conformance database,” he adds.
ISO auditors also request to review the software validation, and FDA requires it. Pathway went through the proper channels and procedures to validate its software, proving that it applied security for authorized viewing and electronic signatures, and showing the audit trail of activity for documentation.
Pathway has its Omnify Empower PLM system integrated with its enterprise resource planning (ERP) system, Exact MAX, via an application programming interface (API). Engineering change orders (ECOs) documented within Omnify automatically populate within MAX.
“Omnify combined with MAX are strong for regulated environments, and successfully support Pathway Medical in addressing the reality of medical device regulatory requirements,” Perino says. “With full lot and serial control, Pathway is able to maintain the level of traceability required by the FDA—and it provides customers with the assurance that Pathway’s processes are sound and effective.”
Added Efficiency
Within a few months of deploying Omnify Empower PLM, Pathway saw major advantages and cost savings.
“Pathway now has the capability to engineer more products, because the Omnify system has freed up Pathway’s resources and has more bandwidth to do more,” Perino says. “Our engineering change processing time has been reduced from days to hours. We haven’t run the numbers on what that equates to in dollars, but I can say the less time our engineers spend processing engineering changes, the more time they can do actual engineering work. And that’s a very good thing.”
Bonus Benefit: Training Management The company’s training process is now fully automated. If training is needed, it is configured in the Omnify system as a task. In addition, Pathway has implemented an escalation process that automatically keeps reminding staff members that need to be trained. “I particularly like the automated training setup on policy, product or document changes, and the fact that it easily identifies recurring training events,” says Ken Perino, Pathway’s senior director of quality assurance and regulatory compliance. Combined with the Quality Management module, Perino says, the module supports Pathway’s compliance with closed-loop corrective action management (CAPA) system requirements. |
Subscribe to our FREE magazine,
FREE email newsletters or both!Latest News
About the Author

DE’s editors contribute news and new product announcements to Digital Engineering.
Press releases may be sent to them via [email protected].
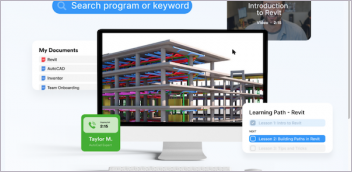

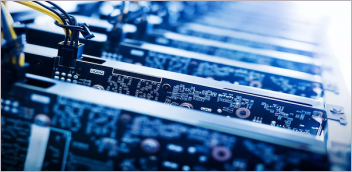
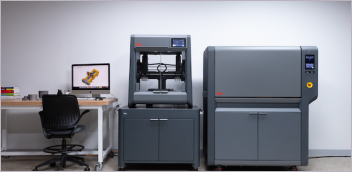