
Latest News
January 2, 2018
CAD—specifically parametric CAD—was developed as an efficient solid geometry construction approach. Therefore, CAD programs are ideal for design engineers who need to express their concepts, whether the shape of an automotive part or the housing of a smartphone, in detailed 3D geometry. Dassault Systèmes’ SolidWorks and CATIA, Autodesk Inventor, Siemens PLM Software’s Solid Edge and PTC’s Creo Parametric exemplify such programs.
By contrast, a newer crop of optimization and generative design programs were developed to let design engineers seek and evaluate a range of possible design options, based on a mix of time-tested FEA (finite element analysis) principles and algorithms. Examples of such programs include Autodesk’s Project DreamCatcher, Altair’s solidThinking Inspire, nTopology’s Element and Frustum’s Generate. In some ways, they are the opposite of CAD. Some of them include a limited set of geometry construction tools, but they function primarily as form-generating engines, sometimes offering unorthodox geometry that users may not have imagined.
In the last few years, the introduction of topology optimization and generative design elements in CAD has started to blur the line between parametric modeling and generative design. The technology experimented with in Project DreamCatcher is now part of Netfabb, Autodesk’s software targeting additive manufacturing. Autodesk also introduced Shape Generator in Autodesk Inventor 2016, Release 2. Topology Study is a new feature debuting in SolidWorks 2018. These features significantly change the way design engineers use CAD software.
Speaking at this year’s Additive Aerospace conference in Los Angeles, Franck Mouriaux, RUAG Schweiz AG aerospace structures general manager, observed, “Engineers were not trained to formulate the problem. They were trained to find solutions.” Formulating the problem, as it turns out, is the key to generating good geometry.
Tell Me Your Problems
No doubt, engineers can express a design challenge in natural language. For example: If I redesign the bracket holding the rocket fuel tank to be 5% to 7% smaller, will the tank still be secure when the rocket is traveling at a certain speed? But formulating such a problem in computable terms—regions targeted for material reduction, regions that must remain unchanged for safety and aesthetics, anticipated stress loads on the bracket while the object is airborne, the direction of the loads, the type of vibrations it’ll likely endure, and so on—is a different matter.
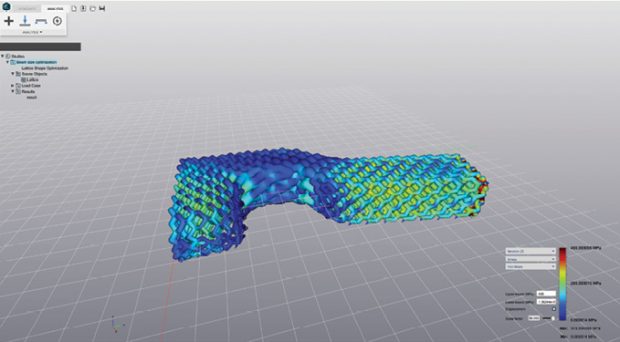
The skill to express the design problem as a set of parameters can be found in simulation software users. But this requirement could prove a steep learning curve for people trained in CAD.
“[It’s especially difficult] for entry-level mechanical engineers,” notes Jesse Coors-Blankenship, CEO of Frustum. “But people who have exposure to FEA (finite element analysis) and CFD (computational fluid dynamics) simulation have a much easier time getting started in generative design. They certainly can pick it up faster if they understand how to apply realistic engineering constraints. Moreover, we see a future that is more multidisciplinary, making engineering concurrent. This brings team knowledge to the product ideation phase, which can help to release the burden on the mechanical engineer to define the problem and create the solution with such new methodology.”
Frustum describes its software, Generate, as “functional generative design.” According to the company, it lets you “move beyond the boundaries of traditional CAD modeling and harness the power of additive manufacturing and the cloud.”
“To best solve a certain design problem, should you use hex8 elements in the meshing phase, or are second-order test elements good enough?” asks Bradley Rothenberg, cofounder and CEO of nTopology. “A CAD user with no experience in simulation may not be able to answer these questions.”
“The solution you get is perfect for the problem you’ve defined, but it might not be perfect for the real problem.”— Bradley Rothenberg, nTopology CEO
To describe them in their own words, nTopology’s founders are a group of engineers “dead set” on developing the next generation of design software. “With our unique combination of generative, manual and simulation-based design tools, we let engineers create parts whose functional requirements are baked right in,” they proclaim on their home page.
To compare them to natural language, generative design inquiries are usually not yes/no questions (will it break or will it hold?); they’re formulated as what questions (under these conditions, what are the best bracket design options to secure the fuel tank?). As you add additional constraints or parameters (such as acceptable weight range for the bracket, preferred manufacturing materials and more), the design options change.
