Creating a Custom Golf Club

Krone Golf Clubs are offered to a limited number of clients through an invitation-only program and fit by affiliated PGA Teaching professionals. Images courtesy of Krone Golf.
Latest News
February 1, 2017
Fore! It’s the universal warning call of golfers, often because they shanked a ball onto an adjacent fairway or—perhaps more rarely—drove the ball further than they expected. It means “heads up, watch out—a ball is coming your way.” Marc Kronenberg, CEO of Krone Golf, wants to help golfers hit long and straight. His company designs and engineers advanced custom golf clubs. A combination of 3D printing and machining enables him to tailor Krone’s KD-1 driver to individual golfers, but it wasn’t easy to find a process that would meet Kronenberg’s exacting specifications.
“Golf clubs have been made of titanium and composites for 20 years, but they haven’t been optimized,” Kronenberg says. After working in the golf equipment industry—starting in research & development before moving into product development and then to manufacturing in China—he wanted to find a way to make better golf clubs. He launched Krone Golf to provide custom clubs that enable golfers to reach their full potential.
“You can go and get a fitting and they’ll adjust the weight or shaft or provide a different loft,” he says. “Our process is different. It’s like getting fit for a bespoke suit. Nothing is premade. We watch you swing, see your strengths and weaknesses, and then design the club for each player.”
The nature of custom clubs make them a great fit for low-volume 3D printing, so Kronenberg initially looked into direct metal laser sintering for the titanium face of the driver. “It was good, but not fully repeatable and tolerances were not perfect,” he says. “If a golf club at the store says it has a loft of 10°, it might actually be between 8° and 12°. If you need a 10° degree loft, I will give you exactly that. CNC is the best way to do that.”
Looking for a Technology Trifecta
Kronenberg works with a CAD expert, but needed a manufacturing partner to realize his vision. He came across CRP Group online and sent an email to them out of the blue. CRP Group, based in Modena, Italy, has more than 45 years of experience in the world of F1 racing. One of its divisions, CRP Technology, produces and sells Windform composite materials for additive manufacturing. Another division, CRP Meccanica, provides high-precision CNC (computer numerically controlled) machining primarily for the motorsports, automotive, aerospace and marine industries.
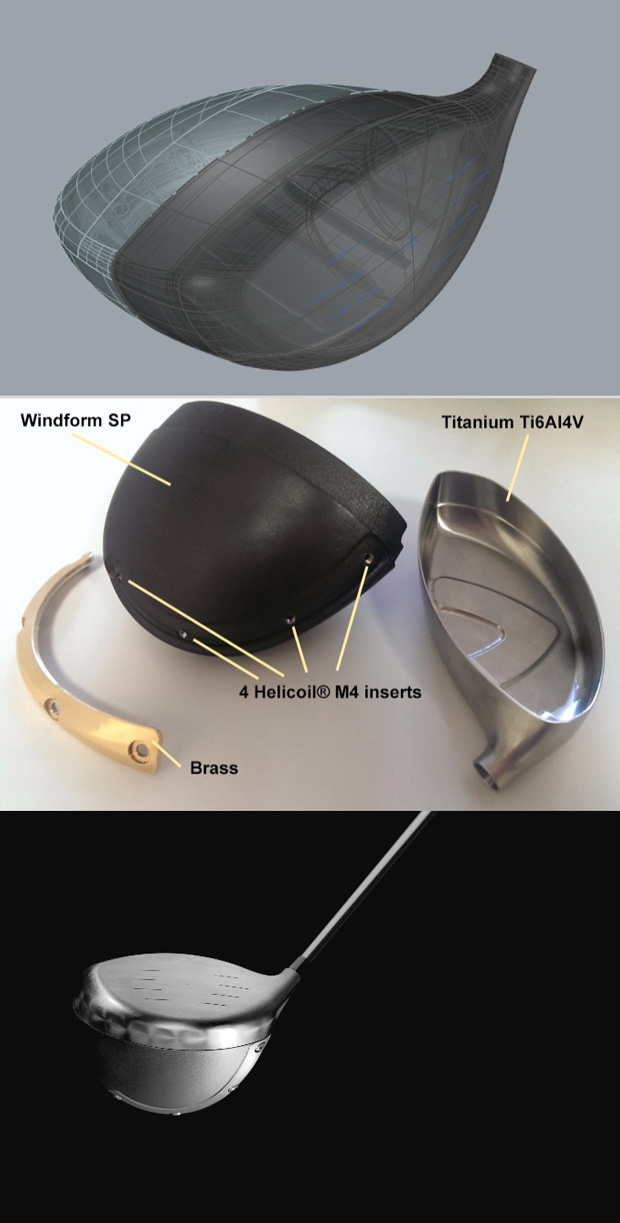
When CRP Group received Kronenberg’s email about a golf club, it wasn’t exactly a natural fit for the company. It took a few months and a trip to Italy by Kronenberg before CRP decided to take on the project.
