Latest News
A GPU Revolution in Discrete Element Method Applications
Altair Signs Agreement with European Space Agency
Nikon SLM Solutions Finds New Partner/Buyer for NXG XII 600
Auburn Engineering Secures $117.7 million in Rsearch Awards
AM Rides On-Demand Manufacturing Wave
JPR Releases Summary on GPU Market
All posts
July 1, 2006
By DE Editors
Dassault Systèmes (DS; Paris, France and Providence, RI) recently announced the availability of Version 2.3 of ABAQUS for CATIA V5. Version 2.3, says DS, takes advantage of the latest technology advances in both ABAQUS Version 6.6 and CATIA V5 R16 as well as builds on the company’s SIMULIA brand and strategy. (SIMULIA, which encompasses all DS simulation solutions, offers scalable simulation solutions and an open framework for performing multidisciplinary analysis within PLM.)
ABAQUS for CATIA V5 |
The integration of ABAQUS with CATIA enables advanced methods developed and validated by ABAQUS specialists to be deployed throughout enterprise as “proven” analysis workflows. This, in turn, enables both design engineers and analysis specialists to leverage identical FEA methods and models within CATIA V5. Not does this integration ensure repeatability and accuracy, says DS, but it allows design teams to do more simulations earlier in the product development process.
New functions in Version 2.3 of ABAQUS for CATIA let users leverage the weld modeling functionality of CATIA V5, which enables the rapid definition of a large number of rigid or flexible connections. New capabilities and improvements account for spot, seam, and surface welds. Connection locations can be independent of the underlying mesh, which reduces model size and complexity of the meshing requirements.
ABAQUS for CATIA V5 |
ABAQUS for CATIA V5 2.3’s support of ABAQUS Version 6.6 is reported to take advantage of full functionality of ABAQUS/Standard solver capabilities, including contact enhancements and performance improvements. Further, the ABAQUS continuum shell technology is available to users. This enables the modeling of shell structures with continuum shell elements, which permits the use of the actual CAD geometry of the structure rather than determining an approximate midplane and appropriate offsets of adjoining components. This approach is said to simplify modeling while improving the accuracy of simulations involving contact.
For more information, click here.
Sources: Press materials received from the company and additional information gleaned from the company’s website.
Subscribe to our FREE magazine,
FREE email newsletters or both!
Join over 90,000 engineering professionals who get fresh engineering news as soon as it is published.
Latest News
A GPU Revolution in Discrete Element Method Applications
Altair Signs Agreement with European Space Agency
Nikon SLM Solutions Finds New Partner/Buyer for NXG XII 600
Auburn Engineering Secures $117.7 million in Rsearch Awards
AM Rides On-Demand Manufacturing Wave
JPR Releases Summary on GPU Market
All posts
About the Author

DE’s editors contribute news and new product announcements to Digital Engineering.
Press releases may be sent to them via [email protected].
#10715
New & Noteworthy
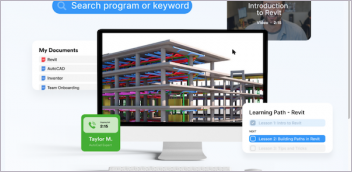
New & Noteworthy: Future-Proof Foundation for Employee Training and Education
Eagle Point Software's Peak Experience for Pinnacle Series adds AI chat, improved...

Eliminate Physical Clamping – With Simulation
The Virtual Clamping tool in ANSA (VCA) from BETA CAE Systems eliminates...
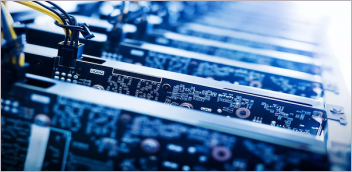
New & Noteworthy: Fast, Flexible and Scalable Simulation – In the Cloud
Ansys Access on Microsoft Azure enables seamless deployment of industry-leading simulation tools...
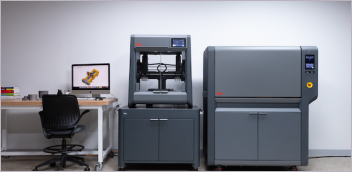
New & Noteworthy: Safe, Cost-Effective Metal 3D Printing - Anywhere
Desktop Metal’s Studio System offers turnkey metal printing for prototypes and...