Latest News
December 1, 2006
By Nancy Rouse-Talley
Modern design and manufacturing is all about lean. The system of designing and implementing processes that add value by improving product and eliminating waste (see the sidebar “Defining Lean,” below) first began in Japanese automobile production facilities in the 1940s and has spread to other industries and to product development.
“For the past ten years lean was considered relevant only for manufacturing systems,” says Ron Yosefi, marketing director of digital manufacturing for UGS. ”Today we also look to lean transformation of design and the back office.”
![]() |
Delmia from Dassault. |
> > Modeling the factory floor in 3D with Dassault Systemes’ Delmia software can shorten the time it takes to design lean processes. Once modeled, processes are validated before they are implemented.
Successful execution of a lean program requires assessing processes, recognizing bottlenecks, and making improvements that not only eliminate holdups but enhance efficiency. In fact, when used properly, product lifecycle management (PLM) forces the evaluation of a process necessary for implementing lean programs. “Even if you apply PLM to an existing process, you have to start improving it before you implement,” says Yosefi.
Digital manufacturing programs such as UGS Corporation’s Tecnomatix and Dassault Systemes’ Delmia support lean manufacturing processes by helping manufacturing engineers pinpoint problems and validate production procedures. Software such as UGS Corp.’s Teamcenter, PTC’s Windchill, and Dassault Systemes’s Enovia Virtual Product Lifecycle Management (VPLM), Smarteam, and MatrixOne manage complex product engineering data and make it easier to share across the enterprise.
PLM Streamlines Manufacturing
Programs that model processes in 3D can shorten the time it takes to redesign manufacturing methods. Toyota uses Delmia software to model programs in its manufacturing facilities, for example. “Engineers can do an assessment of manufacturing processes, determining whether they have the right equipment and tools to ensure product quality before any change is implemented,” says Peter Schmidt, VP of marketing and business development for Delmia. “In addition, they validate (in 3D) that any change made does not put other parts of the process in danger.”
![]() |
Tecnomatix from UGS Corp. |
< < Manufacturing execution systems (MES) such as those in Tecnomatix from UGS can perform tasks like line balancing, where production line operations are aligned to minimize downtime and fluctuations in production. New Production Management portfolio software from UGS allows the MES system to share data with product design engineering.
UGS recently announced Production Management portfolio software that automatically links process definitions in the company’s Teamcenter PLM program to its Tecnomatix manufacturing execution system. (UGS acquired Tecnomatix in April 2005.) The Production Management portfolio uses a shared database that ensures consistency between planning and production, reducing hard-to-resolve differences between as-planned and as-built product configurations.
Moving Toward Lean Design
PLM also can power lean product development. Toyota’s Powertrain Division uses PTC’s Windchill PLM system to manage CAD data and the product-development process. Toyota standardized on PTC’s Pro/Engineer in 2002, and upgraded to Pro/Engineer Wildfire 2.0 in 2004.
Windchill maps concurrent engineering processes, says Brian Shepherd, division vice-president of product management for PTC. He adds that Windchill also helps Toyota standardize design practices. “Toyota is well-known for its rigorous standardization approach,” says Shepherd.
Shepherd says Windchill is used to store design templates that represent best practices for specific powertrain components. “Templates are downloaded ]from Windchill] into Pro/Engineer. A template would not involve a complete design for an engine, but perhaps a trusted design for piston rings,” says Shepherd.
![]() |
Windchill from PTC. |
> > PTC’s Windchill manages the data related to 3D design files. Once captured, this information is then stored in the system and can be reused by engineers.
PLM also speeds up design and manufacturing by exposing engineering data to the factory floor and other areas of the enterprise. The Matrix program from Dassault excels at this task says Jon Gable, vice-president of product management for Enovia MatrixOne, which Dassault acquired in May 2006.
One way the Matrix program encourages lean product development is by bringing together data from mechanical CAD, electronic design, software development, and process planning software into a cross-functional bill of material. Matrix also allows role-based classification, which makes it easier for workers with different jobs to find information.
