aesthetica Speeds New Opel to Car of the Year
GM Europe used Icona Solutions' manufacturing variation visualization solution to fine-tune Insignia while saving time & costs.
Latest News
January 3, 2010
By Neil McLeod
When the new Opel/Vauxhall Insignia from GM Europe won the 2009 European Car of the Year (COTY) award from among a field of 37 contenders, judges agreed that an important contributor to their decision was the “high perceived quality” of the automobile. Perceived quality describes the first impression a customer has of the look and feel of a product, without regard to its functionality. This visible high quality is an important differentiating factor among potential customers for deciding which products and brands they will consider purchasing, and it is a key component of brand identity.
![]() This illustrates a typical example of how aesthetica is used to decide whether gap and flush conditions are acceptable and will provide high perceived quality in the finished product. |
Key to GM Europe’s success with the Insignia was its use of advanced manufacturing variation simulation and visualization software during the car’s development. Known as aesthetica and developed in the UK by Icona Solutions, the software was used during the early concept design stages of the project—enabling the design, engineering, and manufacturing teams to understand manufacturing constraints and agree on gap and flush conditions, as well as manufacturing tolerances, as early as possible. This made it possible to achieve the highest possible perceived quality in the final vehicle without impacting development and manufacturing costs.
Dimensional Management
Ten years ago, GM Europe created the dimensional management department at its International Technical Development Center in Rüsselsheim, Germany to accurately manage tolerances over the entire vehicle development cycle. The department is led by Edgar Lossnitzer, who has defined the new perceived quality processes by instituting a tracking schedule known as the dimensional technical specification (DTS) that specifies all gaps and offsets visible to the customer (along with their nominal values and allowable deviations) and tracks them all the way to production.
The problem GM Europe encountered was that too many gaps were falsely interpreted through tolerance simulation. This often led to controversial discussions in the DTS setting meetings, as well as in follow-up meetings. This costly and time-intensive process resulted in late decisions and additional costs involved in implementing the required design changes.
![]() Target specifications for gaps and tolerances can be defined early in the process and decisions can be released for product development simultaneously using aesthetica. Effects of changes can be seen in real time. |
With a view to overcoming this problem, Lossnitzer and his team set out to fully investigate whether 3D visualization software could help in the dimensional management process during development of the Insignia. The team then chose to investigate aesthetica from Icona Solutions.
The software is unique in that it applies tolerances and component deformations directly to the product’s 3D CAD geometry. These 3D models can then be visualized, in real time, using different light sources, colors, and materials, and its components and assemblies can be distorted, buckled, and moved in 3D space and visualized in real time. (This is unlike traditional visualization software, which can only visualize a virtual product in its perfect, as-designed nominal condition.) With aesthetica, a realistic representation can be produced at any stage of development so perceived quality reviews can be undertaken, and fit and finish problems can be solved immediately.
Perceived Quality Studies
Opel implemented aesthetica at the early stage of the development of the Insignia. Superior design, vehicle dynamics, safety, and comfort, as well as superior aerodynamics and appearance (gap and flush) were all expected from this vehicle; models for the interior and exterior were generated from the first available styling data.
The parameters used for the aesthetica simulations were based on design and manufacturing data, including the material, fastening scheme, and tolerances. Complex deformation effects such as arching, bending, and distorting were represented, enabling identification of the root cause of problem areas. In fact, these parameters can be changed freely to test all possible solutions in order to achieve the highest possible quality in the final product. The digital model was continuously updated to accommodate styling changes, and the process continued beyond validation up to the final confirmation and improvement phase.
GM Europe/Opel uses NX from Siemens PLM Software for CAD and ICEM Surf from Dassault Systemes for surface modeling. Its tolerance stack-up and analysis of the chassis, body-in-white, and powertrain are completed in Vis VSA from Siemens PLM Software. Using aesthetica, design review meetings were routinely carried out in a virtual reality (VR) room so all meeting participants could easily view a 3D model without the need for any physical models.
In these meetings, all key stakeholders were able to review all tolerances, their effects, and any effects of changes. Target specifications could be defined based on realistic images early in the process and decisions could be released for product development simultaneously, thereby avoiding future surprises.
In order for discussions in the VR rooms to be completed as efficiently as possible, a typescript was generated beforehand. With this, the area of the vehicle, perspective, material combination, and light sources for the visualization were defined and stored in aesthetica. As a result, every condition could be quickly reconstructed. The new points and desired notes from the meeting could also be directly entered and stored in the same manner. This allowed new ideas to be discussed immediately and either pursued or rejected, partially eliminating the need for physical models and resulting in cost and—above all—time savings.
Depending on the phase of vehicle development, different goals were pursued and aesthetica’s 3D visualization capabilities proved indispensable because, in the absence of a physical vehicle, no conclusions could have otherwise been reached. This was especially true in areas where many components interface with each other (e.g., the boot ]trunk] lid, meeting of dashboard and door trim). In the development of the Insignia Sports Tourer, these areas were investigated with aesthetica and its Gap/Flush Fitting tools. With these, different possibilities for gap and flush could be judged until an optimal combination was found.
As a rule, only partial models were generated for the interior. These models included the front door trim, instrument panel, and the center console. To observe these areas from the viewpoint of the driver and passenger, the 3D CAD manikin RAMSIS from Human Solutions was used to collect data. Additionally, within the aesthetica model, rotation points were set at the manikin’s eyes to evaluate the view in all directions. Moreover, this avoided identifying problems as a result of being evaluated from unrealistic views.
Enabling Good Decisions
As the models became more advanced, more attention could be applied to elements like screws, rivets, or ribs within gaps, clip connections of components within the visible area, visible sub-materials such as sealing foam or glue, and elements visible through transparent components such as headlamps. This all helped to improve the overall visual appearance, or perceived quality, of the final vehicle.
Icona Solutions’ aesthetica software was developed as a visualization tool that enables vehicles to be developed in a cost-efficient and effective way. Although some people at Opel were initially critical of the high investment needed for the software and 3D visualization on a Powerwall, once it became clear how easily decisions could be made, they were convinced of the value.
Since introducing aesthetica into Opel, there have been no more long-winded and time-consuming discussions regarding a few tenths of a millimeter. Considerable resources have been saved by eliminating the need for physical validation models, and when considered with improved communication of necessary changes, faster decisions, and trimmed development costs, it’s clear to see why Opel feels aesthetica was a worthwhile investment.
More Info:
Dassault Systemes
Neil D. McLeod is a UK-based marketing communications and PR consultant who specializes in the CAD/CAM/CAE and PLM software and systems marketplace. To comment, send e-mail to [email protected].
Subscribe to our FREE magazine,
FREE email newsletters or both!Latest News
About the Author

DE’s editors contribute news and new product announcements to Digital Engineering.
Press releases may be sent to them via [email protected].
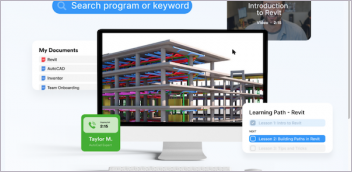

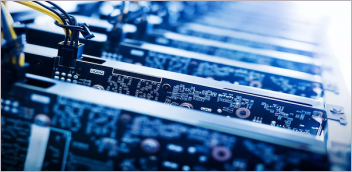
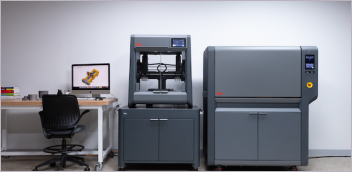