“We keep the physics under the hood,” says Rothenberg. “So if you don’t pick the type of mesh or tessellation, the software knows how to use the best standard mesh types to run the problem. But if you’re an expert and you want to control that, the software gives you that option, too.”
Frustum’s Blankenship agrees that accessibility to various users’ experience levels is key.
“We have worked very hard to make it as easy as possible to start using Generate,” Blankenship says. “It’s difficult to predict what the user may or may not understand up front. One thing is clear—after some hands-on demos, a light goes on and they’re excited to rapidly start iterating with generative design.”
Fusing Parametric and Generative Modeling
“The design process has always been generative. It’s just that computers have never been part of that generative process,” says Rothenberg. Furthermore, comparing CAD programs to generative design programs may be as counterproductive as comparing apples and oranges, because “the two are doing different things,” he adds.
nTopology offers Element Free, a lattice structure generation tool; and Element Pro, a more comprehensive version with geometry editing and analysis tools. “Our software looks more like a traditional CAD package than some of the other generative design tools,” says Rothenberg. “But it does both CAD design and generative design.”
“Frustum Generate is complementary to CAD,” says Blankenship. “Basically, there’s enough CAD interoperability to get you going with generative design.”
The new topology optimization feature in SolidWorks is based on structural and fluid solver technology from TOSCA, part of the simulation software portfolio from SolidWorks’ parent company Dassault Systèmes. TOSCA could be traced back to FE-Design, a German software developer acquired by Dassault Systèmes in 2013.
“We’ve always had optimization in SolidWorks, but it’s driven by dimension,” notes Kishore Boyalakuntla, VP of product portfolio management, SolidWorks. “[SolidWorks 2018] is the first time we introduced topology optimization. This is where, based on loading conditions you supply, the software takes away materials from the base geometry you supplied, and provides you with an organic, optimal shape.”
The new feature, dubbed Topology Study, gives you a choice to define whether to produce the part in additive or subtractive manufacturing. “Based on that specification, SolidWorks removes materials very differently for each approach,” says Boyalakuntla. Because the optimized geometry is a SolidWorks model, you can use the familiar CAD tools to refine the geometry in the final phase, he points out.
Build-in Constraints to Prevent Failures
Mark Cichy, director of computation and research at Dialog, a building design firm, makes a distinction between generative design and computational design. “In generative design, you use the computer to assist you in finding the right design. With computational design, you may design a framework that lets you combine a heavy data set, concepts and ‘build-ability’ factors to guide your design,” he says.
Cichy believes a good computation model should include rules to minimize failures. “Let’s say you have an unusual building envelope shape, and you want to explore ways to build it in titanium or glass-reinforced fiber cement,” he says. “You can build those material behaviors into the computational model, so the software knows what the maximum or minimum curvatures allowable are.”
“So what does it mean for your job? Are we moving to a world of driverless cars and driverless CAD?”—Andrew Anagnost, Autodesk CEO
Design engineers with less computational skills may prefer a generative design software that has built-in rules that automatically exclude forms that cannot be manufactured or constructed. On the other hand, Cichy prefers an open system that engineers or architects can use to build a framework of constraints, to limit the available options to fit the manufacturing or building criteria.
Quite often, what is mathematically optimal—geometry with sufficient material reinforcement to counter the anticipated stress in different regions—is impractical to manufacture or produce, either due to cost concerns or the limitations of the production methods available. Additive manufacturing (AM) now gives the option to 3D print certain complex geometric forms that cannot be machined; however, even with AM, there are certain rules about printable geometry.
“Many topology optimized structures have thin walls and complex geometries with lots of overhanging features, both of which may be challenging even for AM,” says Timothy W. Simpson, director of the Additive Manufacturing & Design Graduate Program at Pennsylvania State University. “Some of the new generative design tools take these into account, but most do not—and engineers are not used to making these trade-offs during the design process. Before AM came along, we didn’t even know these trade-offs existed, let alone how to account for them in our software and design tools!”
In some generative design programs, the manufacturing feasibility rules are part of the generative formulas; in others, they’re not. If they’re not, it’s up to the design engineers to work with the manufacturing engineers and construction engineers to account for them in the generative setup. Otherwise, the range of solutions proposed by the software will most likely include problematic geometric features.
