3D Printing Researchers Use Glass to Open a Window into the Future
Glass is a bio-friendly, bioresorbable, and low-cost alternative to other materials.
Latest News
January 3, 2010
By Susan Smith
Glass is a tantalizing substance in the realm of materials—one that researchers have often wanted to use for various applications. But no one has come up with a way to print glass in 3D. Until now.
![]() The “salt” grains on this organic shape are white industrial sapphires (Al203 corundum) and are used as a high-temperature sintering bed. Depending on the kiln firing process, they will either stick to the parts or not. Image courtesy of Mark Ganter |
Geometry researchers at the University of Washington’s (UW) Solheim Rapid Manufacturing Laboratory on the university’s Seattle campus have developed a process by which they can print glass in 3D. The “vitraglyphic process” is a follow-up to the Solheim Lab’s success last winter printing with ceramics.
Mark Ganter and Duane Storti, both UW professors of mechanical engineering and co-directors of the Solheim Lab, have spent 10-15 years developing math, methods, and algorithms to represent geometry within computers. The next step, then, was to create physical models of geometry.
“We first developed the ability to be able to represent objects that were not easy to make,” says Ganter. They tried equipment from a firm called Ballistic Particle (which went bankrupt), followed by an attempt to use an early manually layered object-manufacturing machine. Ganter says eventually they gave up their summer salaries to buy one of the earliest Z Corporation machines developed, a model 402.
![]() Three SW pots in a new glass using Vitraglyphic process. Image courtesy of Mark Ganter |
There were two big reasons for going with the Z Corp equipment. According to Ganter, it used materials that were “less costly” and “we didn’t like the toxicity of the SLA approach.” Also, the printer was among the fastest then on the market.
“Once we got the technology we saw how much excitement it created in students and in other researchers,” says Ganter. “Nevertheless, we weren’t as interested in being involved in that as in our research area. We partnered with what is now ExOne Corp.” ExOne, a subsidiary of ProMetal, had a Z Corp-style machine. As part of the partnership, Solheim began to experiment with how to print aluminum mixtures, silicon carbides, and silicon nitrites.
One of UW’s grad students, Ben Utilla, wrote a thesis called “How to Print Anything with a 3D Printing Process,” describing approaches to 3D printing in a wide range of materials. The common element, according to Ganter, is working with particles around 20 microns. Then it is a matter of finding binders and fillers to create the reactions that allow the particles to adhere during the build phase and to display desired performance characteristics after post-build processing, such as sintering or infusion with other materials.
UW now has four machines in its lab— each running a different material. The lab continues to develop new materials; they have 25 currently. “I tell people jokingly I’ll stop this quest when I have 1,000 new materials,” says Ganter. “Anything that works for ceramics we can print with. Commonly you can get 20-25 different kinds. I’m pretty sure any glass you can get would be printable. It’s simply a question of my being able to get a firing protocol for it.”
Getting into Glass
Ganter blows glass as a hobby and he’s passionate about its properties and possibilities. “It is a fundamental material type … if you think of materials, there are metals, ceramics, glass materials, plastics, polymers … so there is only a set number of materials, broadly speaking. Glass is a category with which people in mechanical engineering don’t much work.”
![]() “Valve 43” is a sculpture created by Meghan Trainor, a graduate student in the UW’s Center for Digital Arts and Experimental Media. She designed the piece in Rhino 3D and was the first to use the new Vitraglyphic process to produce objects other than test shapes. Image courtesy of Meghan Trainor |
Glass can be transparent or opaque. It is distinguished as an inorganic material that solidifies from a molten state without the molecules forming an ordered crystalline structure. Because its molecules remain in a disordered state, glass is technically a super-cooled liquid rather than a true solid.
Ganter likened 3D printed glass to pate de verre, a 400-year-old technique for creating glassware that is basically a “paste of glass.” In pate de verre, glass powder is mixed with a binding material such as egg white or enamel, placed in a mold and fired. Dating from early Egyptian times, the technique is revived with 3D printing.
Because glass powder doesn’t absorb liquid easily like ceramics, the 3D printing approach had to be altered.
“When we used glass powders, our normal process to print objects resulted in gelatin-like parts,” says mechanical engineering graduate student Grant Marchelli, who led the experimentation. “We had to reformulate our approach for both powder and binder.”
By adjusting the ratio of powder to liquid, the team found a way to build solid parts out of powdered glass (purchased from Spectrum Glass in Woodinville, Wash). Their successful formulation held together and fused when heated to the required temperature.
“We also know that making porous glass objects with these holes that are 20-80 microns in diameter is in the right range for growing biological objects that are implantable, because cells will grow in them,” says Ganter. Indeed, another UW bioengineering researcher is working on that application.
Bio-Friendly
Glass is a highly appealing research domain because there is an entire spectrum of glasses that are “bio-friendly.”
