A FARO Scanner, PolyWorks, and Rhino 3D Help Create a Rolling Lab
Biodiesel University uses the scan-to-3D process to breathe new life into decommissioned transit buses.
Latest News
March 29, 2009
By Susan Smith
![]() Digital ‘cutaway’ rendering of the CAD-modeled bus showing the interior layout with proposed equipment and education stations for the mobile lab. |
Four old decommissioned Washington, D.C. transit buses are the foundation for a new energy education program called Biodiesel University, a nonprofit affiliated with the University of Maryland.
In March 2008, Washington Metro (Washington Metropolitan Area Transit Authority) donated the last four of a decommissioned fleet of diesel transit buses to Biodiesel University so the buses can be turned into traveling educational institutions. Program Founder and Executive Director Dan Goodman says he hopes the mobile laboratories, which will demonstrate how biodiesel can be made from commonly found foodstuffs, will inspire students to pursue careers in science and technology.
As part of a multi-institutional collaboration, students from regional colleges and universities, including the University of Maryland and the Maryland Institute College of Art, have been involved in the design of the mobile labs since late 2006.
![]() Direct Dimensions technician Glenn Woodburn operating the FARO LS Laser Scanner to capture the interior shapes of the bus. |
“Our collective future depends, in part, on our ability to inspire the next generation of scientists and technologists to innovate solutions to the huge energy and environmental issues we face,” says Goodman, who is also senior fellow for renewable energy at the Robert H. Smith School of Business at the University of Maryland. “The mobile labs we are building will be part classroom, part hands-on science center, and part theme-park ride, packaged in a field trip that comes to you.”
The diesel buses will be completely converted to run on biodiesel and then will be outfitted with appropriate scientific and analytical equipment to travel around to different schools, colleges, and public events.
Inside the redesigned buses, visitors will be able to crush beans and seeds and extract their oil in an onsite processing section with access to 36 varieties of feedstock plants, their oil-bearing beans, nuts or seeds, plant oils, and derived biodiesels. A flat-screen monitor will provide detailed information on the benefits and trade-offs of each feedstock. This effort may evolve into a hands-on “feedstock museum.”
Although still in the conceptual stage, a state-of-the-art biodiesel processing unit in one bus will be designed to manufacture up to 250 gallons per day, according to Goodman. That fuel will be used to power the mobile lab as well as other vehicles and equipment at the sites along its route. Vegetable-based biodegradable motor oil, hydraulic fluids, and greases will lubricate the buses. On board, students will learn how to use real-world analytical equipment to test the chemical properties and quality of the fuel.
The Scan-to-3D Process
In the beginning, Goodman had assembled concept sketches of what all this would look like, but he needed measurements with some hard facts to present to possible sponsors of his project. Plus, ABC News was interested in doing a story, but all Goodman had to show at that time were four empty decommissioned buses and some of his sketches.
![]() A screenshot from Rhino3D CAD software of the in-process reverse engineering modeling work. | ![]() Initial raw data captured within the bus interior using the FARO LS Laser Scanner. |
While Goodman’s focus is on renewable energy technology, he asked Direct Dimensions, Inc. (DDI), a Baltimore, MD-based company that specializes in 3D digitizing and converting digital data into high-resolution computer models, to create models of the bus interiors. Direct Dimensions industrial designer Glenn Woodburn took six scans of both the interior and exterior of one of the buses using a FARO LS long-range 3D scanner. In two hours Woodburn collected more than 25 million 3D points, providing a high-resolution point cloud. Dan Haga, a designer at Direct Dimensions, then used InnovMetric’s PolyWorks program to process the point cloud and created an accurate 3D model and animation of the bus using Rhino 3D from Robert McNeel & Associates.
From there, Haga added Biodiesel University’s concept sketches to the model to create a conceptual design, including the placement of lab equipment on the identical buses. Including the scanning, Direct Dimensions spent close to 200 hours on the project.
Biodiesel University then promoted its program and mission using several photorealistic graphical renderings and a 60-second animated 3D virtual tour of the mobile lab design. The animation and renderings show the interior of the reconstructed bus housing an applications section that will feature biodiesel-powered demonstrations including a calorimeter, stove, generator, fuel cell, hot air balloon, water cannon, and a remote-controlled model car to demonstrate responsible uses of biodiesel. An algae farm and jet engine are planned for the roofs of the different buses.
“The renderings and virtual tours present the concept for our mission in a very compelling manner,” says Goodman. “We’re grateful for the effort and enthusiasm that Direct Dimensions has shown for our project.”
When Biodiesel University is ready to actually build its buses, it won’t have to re-engineer anything. Because of the 3D technology and modeling processes used, much of the engineering functions that would be necessary have already been completed. The model, although designed for presentation, is also dimensionally accurate.
![]() Comparison of laser-scanned data to CAD-modeled interior surfaces. | ![]() Comparison of laser-scanned data to CAD-modeled exterior surfaces. |
If Biodiesel University needs additional scanning work to detail the actual equipment inside the bus more accurately, or to upgrade instrumentation, close-range scanners will be used to carefully map out where everything is currently located. Once it is in the 3D CAD model, the equipment can be designed, fabricated, and installed.
“We see the rivets, everything that is in the interior of that bus and so all that can be modeled in the computer in 3D,” says Raphael. When Goodman is ready to build out the equipment inside the bus, he can hand a contractor an accurate computer model.“
![]() A screenshot from Rhino3D CAD software highlighting the in-process exterior reverse engineering modeling work. | ![]() Digital rendering of the CAD-modeled bus showing the proposed exterior geometry and graphical elements. |
Biodiesel University is currently seeking funding from a wide variety of sources, including corporate sponsorship and grants even as Goodman looks beyond the existing old buses. For Goodman, who envisions buses equipped with labs that educate visitors on food versus fuel sustainability issues, carbon, unintended economic consequences, pollution, and land and water use, the current vision is perhaps just the beginning.
More Info
Biodiesel University
Olney, MD
Direct Dimensions, Inc. (DDI)
Baltimore, MD
FARO Technologies, Inc.
Lake Mary, FLA
Robert McNeel & Associates
Seattle, WA
Autodesk, Inc.
San Rafael, CA
InnovMetric
Quebec City, Canada
Susan Smith is a contributing editor for Desktop Engineering magazine. She has been an editor and writer for the technology industry for more than 15 years and resides in Santa Fe, NM. Send e-mail about this article to [email protected].
Subscribe to our FREE magazine,
FREE email newsletters or both!Latest News
About the Author

DE’s editors contribute news and new product announcements to Digital Engineering.
Press releases may be sent to them via [email protected].
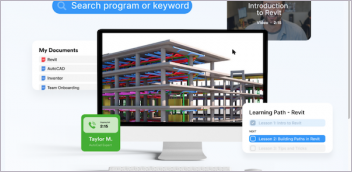

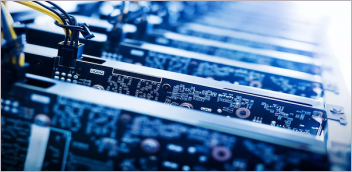
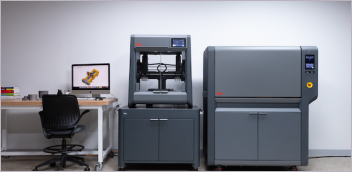