AMSIS Presents Build-Job Prep and Simulation Software
The software is a combination of a classic pre-processor with simulation-based laser beam exposure for reduction in support structures, the company reports.

An example of fast thermal simulation within AMSIS simulation software. Image courtesy of AMSIS.
Latest News
November 14, 2023
With further development of Genesis to the level of Genesis 4 Beta, AMSIS presents the latest generation of build-job preparation and simulation software at Formnext 2023. This universal software offers new features for equipment manufacturers as well as end users in 3D printing of metals to improve laser exposure quality and minimize support structures, the companmy reports. Genesis 4 modules can be integrated into 3D printer software.
Genesis 4 supports end users along the process chain of build-job preparation: importing of STL data, optimal placement and nesting of parts in the build space, generation of support structures, slicing, hatching and exporting the build-job. The USPs of Genesis 4 are the simulation-based functionalities: automatic identification of the overheated zones of a part, automatic reduction of the energy input depending on the overheating intensity and the hatching design of the optimal orientation and sequence of the exposure paths.
Fast thermal simulation within seconds for small parts and up to just a few minutes for large parts enables the precise identification of overheated zones of a part and a quantified depiction of the overheating intensity (criticality). On the basis of the calculated overheating intensity, a specific reduction of the energy input in the overheated areas is carried out.
Using the results gained from the thermal simulation, hatching strategies for the optimal orientation and the sequence of the exposure paths are also realized. Together, all of the above simulation-based functionalities result in an optimized thermal management of the overheated part zones, a significant reduction in support structures, as well as an improvement of the mechanical material properties and quality of the part surfaces.
“Optimized thermal management increases the process stability of the 3D part structure,” says Vasily Ploshikhin, managing director of AMSIS. “End users can significantly increase the performance of their existing machines with Genesis 4 and print higher quality parts with either minimal or no support structures.”
As stand-alone software, Genesis is available in two versions: Classic and Innovative. Genesis Classic, the basic version, has all the functionalities for build-job preparation. It can be used as an alternative to established software tools for build-job preparation, such as Magics from Materialise or Netfabb from Autodesk.
In the advanced version, Genesis Innovative, classic build-job preparation is complemented with simulation-based functionalities. These include the fast-thermal simulation module to identify overheated zones, the module for simulation-based local parameter adaptation and the hatching module for designing the optimal orientation and sequence of the exposure paths. The two software versions currently run via native machine formats on 3D printer from Aconity3D, DMG MORI, EOS and SLM Solutions.
Sources: Press materials received from the company and additional information gleaned from the company’s website.
Subscribe to our FREE magazine,
FREE email newsletters or both!Latest News
About the Author

DE’s editors contribute news and new product announcements to Digital Engineering.
Press releases may be sent to them via [email protected].
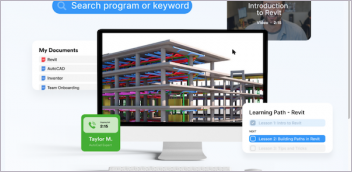

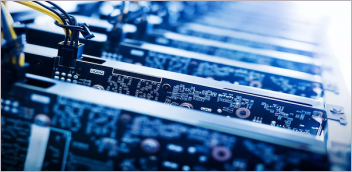
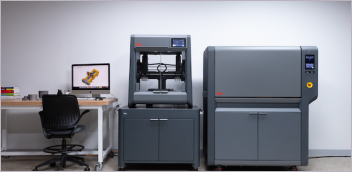