3D Printing Thinks Really Big

A massive plastic-extrusion additive manufacturing system is in development by Thermwood, a traditional CNC equipment manufacturing company, is pictured. Image courtesy of Thermwood.
Latest News
November 2, 2015
There was a time when 3D printing a 6-in. long car model was a mind-blowing process. Now companies are building full-size car bodies, functional bridges, live-in houses and operational jet engines. Additive manufacturing (AM) has become not just big business but a business of big proportions.
Thinking about scaling up your own designs? DE scoped out industrial-strength AM systems that can take on the big jobs, using build-volumes with a minimum of just about 1 meter (39 in.) dimension in one or more of the X/Y/Z build directions. Interestingly, most systems met that criterion for X or Y, or both X and Y values; however, a few systems qualify here based strictly on their extended Z-axis capacity. Also, with most equipment optimized for a single material family, the listings are grouped under plastics-plus, metals, and sand/ceramics applications. We’re leaving the bridges and buildings for another day.
Super-Sizing that Plastic, Rubber or Wood-like Part
- 3D Systems – ProX 950 (1500x750x550 mm; 59x30x22 in.) Perhaps it’s no surprise that, given its decades of experience as the original AM company, 3D Systems markets a large-volume system called the ProX950 production unit. This is a stereolithography (SL) system that can run 13 different UV-curable liquid resins from the company’s Accura line, in black or white ABS (acrylonitrile butadiene styrene) as well as in materials that are flexible, clear, tough or castable.
- 3DP Unlimited – 3DP1000 (100x100x500mm; 39.3x39.3x19.7 in.) This open-bed printer comes from a company experienced with controlling accurate industrial-strength linear motion. Printer type is fused filament fabrication (FFF) with layer resolution down to 70 microns. Three-millimeter filaments handled include, but are not limited to, polylactic acid (PLA), ABS, polycarbonate (PC), nylon, Ninja Flex and high impact polystyrene (HIPS).
- BigRep – BigRep ONE (1100x1050x980 mm; 43.3x41.3x38.6 in.) Offering a 1-cubic-meter build volume, this FFF system features ruggedness and accuracy aimed at industrial customers. The new, modular, dual-nozzle extruder can print support material and multiple colors; the universal spool-holder fits all filament spool sizes and holds up to four 10 kg (22 lb.) rolls in an enclosed cabinet. An improved heat-bed comes with auto-leveling.
- Cincinnati Inc. – Big Area Additive Manufacturing (BAAM) 100 Alpha Size 2 (6096x2362x1829 mm; 240x93x 72 in.) and BAAM 100 Alpha Size 1 (4000x2000x864 mm; 157.5x78.75x34 in.) Entering the world of AM backed up by more than 100 years’ experience with metal fabrication processes, Cincinnati Inc. offers two extremely large plastics-based 3D printers that can extrude 38 to 100 lbs./hour of pellet-feedstock thermoplastics.
- Cosine Additive – Additive Machine 1 (AM1) (1100x850x900 mm; 43.3x33.5x35.4 in.) This Houston-based company is big on composites. Its AM1 FFF system supports any third-party filament, but the buzz surrounds its use of polycarbonates. The system can process filaments containing a wide variety of additives including chopped and continuous carbon fiber, glass fiber, glass spheres, mica and stainless steel and bronze powders.
- German RepRap – X1000 (1000x800x600 mm; 39.4x 31.5x23.6 in.) Industrial users will be pleased with this larger version of the company’s previous FFF systems. Based on the open-source RepRep designs, the X1000 features an enclosed unit with a touch display, browser-based user interface and integrated nozzle cleanup function.
- Massivit3D – Massivit3D (1500x1200x1800 mm; 59x47.2x70.9 in.) This Israeli company, founded in 2013 by experienced 2D and 3D printing executives, managers, scientists and engineers, has developed an AM process called gel dispensed printing (GDP). The debut system can already print a UV-cured gel, using a shell/support approach, at rates of up to 1000 mm/sec (39 in./sec) on both X and Y axes.