Together, Krone and CRP Group found some similarities between golf and high-performance atomobiles. In golf, distance and launch conditions like loft, spin and ball speed are as easily measured and quantified as automobile acceleration and top speeds. The nuances of how a club feels in the golfer’s hands or how it sounds when striking the ball are similar to factors CRP Group was familiar with in the auto industry, such as getting the balance, handling and exhaust note just right.
The Custom Club Process
Titanium golf club parts are typically cast, stamped or forged. Their composites are laid up by hand using pre-impregnated materials cured by compression molding or in an autoclave. The traditional methods have limitations, according to CRP Group. Titanium cannot be cast or stamped any thinner, due to the need to post-weld parts together, and welding creates a heat-affected zone that can cause deformation in thin areas. Traditional carbon fiber parts cannot become any stiffer without switching to expensive high modulus fibers.
CRP Group says high-performing CNC machining and additive manufacturing solve those issues. CNC machining of the club face allows tight control of thicknesses in critical areas, while additive manufacturing of the body enables the creation of very stiff, lightweight structures and 3D lattice geometries that were not possible before.
CRP and Krone decided on a combination of Ti6Al4V titanium alloy for the face and hosel, a brass weight, and Windform SP for the body of the KD-1. Windform SP is a carbon microfiber reinforced polyamide laser sintering material that is resistant to shock, vibration and deformation, according to CRP Technology.
“Windform is strong and light, so it freed up some weight,” Kronenberg says. “We can now place a dense ribbon of discretionary weight across back.”
3D printing also allows for iterative changes and future improvements, such as adding sensors into the head of the club to track more swing data than current “smart” clubs track via sensors in the grip. “If you want to know what the golf club is doing, sensors should be in head too,” Kronenberg says.
A Krone golf club CRP previewed in its CES 2017 booth had a sensor in the head and one in the grip. Krone’s smart club prototype plans include both 3- and 9-axis accelerometers, a gyroscope and a magnetometer for the club, which will track swing data through an app. The electronics can be removed and replaced with dummy weight for actual play.
“CRP been a great partner to work with,” Kronenberg says. “If I send an order Monday morning, parts are in my hand Friday afternoon. They’re fitting beautifully—really quality stuff.”
More Info
Subscribe to our FREE magazine,
FREE email newsletters or both!Latest News
About the Author

Jamie Gooch is the former editorial director of Digital Engineering.
Follow DE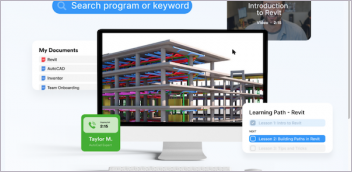

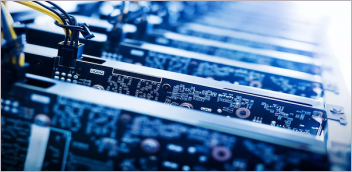
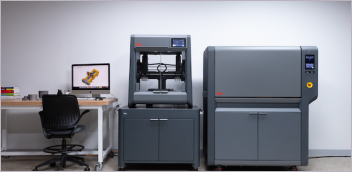