Capturing Reality

Autodesk Memento’s user interface is designed to allow non-experts to learn how to use it without training. Image courtesy of Autodesk.
Latest News
May 1, 2015

The dividing line between the physical and the digital has blurred significantly thanks to advancements in 3D scanning, post-processing software and 3D printing. Metrology technology that was once used simply to measure objects or buildings can now be used to digitize physical items, transform them, incorporate them into visualizations, and then produce altered versions of those products or components in the real world. Scanning has moved beyond metrology into what Autodesk is promoting as “reality capture” or “reality computing.” Instead of just capturing measurement, companies are now leveraging the same solutions to create 3D point clouds for more realistic models or visualizations. “We’ve seen all of these emerging technologies coming up and becoming more mainstream,” says Elmer Bol, director of Market Development in the reality solutions group at Autodesk. “Laser scanning is nothing new, but it has become more mainstream. It was clear to us that our customers wanted to move this data into our solutions, but they weren’t doing this just for the sake of doing it. It was a means to an end. They wanted to use that scan data to get some sort of deliverable that is valuable.” Companies are using these approaches in prototyping, reverse engineering, architecture, and even quality assurance applications. “The basic idea is that you 3D scan a real world object, make a comparison of the original 3D model that was used to produce the manufactured item, and perform a quality assurance,” says Evgeny Lykhin, vice president of Product Management at Artec Group. Unlike traditional metrology, the focus in many of these reality capture applications is less on precise measurement and more on scanning enough data to create viable digital models that can be manipulated and then built. “All of these uses just emphasize that people want to get three-dimension data that provides a close enough representation of the object that they can do planning, preservation or re-create those objects,” says Orlando Perez, director of Product Management at FARO Technologies. “The newer non-contact laser scanning methods do that quickly and efficiently.” In the reality capture model, 3D scanning technology creates high-density point clouds that can be pre-processed then used in 3D design applications. The captured data can be manipulated, edited, analyzed, integrated with other model information, or used to simulate real-world operations. Laser scanned or even coordinate measurement machine-based metrology data can be combined with feature recognition software to convert point cloud and contact-probe data into a 3D solid model that can be used for inspection or reverse engineering. The data can be turned back into both physical and virtual items. Visualization solutions can incorporate the digital objects, which not only helps provide context for the design, but can also help ensure that new designs fall within required specifications and tolerances. The data can also be fed to CAM systems or 3D printers to realize the new designs. The scans can also be compared to original 3D design models of the object or structure for deviation analysis and quality control. “It’s a paradigm shift,” Bol says. “We’re seeing this more and more, and it can be scary for traditional designers.” Using scans for reverse engineering is an accepted practice in many industries. More intriguing is the idea that users can scan objects in great detail, and create new and upgraded designs for products, machine components and other items. Combining the scan information with design exploration or optimization solutions, users can digitally alter real-world objects. They can then simulate the results of using different materials and production methods, or alter the physical shape of the component. “For example, in aerospace there is a push to make things lighter,” Bol says. “So, a company can scan a component they want to replace, take those constraints for what they scan and fill it in with something else. You can generatively grow lattice structures that are lighter, and then those lattice structures can be fabricated using additive manufacturing.” The scanned object can be utilized in an augmented reality program to simulate its incorporation into an environment or another structure. Users can check for fit, make alterations, and then create a prototype via a 3D printer. Enabling this approach to design is scanning equipment that is much more intuitive than in the past. “We’ve created algorithms and features that make scanning as easy as possible,” Lykhin