Closing the Manufacturing Skills Gap: The Essential Role of Training Platforms
As the industry becomes more technologically complex, manufacturers need to upskill their workforce before they fall out of date.

Latest News
July 17, 2024
A boom in manufacturing demand, increased retirement of seasoned workers, and low recruitment from the incoming generation of the labor force are combining to create a critical shortage in qualified labor. Manufacturers are responding to this skills gap in various ways. 65% of manufacturers are reskilling employees to address labor shortages, while 57% are introducing new technologies to make up the difference. While these measures are important, they don’t provide a complete solution, and may introduce new complications.
The skills gap is complex, and therefore requires a multifaceted solution. They key challenges manufacturers must contend with include:
- A retiring workforce who are taking institutional knowledge with them as they leave.
- Technological advancements which are filling in portions of the skills gap while also creating new training challenges.
- Low awareness from young people and their parents about career opportunities available within the manufacturing sector.
- Attracting and retaining the current skilled labor force through competitive job offers.
Each of these challenges can be solved with training tools, but to be successful, manufacturers must choose the right platform. If you’re looking for a training solution to your manufacturing skills gap problem, here are the four challenges your platform should solve.
Challenge 1, The Retiring Workforce: Capturing Knowledge Before it Disappears.
Manufacturing workers are retiring in great numbers. This demographic shift has been a long time coming, yet many manufacturers are caught in the difficult position of losing workers before they have found and trained their replacements. As a result, they are at risk of losing important institutional knowledge unless they prioritize process documentation before these workers leave.
The solution is an LMS platform with custom course creation features. This allows manufacturers to develop training with their current workforce in order to capture and standardize procedures long-term. Having these resources available will make it more efficient to train new workers as they come on board.
Challenge 2, Technological Advancement: Supporting Internal Training for New Systems.
While it’s crucial to capture the knowledge of the retiring workforce, even the most experienced workers need training to keep up with technological changes. As manufacturers introduce advanced systems into their production line—autonomous robots, augmented reality, and other Industry 4.0 innovations—they are in fact creating a new skills gap between their current workers and the technology they now need to learn to use.
Learning these new skills often means mastering the software created to control them. As that software updates, workers will need ongoing training support to learn along with it—and that means training materials that update alongside the software.
This is true of more advanced manufacturing positions as well, such as mechanical engineers, designers, or CAD users, many of whom enter the workforce with limited experience using industry standard software. These employees may need training support to get up to speed on the programs your company uses, as well as ongoing learning to keep their knowledge of those programs sharp. If you’re evaluating a learning platform, consider its content library alongside its other features and functions, and compare the courses it offers against your business’s current software stack.
Challenge 3, Career Awareness: Promoting a New Image of Manufacturing Opportunities.
Despite the introduction of advanced technology to the manufacturing sector, the industry still suffers from a reputation for being less sophisticated than other STEM-related industries. According to a survey from the Workforce Institute, 54% of manufacturers say that negative industry perceptions affect their ability to recruit Millennial and Gen Z talent, while in a separate study from Deloitte, 36% of manufacturers identified lack of interest in the industry among young people and their parents as a key contributing factor to the skills gap.
The Manufacturing industry needs to change this perception, and training opportunities might be their best bet. According to the American Upskilling Study, run jointly by Amazon and Gallup, the 18–24-year-old demographic lists training as one of their top benefits, above life insurance, retirement, parental leave, and vacation. A recruitment campaign that focused on both the new technology being used in the manufacturing industry and highlighted the training programs around it would help shift the industry image and attract new workers.
Challenge 4, Attraction and Retention: Effectively Competing for Top Talent.
Given the popularity of training opportunities among new workers, it stands to reason that a company that invests in high-quality continuous learning will also be better positioned to attract other top talent, as well as those just entering the industry. Among workers who already have training, however, the prospect of repeating courses or slogging through old material can be an inhibiting factor rather than an attraction.
Skill assessment tools can avoid this challenge by helping to match new hires with the appropriate level of training content. They can also support the hiring process by helping to identify what knowledge gaps an applicant has so that manufacturers can make more informed hiring decisions. In an ideal solution, the assessment tool would integrate with a manufacturer’s onboarding process, so that a new worker could come on board and have a customized training path ready for them from day one.
Pinnacle Series: LMS Platform + Elearning Library + Skills Assessment
If all of this sounds like we’re writing toward a specific solution, we are. At Eagle Point Software, we’ve built Pinnacle Series as the solution to each of these challenges. Our LMS platform is fully equipped to enable manufacturers to develop custom course content based on their internal best practices. Our elearning library carries a wealth of courses around the most in-demand content in the Manufacturing industry—including AutoCAD, Inventor, and SOLIDWORKS—and it grows each month, with new courses added and old courses brought up to date with the latest software versions. And our skills assessment tool not only identifies training needs, but also creates individualized learning paths so that trainees can start learning new skills from the first lesson.
The manufacturing skills gap will be with us for years to come, but it won’t affect all businesses equally. Those that invest in training—and publicize their commitment to continuous learning—will be more competitive in recruiting workers both new and skilled, managing their stores of internal information, building employee satisfaction, and retaining talent for the long haul.
Pinnacle Series can be your partner in this endeavor. If you would like to schedule a demo of our platform—or set up a free trial—contact us today.
More Eagle Point Software Coverage
Subscribe to our FREE magazine,
FREE email newsletters or both!Latest News
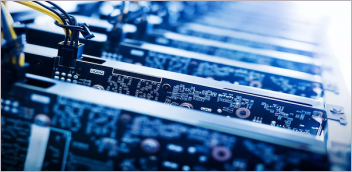
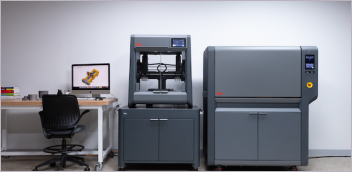
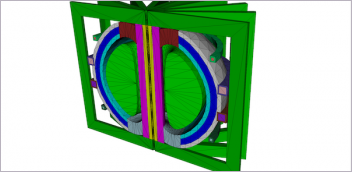
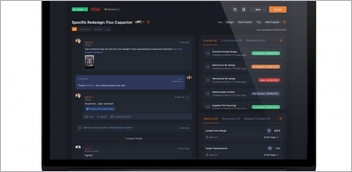