Too Perfect for Reality
Math deals with the absolute; reality is full of uncertainty and unexpected changes. This makes generative design somewhat paradoxical. “The solution you get is perfect for the problem you’ve defined, but it might not be perfect for the real problem,” says Rothenberg. “You may have defined the [rocket fuel tank’s] pressure vessel with all the load cases you can think of, but in reality, there may be the effects of sloshing, which you didn’t consider or know how to define. So the optimization algorithm didn’t take that into account.”
Before optimization made lightweighting possible, engineers usually over-engineered parts to account for unanticipated load cases. They build parts to be much stronger than necessary, just in case. As lightweighting becomes the norm, over-engineering is now seen by many as a wasteful practice, an engineering sin. But is engineering parts with barely enough strength a good idea?
“The structures are optimized for a given set of loading conditions,” warns Simpson. “So if the part experiences different loading than anticipated during its operation, then the structure has a much higher likelihood of failure because of all of the material that has been removed during the optimization process. Nevertheless, generative design tools can give engineers new insight into what an optimal structure might look like, which helps them be more creative during the design process.”
For the time being, Rothenberg thinks the best approach is to let experts set up the optimization as a series of steps, then let the less-experienced or inexperienced colleagues use it as a guided workflow. That is the vision Rothenberg and his R&D team share. They’re working to accommodate it in their Element software. The strategy is similar to the template-driven approach to promote simulation use. (For more, read “Wanted: Simulation App Publishers,” DE, April 2017).
Changing Roles
Last November, during his keynote address at Autodesk University (AU) in Las Vegas, Autodesk CEO Andrew Anagnost decided to tackle the anxiety that’s on many CAD users’ minds. “So what does it mean for your job? Are we moving to a world of driverless cars and driverless CAD?” he asked rhetorically.
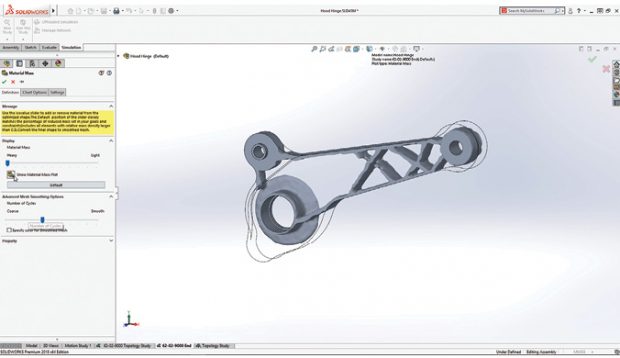
Cichy says, “The shift is [toward a workflow where] experience and the nature of knowledge are more tightly integrated. That is, the engineer, architect, designer, etc., can spend more time on engineering and less time on representing the engineering. One could argue that this is a much better position to be in.”
With the ability to churn out design ideas at a speed inconceivable to humans, generative design certainly appears to be a breed of self-driving CAD. For many veterans trained in geometry sculpting, this is a fundamental shift in the nature of their work, not a comforting thought.
“When I left architecture and went into construction, I discovered there are many designs that should theoretically work, but actually don’t,” says Cichy. “There are mitigating factors onsite that change the design. If it changes even by a millimeter, it has cascading effects.”
To develop a good computation model, or to set up the design-generating script correctly, you may need additional input from those with first-hand experience—those who are involved in transforming digital ideas into physical objects.
“The so-called old-timers have a lot of experiences to tell you what works, and what doesn’t,” Cichy points out. “So if you want to build the computational model with all the important variables, they’re the ones who can help you.”
“[With generative design,] there isn’t just one right answer, but there are many viable alternatives,” said Steven Hooper, Autodesk’s director of manufacturing strategy, in his talk at AU. “[Technology] doesn’t replace the design engineers; it augments them with the ability to explore that solution universe.”
More Info
Subscribe to our FREE magazine,
FREE email newsletters or both!Latest News
About the Author

Kenneth Wong is Digital Engineering’s resident blogger and senior editor. Email him at [email protected] or share your thoughts on this article at digitaleng.news/facebook.
Follow DE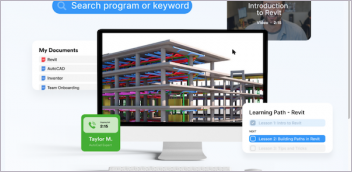

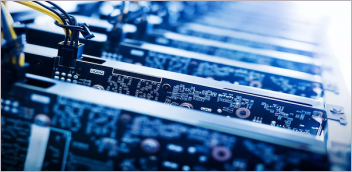
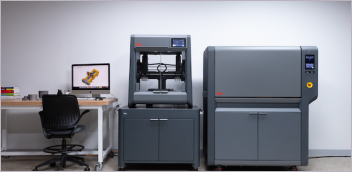