3D Printing Takes Off
Latest News
January 1, 2015

The pressure is on aerospace companies to reduce the weight of their planes while ensuring safety and quality. Manufacturers are increasingly turning to new materials and technologies to lighten the load, including rapidly evolving 3D printing and additive manufacturing solutions.
When Airbus Group Innovations partnered with EOS to compare rapid investment casting and direct metal laser sintering for the production of an Airbus A320 nacelle hinge bracket, they found that using direct metal laser sintering (DMLS) to build the hinge out of titanium could reduce the weight per plane by as much as 10 kg because of the lattice structure used in the hinge. The additive manufacturing process also used less total energy, reduced material consumption by 25%, and even reduced CO2 emissions by nearly 40% over the lifecycle of the hinges.
“The door hinge had a bulky design, and it was a low-volume manufacturing item for multiple locations on the plane,” says Andrew Snow, senior vice president at EOS North America. “Using the lattice structure, we could maintain mechanical integrity while reducing weight. And it’s a design that can only be manufactured additively.”
3D printing was initially seen as a way for aerospace, automotive and other manufacturers to create rapid prototypes or molds. Now, new additive manufacturing techniques and materials are making it possible to create lightweight end-use parts. While many of these parts are for interior areas of planes that are not subject to extreme stresses, printed parts are working their way into vehicle bodies, as well as being incorporated into jet and rocket engines.
Printed parts can reduce weight, cost and complexity. “Anything that helps on the assembly side is going to be worth the implementation process, because the return on investment is through the roof,” says Chris Holshouser, senior manager, Vertical Solutions, Stratasys.Lighter Parts at Lower Cost
The expansion of additive techniques into end-use components is enabled, in part, by the addition of techniques like electron-beam melting, and the increase of available materials like titanium, ceramic, resin and thermoplastics to generate production-grade aerospace parts.
“The printing technique and the materials are very tightly coupled advancements,” says Tom Charron, vice president of Product Marketing at 3D Systems. “That’s why companies like 3D Systems develop the materials and printers together. It’s not like injection molding, where you can put lots of different plastics into a mold. Printers have engineered material specifically for what they are doing, as a general rule.”
Additive manufacturing can reduce costs by eliminating tooling and production expenses, provide additional manufacturing flexibility by reducing tooling required for injection molding or casting, and most importantly, provide lighter weight components. A printed part can be made with a hollow or latticed interior structure that reduces the amount of required material, and cuts down weight while maintaining strength and durability. Manufacturers can also create more complex geometries.
“Mass customization is also a big driver of 3D printing,” Charron says. “There is no cost difference between printing one or one thousand different pieces. Every one costs the same.”
Companies across the aerospace industry have launched 3D printing projects, and many have already incorporated these parts into aircraft. At GE Aviation, engineers are testing cobalt-chromium alloys (traditionally used for joint replacements and dental implants) to use for printing nozzles and other jet engine components. GE has been able to print the nozzle using direct metal laser melting, and created a nozzle that is 25% lighter and five times more durable than the current nozzle (which is made from 20 different components). The process can take up to 120 hours and requires a massive amount of computing power to monitor construction of the part.
Honeywell has its own 3D printing program under development. Boeing has produced thousands of 3D-printed parts, including 30 components in the Dreamliner.
These printing efforts aren’t always targeted at lightweighting. In early 2014, BAE Systems produced and certified the first replacement part for the BAE 146 regional jet using additive manufacturing, a plastic window breather pipe. The pipes were previously injection molded, but the tooling for the pipes was no longer available. New tooling would have taken several months and nearly $25,000 to develop. The printed parts cost 60% less than manufactured parts. (The company has also produced some 3D printed parts for the Tornado GR4 fighter jet.)
BAE’s experience points to one of the major advantages of additive manufacturing: the elimination of tooling and molds that can add months or even years to a production schedule.
“If you look at the whole process, it may take several seconds to injection mold a part that takes an hour to print, but you have to consider the two and a half months it took to make the tooling for injection molding, and you don’t have to store that tooling,” Charron says. “If you make a design change, it doesn’t cost you anything, because you don’t have to change the tooling.”
Additive manufacturing also has other advantages over machining or molding. “It’s hard in machining to add material back if there is a problem,” Stratasys’ Holshouser says. “With additive, you can take action to save a long build-time part.”
Unitization Reduces Weight
In many cases, printed parts can be produced in one or two pieces, greatly simplifying the assembly process and reducing weight by eliminating rivets and adhesives. “Unitizing an assembly into one component saves labor, and that’s an important benefit,” Holshouser says. “There are limitations to that, but the design freedom you get with respect to additive lets you make extremely complex parts without incurring a lot of cost.”
New materials have also helped with lightweighting. PEEK and PEKK high-temperature, high-performance polymers, for example, can be used to replace other heavier materials.According to Snow, the fiber optic single-model diode pump laser that EOS is using in its direct metal sintering solutions allows these systems to work with other types of metals. “We can work with traditional alloys now like Titanium 64. We can do super alloys, and the sky is the limit on stainless steel, so it has opened up a whole new plethora of materials,” he says. “That has been a key innovation.”
Holshouser says that there are now thermoplastic resin systems that can compete on specific strength with aluminum. “People don’t realize the capabilities and benefits of thermoplastics, and what you can do with them now,” Holshouser says. “There are ways to tailor thermoplastics to control conductivity or thermal passages. You can’t get that with metals. Thermoplastics are more tunable.”
3D printing companies have also gotten better at meeting tighter tolerances with a wider variety of materials. “We’ve gotten much better at controlling those tolerances and predicting how the material will react within the powder bed,” Holshouser says. “Before, we could process materials but not in a repeatable manner. You have to have that predictability for manufacturing.”
And because the technology can generate higher quality parts with these new materials, printing applications have moved into some of the most extreme applications in aerospace. NASA and Aerojet Rocketdyne recently conducted hot-fire tests on 3D-printed injector and thrust chamber assemblies using copper alloy materials, confirming the printed parts could potentially be used in space launches. NASA also tested printed injectors in August 2014 that could be used on the RS-25 engine for the planned Space Launch System (SLS) rocket. Those injectors can be printed and assembled using just two parts, compared to the 160 components needed for traditionally manufactured injectors.
In January 2014, SpaceX launched a Falcon 9 rocket with a 3D-printed main oxidizer valve body in one of the craft’s nine Merlin 1D engines. The valve is now qualified to fly interchangeably with cast parts on all Falcon 9 flights. SpaceX also tested a printed SuperDraco engine chamber, which could be used on the Dragon Version 2 vehicle’s launch escape system.
Innovations Move Tech Forward
To move from prototyping to end-use parts, 3D printer companies have had to modify their equipment and approaches to the manufacturing floor.
3D Systems, for example, in its new ProX 400 direct metal 3D printer, has separated the pre- and post-processing steps from the actual printing. “That way you are purely printing, and as soon as the part is done it can be moved out of the printer and into a separate de-powdering unit that does the post-processing,” Charron says. “You can use the print volume more efficiently that way and increase throughput.”
3D Systems also developed a high-speed, continuous fab-grade printer for high-volume, customized printing of plastics that moves the print beds at high speeds beneath print heads.