Soon it will be easier for Dassault customers who manage mechanical CAD data in Enovia VPLM software to make that information available through Matrix. Gable says workflow tools or formal project portfolio management will provide access to design data now stored in local Enovia VPLM systems, allowing a more accurate picture of the total design process.
“Matrix is seen as an aggregation point for data,” says Gable. “As design deliverables are completed in VPLM, we’ll expose them at the project execution layer and make them available to the rest of the company.”
Part 2 of this article will describe in more detail how the features and functions of specific PLM systems support lean product design and manufacturing.
Nancy Rouse-Talley is a freelance writer who focuses on technology subjects, including product lifecycle management, computer-aided design, and engineering. Send your comments about this article through e-mail by clicking here. Please reference “Lean PLM, December 2006” in your message.
Defining Lean Manufacturing
In the 1990 book, The Machine That Changed the World, manufacturing experts James P. Womack, Daniel T. Jones, and Daniel Roos described the secret weapon that Japanese automobile manufacturers were using to beat America’s Big Three. They called it lean production and characterized it as a way to create value for customers by improving quality and eliminating waste. According to the authors, five principles guide lean manufacturing:
• Specify the value desired by the customer
• Identify value streams and eliminate wasted steps in them
• Make product flow continuously through the remaining value-added steps
• Introduce just-in-time production methods to all steps where continuous flow is possible
• Manage toward perfection to reduce the steps in the process and the time and information needed to serve the customer.
The seminal implementation of lean manufacturing is the Toyota Production System, which was pioneered more than 50 years ago by the company’s founder Sakichi Toyoda and engineer Taiichi Ohno. The Toyota Production System changed the way manufacturing engineers looked at production. It eliminated concentration on individual machine performance in favor of optimized product flow through a complete process. In lean, no one part of a process is improved at the expense of other parts.
Lean production methods eliminate what Ohno called the seven deadly wastes:
• Excessive time to transport product between processes
• Excessive, wasted, or improper motions by workers
• Waiting for the next operation in a process
• Maintenance of parts inventory
• Improper use of high-cost automation
• Quality defects that lead to scrap
• Overproduction of finished product
Tools such as kanban (instruction card) stock management, just-in-time inventory control, and poka-yoke (foolproof) equipment design are associated with lean processes. However, lean strategy is more than simply tools. A successful implementation of a lean program involves a new, process-oriented way of thinking.
“Tools will never be the competitive edge,” says Ken Kreafle, general manager of vehicle production engineering for Toyota of North America. “The competitive edge is found through the interface of people with the tools.”
The Toyota Production System helps workers find a problem, solve the problem, and keep the problem from returning, says Kreafle. Keeping a problem from returning is hard, he adds, and requires process standardization and the use of kaizen, or continuous improvement using problem-solving and analysis. It is kaizen that is central to lean thinking.
Kreafle adds that many companies have copied the tools used in the Toyota Production System without as much success. “They copy tools, but they don’t copy the thinking,” says Kreafle.
—N R-T
Companies Mentioned
Dassault Systemes
Suresnes, France
PTC
Needham, MA
UGS Corp.
Plano, TX
Subscribe to our FREE magazine,
FREE email newsletters or both!Latest News
About the Author

DE’s editors contribute news and new product announcements to Digital Engineering.
Press releases may be sent to them via [email protected].
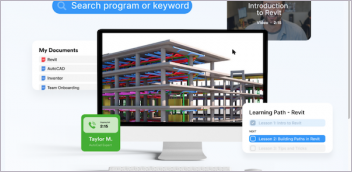

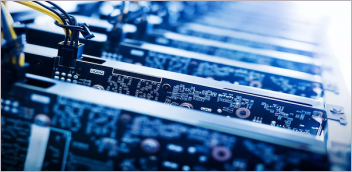
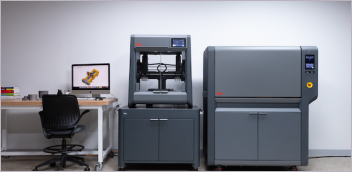