Alcoa Expands Metal Powder Production

DCIM100MEDIA
Latest News
July 18, 2016
Aluminum giant Alcoa has opened a state-of-the-art 3D printing metal powder production facility at its Alcoa Technology Center near Pittsburgh.
The new plant will produce titanium, nickel and aluminum powders “optimized for 3D printed aerospace parts,” the company said.
“Alcoa is forging a leadership path in additive manufacturing with a sharp focus on the critical input material—metal powders,” said Alcoa Chairman and Chief Executive Officer Klaus Kleinfeld. “We are combining our expertise in metallurgy, manufacturing, design and product qualification to push beyond the possibilities of today’s 3D printing technologies for aerospace and other growth markets.”
Alcoa plans to develop materials with specific properties needed for high-performance components, leveraging its experience in developing metal powders for rocket fuel, paint and other applications.
The new facility will be part of the Alcoa spin-off Arconic once that division separates from Alcoa’s commodity business later this year. Arconic will be an independent, publicly traded company. The plant is part of a $60 million 3D printing initiative that also includes facilities in California, Georgia, Michigan, Pennsylvania and Texas.
Alcoa also recently announced its Ampliforge process, which combines additive and traditional manufacturing. It allows the company to print a near complete part, then treat it using forging and other processes. That process is being piloted in Pittsburgh and Cleveland.
In other metals news, Russian aluminum producer Rusal and machine tool manufacturer Sauer have signed a memorandum of understanding to develop 3D printing technology for the industrial use of aluminum and aluminum alloys. The companies will develop 3D technology for aluminum products to print parts in the machinery producing, aerospace and automotive sectors.
Rusal will develop alloys for powder conversion, which will be tested and qualified by Sauer equipment.
“The key benefit of 3D printing technology is its ability to make industrial parts of any shape and complexity that cannot be produced using conventional means. Also, the technology is practically waste-free,” Rusal’s Director for New Projects Alexey Arnautov said.
Subscribe to our FREE magazine,
FREE email newsletters or both!Latest News
About the Author

Brian Albright is the editorial director of Digital Engineering. Contact him at [email protected].
Follow DERelated Topics
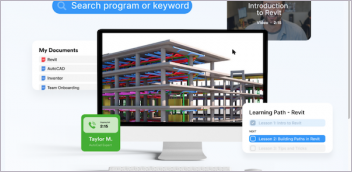

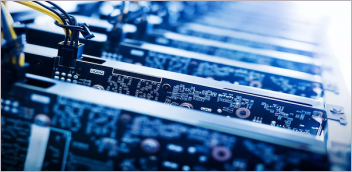
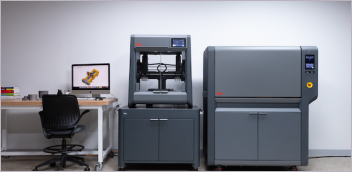