Throughput and production efficiency will be critical for expanding additive manufacturing in aerospace. “People have applications that they want to adapt to additive, but it can be cost prohibitive because of the speed of the technology,” says Snow at EOS. “We’re trying to bring the ROI (return on investment) for the customer into place via innovations that increase productivity of the technology. We’re looking at new ways of delivering the laser beam to the powder bed, and at multi-laser solutions to better meet the needs of the applications for production.”
Those multi-laser systems would use multiple lasers with multiple fields in a single build envelope to increase throughput. “That would be most beneficial for larger part applications where a single laser solution takes a long time to complete a build,” Snow says.
Design Challenges
For aerospace companies that want to use 3D printing to reduce weight or costs, the biggest challenges may not come from the technology or materials, but from the design side.
To successfully print a part, these companies need engineers that can design for additive manufacturing, and software that can fully leverage the technology. “Engineers don’t know how to design for it,” Holshouser says. “It wasn’t available to them before. We can create internal lattices with our solutions, for example, but you need a CAD expert to go in and create these structures in the design. The disruptive nature of additive is further along than the know-how available to utilize it.”

“Adoption of additive for end use manufacturing on a large scale will require a rethinking of how parts are designed,” Charron says. “Today every engineer out there is used to designing for the manufacturing processes. The software works the same way. Now you can design things in ways that are very different.”
That will require a large-scale education effort within aerospace and across engineering schools. “That’s our biggest challenge, showing engineers how to design with additive in mind,” Snow says. “We’re making some headway as the industry brings awareness of the design rules of additive and what is possible, and more and more college curriculums have the technology.”
“There are pioneers who are starting to think differently and take advantage of additive manufacturing, but I think most companies have not seriously thought about changing how they do production to take advantage of the technology,” Charron says. “That will be a huge part of the way the industry moves forward over the next five or 10 years.”
More Info
Subscribe to our FREE magazine,
FREE email newsletters or both!Latest News
About the Author

Brian Albright is the editorial director of Digital Engineering. Contact him at [email protected].
Follow DE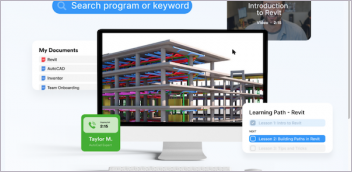

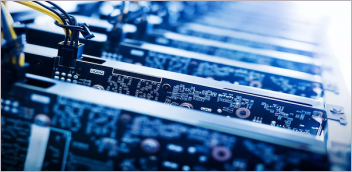
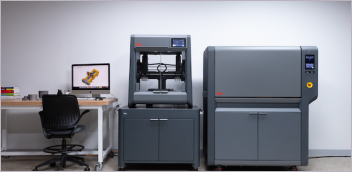