- Materialise – Mammoth (2100x700x800 mm; 82.7x27.6x31.5 in.) The Mammoth system from Materialise in Belgium is a stereolithography apparatus (SLA) resin system; parts are available through the company’s service bureau only, but the company operates 14 of these enormous systems with typical lead times of four to eight working days. Currently offered materials are functional white, grey and transparent ABS-like plastics.
- Sicnova – JCR 1000 (1000x600x600 mm; 39.4x23.6x23.6 in.) Sicnova of Spain began in 2007 as a 3D printing consulting and reseller business, but decided that the market needed a larger FFF system. In March 2015, Sicnova introduced the JCR 1000, an enclosed, heated environment system with two print heads and interchangeable nozzles; the system can print with a large range of thermoplastics, nylon, rubber and carbon fiber materials.
- Stratasys – Objet1000 Plus (1000x800x500 mm; 39.4x31.5x 19.7 in.) In 2015, Stratasys added yet another PolyJet technology system to its line-up, this time extending its Objet line of multi-material printers with the Objet1000 Plus. Dual jetting allows combining base resins that are UV-cured into composite digital materials with properties ranging from ABS-like to rubber-like, with a wide range of colors and transparencies.
- Voxeljet – VX800 (850x500x1500/2000 mm; 33.5x19.7x 59/78.7 in.), VX1000 (1060x600x500 mm; 41.7x23.6x19.7 in.), VX2000 (2060x1060x1000 mm; 81.1x41.7x39.4 in.) and VX4000 (4000x2000x1000 mm; 157.5x78.7x39.4 in.) Each model of these large-scale AM systems from Voxeljet is available for purchase or for parts/mold production at the company’s service bureau facilities. Parts made by 3D printing a binder onto powdered plastic can be infiltrated with epoxy or wax; applications include prototypes or masters for lost-model casting.
Mega Metal AM Systems
- BeAM – MAGIC (1500x800x800 mm; 59.1x31.5x31.5 in.) and CLAD (1000x700x700 mm; 39.4x27.6x27.6 in.) The configuration of three- to five-continuous axes lets these directed-energy systems manufacture or repair metal parts using laser-melted metal powders. The MAGIC machine features a controlled atmosphere as standard; this is an option on the CLAD unit.
- Fabrisonic – 7200 (1829x1829x914 mm; 72x72x36 in.) Fabrisonic’s ultrasonic additive manufacturing (UAM) process builds up parts from thin metal sheets, while permitting separate parts and materials to be inserted in-process, from wires and electronic sensors to composite fibers and shape-memory alloys. The system can join fine layers of multiple metals without forming brittle intermetallic junctions.
- Norsk Titanium – (1200x1200x1800 mm; 47.2x47.2x70.9 in.) Norsk Titanium has developed a plasma-arc-based direct metal deposition technology to melt titanium wire for near-net shape manufacturing, as well as to repair titanium parts. The company recently announced plans to open a 200,000 sq.-ft. facility in the U.S., where it will operate several dozen of the units in a public/private partnership to produce aircraft parts.
- Optomec – 850-R (900x1500x900 mm; 35.4x59.1x35.4 in.) LENS AM technology, based on laser melting a focused stream of powdered metals, supports repair, rework and modification of high-value industrial components. The 850-R features five-axis motion and deposits up to 0.5kg/hour of metals such as titanium, nickel, stainless steel, cobalt, copper and aluminum.
- Plus Mfg – +1000K (1200x900x600 mm; 47.2x35.4x23.6 in.) Wire feedstock is used in this fully enclosed, arc metal deposition (AMD) system for creating near-net-shape parts. The company’s goal is to help users create parts quickly and with low energy draw; typical deposition speed is more than 2.5 kg/hour (upgradeable), currently processing steels, aluminum and titanium.
- Sciaky – EBAM 300 (5791x1219x1219 mm; 228x48x48 in. (typical)) Six decades of experience with electron beam welding led to Sciaky’s development of Electron Beam Additive Manufacturing (EBAM) systems as a fast, economical alternative to forging and casting of large parts. Each system is custom made. Materials processed include wire feedstock of titanium, titanium alloys, stainless steels, Inconel, tantalum, tungsten and niobium.
