Editor’s Pick: Real-time quality assurance for advanced metal additive printing
The new module is Data Analyzer, software for quality assurance and data analysis.

A chart showing how the various modules in Foundry, including the new Data Analyzer, work to improve Joule Printing. Image courtesy of Digital Alloys.
Latest News
January 20, 2021
Digital Alloys has released a new software module for its Joule Printing process control software, Foundry. The new module is Data Analyzer, software for quality assurance and data analysis. Together with existing Foundry modules, Data Analyzer provides for non-destructive inspection of printed parts. The result is a capability for quality control in a Joule Printing factory.
Digital Alloys describes Joule Printing as its patented technology for using joule (resistive) heating to “rapidly and efficiently melt metal wire into high-quality near-net-shape parts.” The company says Joule Printing is “an order of magnitude higher print resolution” compared to Wire DED (Directed Energy Deposition), an open method of metal printing used in 3D printers from several vendors.
Digital Alloys says their Joule Printing method offers throughput as fast as existing Wire DED printers but with better resolution. The company explains that Wire DED printing can achieve high volumetric deposition rates, but only with thick wire that results in low process resolution. By comparison, the company says Joule Printing uses higher linear speed that achieves a higher ratio of print speed to resolution.
Data Analyzer joins the existing Foundry module Printer Console, which provides closed-loop process control and process data management. Data Analyzer improves the throughput of Joule Printing by adding quality assurance and data analysis, offering a repeatable production process.
The company says the addition of Data Analyzer in Foundry makes Joule Printing even more reliable for fine-grained real-time process control of the print process. Embedded algorithms in Foundry control five elements: Printer Management; Process Control; Print Data Management; Data Management for MES and ERP; and Maintenance, Repair and Operation (MRO). The resulting tight control of process parameters allows the system to deliver consistently dense (99.5%) strong isotropic parts.
Data Analyzer allows viewing and analyzing data from the many sources captured by Foundry. The module can generate custom plots for process signals, which can then be manipulated and navigated to focus the data on various informative events. The company says a QA technician could use the data, for example, to identify regions where a print process deviated from preset operating bounds.
Data Analyzer is now available directly from Digital Alloys for existing Foundry users.
Sources: Press materials received from the company and additional information gleaned from the company’s website.
Subscribe to our FREE magazine,
FREE email newsletters or both!Latest News
About the Author

DE’s editors contribute news and new product announcements to Digital Engineering.
Press releases may be sent to them via [email protected].
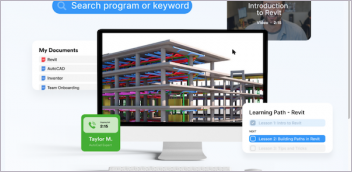

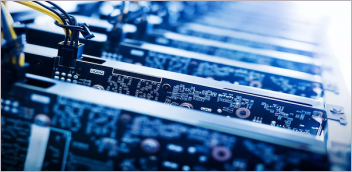
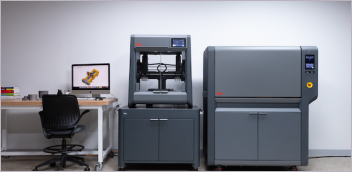