Delcam Offers Reverse Engineering with PowerSHAPE Pro
Integrates CopyCAD reverse engineering package.
Latest News
March 28, 2011
By DE Editors
Delcam has integrated the functionality from its CopyCAD reverse engineering package into the 2011 release of its PowerSHAPE Pro CAD system. This extended range of functionality, which will be supplied automatically to all users on maintenance, is suited for the creation of CAD models from all types of digitized scan data, and for the re-engineering of existing products.
PowerSHAPE Pro offers “Tribrid Modelling” — the addition of triangle modeling to the combination of surface and solid modeling that is offered in other CAD packages as “hybrid modeling.” Having all the different modeling techniques in a single package reduces the need to transfer data between multiple programs, according to Delcam.
With Tribrid Modelling, the company says PowerSHAPE Pro allows the design intent to be captured from the physical model rather than producing a duplicate digital representation. This is particularly important when generating models from items that might be worn or damaged, and in cases where the quality of the initial data is less than perfect. Three techniques can be used to convert the scan data into the CAD model, based on key points, surface patches or surface sketching.
PowerSHAPE Pro can use the positions of key points to create arcs and lines, and then convert them into the full range of prismatic solids. This approach will usually be much quicker than methods based on a complete scan of the object.
For more complex shapes, PowerSHAPE Pro now contains all the sculpting and model repair tools previously available in CopyCAD to edit triangle files. These tools allow uneven surfaces to be smoothed out, gaps in the data to be filled, and extra points to be added in areas where only sparse data has been collected.
The edited triangle data can then be converted into the component features. The user has total control over the way the complete data set is divided into the various elements. Each area can then be converted into CAD data by generating a network of curves and then projecting it onto the mesh of triangles. A single surface is generated within the complete set of curves, using PowerSHAPE’s Smart Surfacing functionality to analyze the curves and determine the most appropriate way to create the surface.
The third approach allows the user to sketch onto the surface of the triangle file and use the resulting lines to create the geometry. This can be done by rotating or extruding a single line to create a surface, or by sketching two or more cross-sections and then flowing a surface between them.
The solid model can then be completed with filleting and blending options within PowerSHAPE Pro.
At any stage in the process, analysis tools are available to display the differences between the triangle mesh and the model created in PowerSHAPE Pro. This will highlight any areas that are outside the required tolerance.
In cases when the scan data only represents the external surfaces of the component, PowerSHAPE Pro’s solid modeling tools can be used to produce a complete model.
The integrity of the final solid model can be checked with the Solid Doctor options within PowerSHAPE Pro.
For more information, visit Delcam.
Sources: Press materials received from the company and additional information gleaned from the company’s website.
Subscribe to our FREE magazine,
FREE email newsletters or both!Latest News
About the Author

DE’s editors contribute news and new product announcements to Digital Engineering.
Press releases may be sent to them via [email protected].
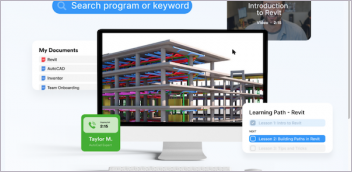

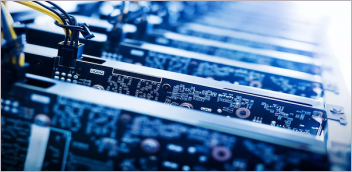
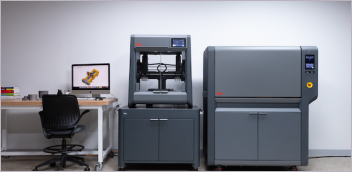