Latest News
June 1, 2012
By Jessica Milan
The benefits of a systematic product cost management program are significant, yet many manufacturers struggle to implement them effectively. Let’s discuss the guiding principles to initiating an effective product cost management program.
Who Owns Product Cost Management?
Many people and departments within an organization have an impact on product cost. An engineering team decides on a specific design, but design alternatives dictate different costs. A sourcing team pays to produce a specific design, but there are multiple potential costs for manufacturing the design. A manufacturing team selects one way to produce a design and estimates a ballpark cost, but there may be more cost-effective ways to manufacture it.
Traditionally, product cost management has been performed by cost engineering experts. Their domain knowledge builds over time, but it’s difficult to duplicate and scale across all products developed by a large organization. Effective product cost management requires a set of systematic activities, processes, and tools for use throughout the enterprise to guide decisions to the lowest costs available. For design engineers, this approach enables you to attack cost at the point of origin and yield the greatest impact.
Core Cost Management Activities
There are a number of core activities involved in effective product cost management that involve design engineering—as well as other departments. Some of the most recommended include:
- studying cost tradeoffs of different concepts at the R&D stage;
- evaluating multiple design alternatives for lowest cost during new product introduction (NPI);
- evaluating the cost of proposed solutions to an engineering change order;
- evaluating multiple manufacturing and tooling alternatives for lowest cost, including make vs. buy analysis;
- generating a detailed “should cost” to validate supplier quotes and ensure lowest pricing;
- batch analyzing current prices of commodity groups to find over-cost outliers; and
- evaluating multiple cost-down ideas on current products in real time to identify the highest potential reduction.
Cost Management Processes
The core activities above fit into various processes over a product’s lifecycle, and include key cost control points during the product development process. These are measurable, managed checkpoints that dictate where and when people should perform the core cost management activities above. The output and results of these activities continue to build on one another throughout the product development lifecycle.
For example, during NPI, there are typically design review meetings at regular intervals to ensure that it’s meeting requirements. But rarely is there a conversation about the financial implications of different design alternatives. Mandatory cost evaluation should be part of key design review milestones.
Another example is when a design reaches the release to manufacturing milestone. At this point, there is often a decision to make or buy that product, or key components within it. The company that has implemented a cost control point at this milestone could be quickly calculate the financial impact of both options to make an economically wise decision in a fraction of the time it would take to create and manage a request for proposal.
Cost Management Tools
Effective product cost management is also enabled by putting the proper tools in the hands of everyone who has an impact on product cost, especially design engineering. These tools help identify and assess true product costs at a detailed level at any stage, and enable people to act on the appropriate opportunities to reduce costs. Some of these tools might include:
- product cost estimation systems that can quickly and consistently generate and manage accurate cost estimates without requiring specialized manufacturing or cost knowledge;
- reporting systems for documenting and tracking cost management results and key product indicators over time;
- analytics systems to search large volumes of data and identify cost outliers and trends; and
- bill of materials cost-tracking systems to roll up costs at any point in a product’s lifecycle.
Without these core activities, processes and tools, product cost management remains a manual and decentralized function—of value only to manufacturing or cost engineering experts. It also leads to inconsistent estimation methods with static information that is difficult to update, manage and share.
To truly affect product costs and drive down the costs of goods sold by entire percentage points, manufacturers must deploy product cost management further upstream in the development process and across all departments and levels. Design engineers must identify key cost control points, and define the activities and processes needed to reduce costs. Organizations must also have the right tools to analyze the cost of trade-off decisions quickly and easily each time they make a decision.
Jessica Milan is a client engagement manager at aPriori (aPriori.com). Send e-mail about this article to [email protected].
Subscribe to our FREE magazine,
FREE email newsletters or both!Latest News
About the Author

DE’s editors contribute news and new product announcements to Digital Engineering.
Press releases may be sent to them via [email protected].
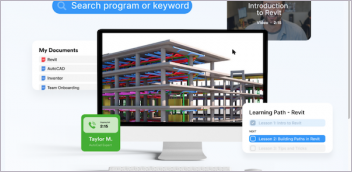

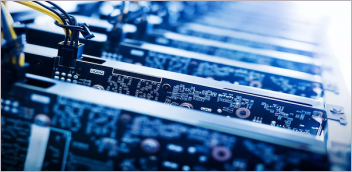
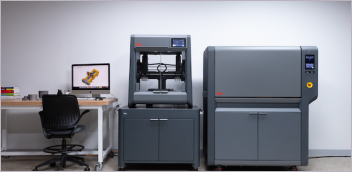