Aras Innovator: PLM on a Shoestring, 1 in a Series
Part I: When Phoenix International Holdings needed to implement a PLM system and essentially had no budget, choosing Innovator was easy.
Latest News
January 3, 2010
By Brent Evers
Aras Corporation and its PLM system, Innovator, have received considerable attention since announcing its business and licensing model change to open source. As expected, this new approach has spawned both skepticism and praise from users, competitors, and the press.
![]() Phoenix International Holdings designs, builds, and operates robotic vehicles and tools for use in the subsea oil and gas, scientific, and government markets. |
At Phoenix International Holdings, which specializes in the design, manufacture, and operation of deepwater (up to 6000 meter operating depth) remotely operated vehicles (ROV), autonomous underwater vehicles (AUV), and other subsea systems, we implemented the open source Innovator application in house with no outside support.
Phoenix is a 12-year-old employee-owned company. Readers might be familiar with the Navy’s advanced Towed Pinger Locator system—designed, built, and operated by Phoenix—that was most recently used in the search operation following last May’s Air France tragedy off the Brazilian coast.
![]() Phoenix previously managed engineering data via an array of spreadsheets and directories. |
Phoenix’s history is based in the operation of ROVs. Engineering grew out of a support role, and over time has evolved into a business unit primarily focused on the development of specialized, one-off subsea tools and vehicle systems. Many of our engineers have significant offshore and operations experience, and while some have new product development and manufacturing backgrounds, we do not have a strong foundation of experience with engineering systems to provide product data management (PDM), product lifecycle management (PLM), or configuration management (CM).
Learning PLM
Despite minimal experience with PLM systems, it became clear to those of us who were managing product structures and system development on a day-to-day basis that we had to improve processes and systems within our engineering organization.
As Phoenix approached the completion of several large engineering development programs in the early fall of 2008, the timing was right to revise our internal processes to reflect lessons learned and move closer to our end goal of corporate ISO 9000 certification. We also began investigating tools to support the implementation of our improved internal processes, and “Web-demoed” several PLM systems.
Our initial review of PLM tools was driven from the integration needs of our CAD tools. Phoenix uses OrCAD from Cadence for schematic capture, PADs from Mentor Graphics for PCB layout, and primarily SolidWorks for mechanical design. Several of the PLM systems we reviewed were biased toward one type of CAD system or another. And while few seemed to be able to demonstrate a solid existing integration with all of the platforms that we wanted to integrate, each company assured us that they could do anything for a price. This happened in September of 2008 as the economic sky was falling, making the prospect of asking for new funding less than prudent, if not outright foolish.
![]() Aras Innovator provides a complete PLM solution with no cost barriers to entry. |
Cost Realities in a Financial Crisis
Because of our cost limitations, the larger vendors weren’t even up for consideration. We were focused on a solution for our team of 35 engineers and draftsmen that would require an initial outlay under $50,000. Several options fell within that realm, but most seemed to bring a distinct possibility of significant cost creep that might have embarked the company on a never-ending spending spree in support of the elusive “complete PLM solution.”
In our initial investigation, one theme became more and more apparent: The more we learned about PLM systems and the processes that they are designed to support, the more we realized how little we knew. This compounded the investment problem. With financial resources already tight and getting tighter, what if we made the wrong choice?
There was one system that was different: Aras Innovator. It was free. We were very dubious, which was further reinforced by competitive vendors who were rightly worried about this new potential competitor. “Aras—yeah, I’ve heard of it—it’s like some shareware utility sort of thing.” Our IT department was especially skeptical, having been burned on other occasions with the lure of open source applications that turned out to be untested, undocumented, and a resource burden.
We put some of those questions to the folks at Aras. We asked them, “How do you configure this? How does it handle SolidWorks data?” The usual response was, “Well, Aras can configure that for you or you can configure that yourself.”
In the end, because we were gun shy to commit funds to an effort for which we had so little understanding, we punted. We decided to download and install Innovator and experiment, using the talents of our software engineers. We figured, if nothing else, we’d learn enough to make a better-informed decision later.
Phoenix Requirements
As engineers, we (ideally) develop systems through a systematic approach with its foundation in requirements definition. Unfortunately, when it came to our own PLM implementation, we didn’t know enough to even know what to require. But we had some ideas about what we wanted to achieve with its implementation. They included:
- A single process for development and documentation of all engineering projects
- A single repository (vault) for all project data
- The ability to establish and revise a product structure
- The ability to control all documentation
- A formal document (drawing) release and change process
- The ability to pack and go with all project data so that vehicle operators could pull all project documentation prior to a job and take it to an offshore environment where communications might be impossible to establish.
Gaining Confidence
As we began to work with the Aras Innovator software, we generated more questions about our own processes and we slowly but surely began a spiral refinement process of our own requirements, even if we never formalized them. We learned some things about PLM systems, about our own (lack of) processes, and that we needed to put a lot more effort into figuring out how it would all fit together. Most importantly, we wanted to implement it without it becoming an overburdening beast to our lithe but out-of-control ability to get a functional prototype design operating in the water quickly.
In the next installment of this series, we’ll discuss the process of implementing a PLM system without outside assistance and on a minimal budget. We’ll talk about the advantages of that learning process and how it has helped Phoenix better define the processes that it needs to be successful.
Read part 2 of this article here.
Brent Evers is the engineering manager at Phoenix International Holdings, Inc. Send comments about this article to [email protected].
Subscribe to our FREE magazine,
FREE email newsletters or both!Latest News
About the Author

DE’s editors contribute news and new product announcements to Digital Engineering.
Press releases may be sent to them via [email protected].
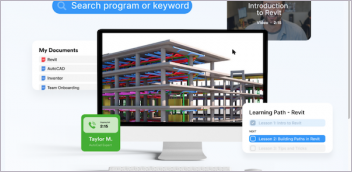

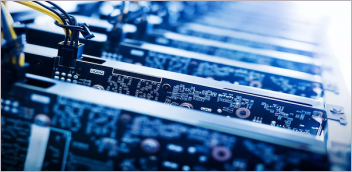
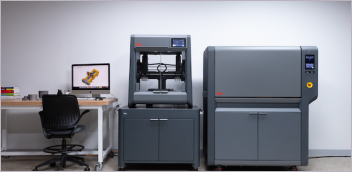