Sand and Ceramics for Really Big Parts
- 3Geometry – DSM1200 (1200x1200x420 mm; 47.2x47.2x16.5 in.) Based in India, 3Geometry markets a family of AM systems developed for tool-less manufacturing. The DSM1200, available in regular and high speed build versions (3600 cm3/hour or 10,000 cm3/hour) uses laser sintering technology to create sand-based molds for metal casting. Different sands are available for different end-metal applications.
- ExOne – Exerial (Two build sections, each 2200x1200x700 mm; 86.6x47.2x27.6 in.) and SMax (1800x1000x700 mm; 70.9x 39.4x27.6 in.) – ExOne systems use binder-jet technology to print sand cores and molds for casting parts. The SMax has a single job box; the Exerial model includes two build sections within the same system for continuous part production and processing.
- Prodways – ProMaker V4000 (1060x2250x2040 mm; 42x89x 81 in.) This system is the largest of the ProMaker V series from Prodways, a company of Groupe Gorgé based in France. UV laser technology supports curing of highly viscous ceramic materials, creating parts to be used as prototypes or in short production runs. When fired, the finished material is high density and highly homogeneous.
- Voxeljet – These large systems from Voxeljet, as mentioned above, can 3D-print a binder onto plastic powders and sand materials, the latter for creating cores and molds for casting. The company’s phenolic resin binders allow use of untreated silica sands with different pH values and ceramic materials.
So Close to 1 Meter
With a number of companies offering build volumes with almost-1-meter dimensions, we felt we should mention a few of them. By building your part on a diagonal, you could gain that hypotenuse benefit.
- Stratasys – Fortus 900mc (914x610x914 mm; 36x24x36 in.) FDM system works with 12 production-grade thermoplastic filaments.
- CMET – Rapid Meister ATOMm-8000 (800x600x400 mm; 31.5x23.6x15.7 in.) SLA system from Japan; works with proprietary resins, including clear, heat resistant and rubber-like.
- Concept Laser - XLine 2000R (800x400x500 mm; 31.5x15.7x19.7 in.) Powdered metal laserCUSING system, dual-laser build process.
In Development
A number of groups and companies have projects in the works to produce their own large-scale systems, some for general-purpose use and some for very targeted applications. For FFF systems, check out the ongoing work at Builder, Monkeyfab, Powercap Energy Systems, SeeMeCNC and Stacker. In the meantime, here are two groups developing large systems for metals and composites.
- Aerosud – Project Aeroswift (2000x600x600 mm; 78.7x23.6x23.6 in.) This consortium project, underway in South Africa since 2009, involves Aerosud aeronautics company and the National Laser Centre at the South African Council for Scientific and Industrial Research. The team has been developing a large-scale, high-speed selective laser melting system to enable manufacture of large components for the aerospace industry. Powdered materials being evaluated include titanium, Inconel and steel alloys.
- Thermwood - AMS (3048x3048x1524 mm; 120x120x60 in.) Noting interesting opportunities in the AM World, Thermwood, a US manufacturer of large CNC equipment, is adapting its Model 77 semi-enclosed gantry machine to include a six-axis, articulated thermoplastic-extruder head. It will print near net shape components made from carbon graphite reinforced composite materials.
Subscribe to our FREE magazine,
FREE email newsletters or both!Latest News
About the Author

Pamela Waterman worked as Digital Engineering’s contributing editor for two decades. Contact her via .(JavaScript must be enabled to view this email address).
Follow DE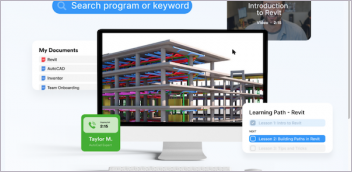

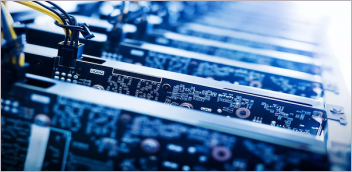
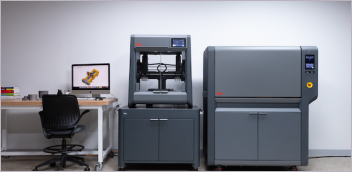