
Latest News
October 1, 2014
EcoCAR 3 is the third installment of the U.S. Department of Energy’s (DOE’s) Advanced Vehicle Technology Competition (AVTC), described on its website as designed to “help meet the demand for automobile engineers who are thoroughly indoctrinated in advanced vehicle propulsion technology.” The AVTC puts vehicle design teams from 16 universities to the test—in this iteration, challenging them to redesign the Chevrolet Camaro into a hybrid-electric car. The 16 teams will each reduce their modified Camaro’s environmental impact “while maintaining the muscle and performance expected from this iconic American car.”
The four-year competition runs through 2018, with university teams following the EcoCAR Vehicle Development Process (EVDP), which parallels competition sponsor General Motors’ VDP in that teams must establish a plan for R&D, analysis and validation of their EcoCAR 3 vehicle design over the four-year period. The undergraduate teams are expected to explore lightweight materials in addition to removing weight from the Chevy Camaro’s design as part of the overall competition.
The EcoCAR 3 competition provides each team with a copy of the NX 8.5 CAD package from Siemens PLM Software to perform their solid body modeling for the modified Camaro designs.
Losing Weight
New features of the EcoCAR 3 that set it apart from the previous EcoCAR competitions include an underlying goal to reduce energy consumption and emissions without compromising fuel performance and utility, says Jesse Alley, technical lead, EcoCAR 3 Program, Argonne National Labs. To do that, teams really need to reduce the weight of the vehicle.
When it comes to removing weight from designs, anything goes—within reason, of course.
“Anything is possible as long as you can do it safely,” Alley says. “We don’t limit specific things: They can create a rear cradle out of magnesium if they can convince GM that it is structurally sound, based on structural and finite element analysis (FEA).”

Judging from past EcoCAR team activity (EcoCAR 2), however, teams use mostly aluminum and carbon fiber whenever they depart from steel, after considering costs, safety and budget.
Typically, teams also self-limit what they attempt.
“For the most part, we didn’t touch anything structural due to safety,” recalls Katherine Bovee, EcoCAR 2 controls team leader for The Ohio State University (OSU) EcoCAR 2 team. But the EcoCAR 2 competition did enable the OSU team to work on lightweighting power trains and body panels, so long as they could make them strong enough. “To maintain vehicle safety, teams are required to use a safety factor of 2 over requirements, meaning two times the required strength,” says Bovee.
Simply using smaller designs is an option. Instead of replacing existing materials with a lot of lightweight materials, the Pennsylvania State University (PSU) Advanced Vehicle Team achieved lightweighting by cutting weight out of the designs. “We replaced the stock engine (during EcoCAR 2) with a .75 liter engine. We figured out what was the smallest possible component to power the vehicle, and used a 90 kW peak electric motor while other teams used a 165 kW peak electric motor,” says Benjamin Sattler, project manager of PSU’s Advanced Vehicle Team.
The Carbon Fiber Factor
The choice of materials varies among teams in these EcoCAR competitions. Some simply use steel. Other pursue aluminum such as for rear cradles, which can help drop 10 to 20 lbs., Alley says. “The OSU team did that for EcoCAR 2.”
A couple of teams in EcoCAR 2 used carbon fiber for battery enclosures. One team used it for structural components. OSU and Ontario’s University of Waterloo used carbon fiber for trunks and hoods. “Carbon fiber is probably the most interesting thing that any of the teams use,” says Alley.

Teams see opportunities and challenges when working with lighter materials, he adds. Although carbon fiber is lighter and stronger, it is more expensive and not always suitable for complex designs. Aluminum and steel are more a fit for creating sub-frames, which resemble a bunch of steel tubes that are welded together. Aluminum is an isotropic material that is easy to design with, because it will react consistently under various pressure conditions. By contrast, carbon fiber does not react the same to differing pressure. (Editor’s note: See “FEA & Composites” for more information.)
“How you pull it and how you orient the strands when making parts determines how it will work,” says Alley, noting that carbon fiber requires advanced analysis and design techniques to get it to do what team members want. “The teams who are working with carbon fiber are really pushing the limits for an undergraduate design team.”
Bovee recalls that her EcoCAR 2 team looked at Kevlar, fiberglass and carbon fiber for light weighting, but ultimately selected carbon fiber for their Malibu’s hood. The team considered using Kevlar in the hood to increase its strength, leveraging Kevlar’s favorable strength-to-weight ratio.
“A lot of the team members who worked on the carbon fiber hood will stay on for EcoCAR 3, and try to get the Camaro’s weight down,” she adds, noting that the EcoCAR 3 will be similar to the EcoCAR 2.
“In addition to the composite materials, we have aluminum, magnesium and titanium to consider for the EcoCAR competitions,” says Bovee. Aluminum is softer and easier to work with than a block of steel when creating engine mounts and brackets for inverters, she says. But titanium and magnesium are largely financially out-of-reach for teams in these competitions.

“We looked at getting magnesium rims, but they were too expensive,” says Bovee. Using magnesium could have taken off 10 lbs. per rim, adding inertia and favorably affecting fuel economy. “We could have achieved better acceleration and shorter plug-in times, too, since it is a hybrid,” she admits.
Likewise, the PSU team had some wishful thinking about design maneuvers that they just couldn’t cram in. They wanted to replace the brake rotors on the EcoCAR 2 vehicle with titanium, but there would not have been time to have had the rotors reviewed for safety and to ensure they maintained the thermodynamic qualities necessary in a stock car. “We were able to replace the iron brake hats with aluminum hats, though,” says Sattler.
As with most metals, there are a slew of different aluminum alloys a team can use, where the material properties are malleable depending on the heat treatments they apply.
“You have to be careful, though, because the resulting metal will start to deform at different temperatures,” Sattler warns. “It will also experience different compressive loadings in a crash event.”
For the project, a team can replace steel with aluminum and, if they choose their alloys correctly, they will see the same mechanical properties they need to maintain and have them in a lighter component, he says—but there are trade-offs, such as how much and how well one can machine or weld the resultant metal.
“A great alloy may not be easy to machine,” he adds.
While the first order effects of light weighting include increased performance and fuel economy, there are other benefits, Alley says.
“The teams could also improve handling (utility) by making stiffer chassis components that don’t bend, while keeping the weight the same by using lighter materials,” says Alley.
More Info
Subscribe to our FREE magazine,
FREE email newsletters or both!Latest News
About the Author

David Geer is a freelance technology writer based in Northeast Ohio.
Follow DE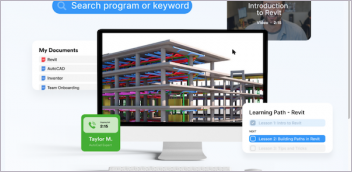

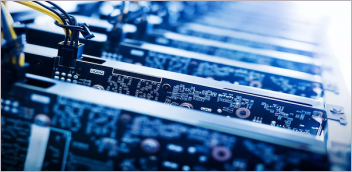
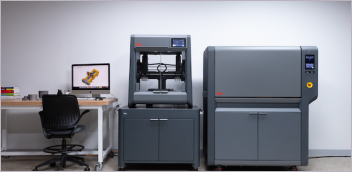