says. “It’s still not a fully automated process, though.” Autodesk has teamed with a number of 3D scanner companies and other partners on reality capture projects. The company has also launched ReCap, its suite of reality capture software and services, and Project Memento, a toolkit that generates 3D meshes from photos and scans, and includes the capability to clean up the meshes, detect and fix mesh errors, and optimize the 3D models for publishing and other digital uses. The concept has gained traction in the architecture and BIM (building information management) space. TURIS Systems, for example, used Autodesk ReCap’s pre-processing functionality to help a client, Studio Gang Architects, renovate an existing building. The company scanned and modeled an existing power generation plant that was being converted to a student activity center. The company used a FARO scanner to capture 277 scans of the building. The point cloud files were joined in Revit to create a 3D model, providing engineers with an accurate documentation of the structure as they developed plans for the building conversion. TURIS reduced surveying time from months to days, and cut 15% from the cost of the project, compared to on-site manual measuring. “We’ve also seen clients use this for synthetic biology applications, and in fashion where people are creating 3D-printed organic dresses,” Bol says. Volvo scans its existing assembly cells and uses the point cloud to create a digital plant; the company then uses model data and scan information to simulate and verify production processes for new vehicles. In aerospace, Autodesk says a maintenance company is scanning existing jet engine or turbine blades so that they can use machines and specialized welding techniques to repair portions of the worn blades and ensure they stay in balance. Custom surgical implants are another area where reality computing has shown immediate utility. Oakland, CA-based FATHOM, for example, has used a combination of 3D scanning and printing to help develop customized prosthetics. The biggest challenge users face with reality capture is that much of the software is still hard to learn. “The hardware is pretty easy to use but the software required to create deliverables is complex and expensive,” Bol says. “The software is aimed at high-end professional users, and that’s an inhibitor that the industry needs to tackle.” At Autodesk, that effort has involved creating a new type of user interface for ReCap. “With ReCap and Memento, we set out to create products that you can learn without training,” Bol says. The other barrier: cost. “The technology is not cheap,” Bol adds. “But we’ve seen that, even though the cost of the software and hardware is high, once companies dive in and get the scanners, they can often earn their money back within the first project they use it on. That payback comes through reducing errors, finding problems and just being able to do things they couldn’t do before.” Scanner companies are also working to make the scan process even easier. “For our customers, the ideal would be to click one button, wave the scanner around an object, and get a scan — period,” Artec’s Lykhin says. “We’re not there yet, but we need to do everything we can to be as close to that as possible.” “The optics still have to improve to the point that you can get the same amount of accuracy or better from a laser scanner than you could with a high contact device, so that’s where a lot of the focus is these days,” Perez says. “There are different techniques evolving to provide more precision, that can change the contrast on the object or use triangulation.” And while much of the action thus far has been on the architecture side, product design and manufacturing are still big opportunities for reality capture. “We’re working with other product design teams, like Fusion 360, to integrate reality based workflows into the design side of things for mechanical parts and industrial parts,” Bol says. “We can quickly and simply digitize components instead of designing from scratch, and look at better ways of manufacturing that product. It’s still the early days, but that is getting a lot of attention.” More InfoPhysical to Digital and Back Again
Enabling New Applications
Autodesk Memento’s user interface is designed to allow non-experts to learn how to use it without training. Image courtesy of Autodesk.
Ease of Use Improving
Subscribe to our FREE magazine,
FREE email newsletters or both!Latest News
About the Author

Brian Albright is the editorial director of Digital Engineering. Contact him at [email protected].
Follow DE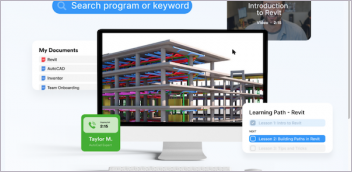

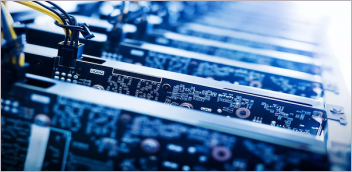
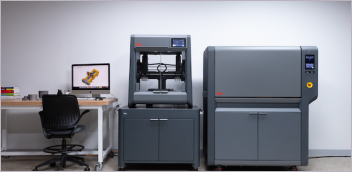