“I could take a piece of sterilized glass and implant it under your skin and it would be fine. The human body just isn’t bothered by glass at all,” says Ganter, adding that researchers have placed a glass heart in the middle of the chest, the skin stretching to accommodate it, without the body rejecting it. “There are some glasses that are actually bio-absorbed,” says Ganter, “dissolving over a period of months in the human body. I know they exist, and I’m very confident we’ll be able to print them as soon as we can find a supplier.”
Although 3D printing with cells to produce replacement body tissues is still highly experimental, the development of 3D printing with glass opens up new directions for interactions between cells and glass.
Low Cost Materials
Ganter says using glass and ceramics is very inexpensive. Powdered recycled glass is available in most large cities and all that is necessary is to mix the powder, pour it in the machine, and see how it works. The glass is pink in pre-firing and gray in the post-firing stage.
Using his own binders formulated at UW, Ganter can make color products using the Z Corp monochrome machines. The recycled supplies sell for $1 per pound; specially formulated binders for most rapid prototyping machines would cost around $30-$50 per lb.
![]() The Solheim Lab at the University of Washington uses early Z Corporation 3D printers in its experiments with materials. Image courtesy of Mark Ganter |
Applications
Custom glass formulations are used extensively in semiconductor manufacturing, as well as in building supplies. Possible applications include: art, architecture, medical, and dental.
Howard Kuhn (former director of research for the Ex One Company) says that while infiltrations have worked with a number of glass and porcelain systems, nothing has been refined to the point of being commercially viable.
Joe Titlow, director of product management for Z Corporation, says his company has done a lot of research in the area of 3D printing of glass in the past. “Our experience to date has been that it is pretty easy to get something that kind of works that will piece together glass particles,” he says. “What is difficult, and what we haven’t yet found a solution for, is making what we think would be a viable product in this space, something that would actually be able to perform like glass and look like glass.”
EOS laser-sintering systems do not create glass parts at present, according to the company. The closest they have come is their material PA 3200 GF, a glass-filled fine polyamide that is used for applications such as housings and thermally stressed parts.
Assistant professor of architecture at the University of California, Berkeley, Ronald Rael, is working on new kinds of ceramic bricks that can be used for evaporative cooling systems. “3D printing in glass has huge potential for changing the thinking about applications of glass in architecture,” Rael says. “Before now, there was no good method of rapid prototyping in glass, so testing designs is an expensive, time-consuming process.”
With 3D printing, one can insert different forms of glass to alter the performance at positions specified by the design.
Properties
The challenge now is to do the engineering work to characterize the properties of new materials for 3D printing. What the glass might be used for depends upon its strength and porosity.
Solheim Lab researchers are still working to get a handle on porosity and will begin strength testing within three months. “We print a 10 ml x 10 ml x 100 ml bar and the first thing people want to do is try to break it,” Ganter says. “The last run we did, the grad student who made it couldn’t break it in his hands.”
At the Lab, they print cylinders similar to two stacked hockey pucks, then test their resistance to crushing. Those that pass the test can be used as building materials.
The finished glass material looks “more like sugar,” and is porous. “You’re looking at mostly glass-air boundaries,” says Ganter. “If you take a glass and crush or break it, the powdery stuff looks pretty white.”
Possibilities Ganter sees for the porous materials include filters or liners for containers that should not slosh. Tanks that might be filled with a glass foam chemically neutral to whatever else you fill it with would be ideal. You can soak the glass with gasoline, for example, and the gas won’t drip out. In chemical engineering, porous glass is used for filter or reactor applications, where there may be a chemical reaction within a vessel.
Glass holds a lot of promise as a low-cost material for use in many different capacities. The ability to repurpose used glass in 3D printing for new products, and the bio-friendliness of glass, make it appealing to a manufacturing industry that is charged with finding ways to recycle, repurpose, and use non-toxic and dissolvable materials.
As designers, artists, and manufacturers become increasingly aware of the breadth of uses for glass and 3D, it should find its way into more applications as a low-cost alternative.
More Info:
EOS
Solheim Rapid Manufacturing Laboratory
University of Washington
Contributing Editor Susan Smith is DE’s expert in rapid technologies and has been immersed in the tech industry for more than 17 years. Send e-mail about this article to [email protected].
Subscribe to our FREE magazine,
FREE email newsletters or both!Latest News
About the Author

DE’s editors contribute news and new product announcements to Digital Engineering.
Press releases may be sent to them via [email protected].
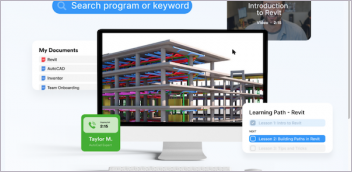

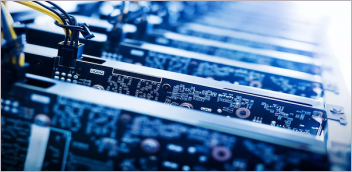
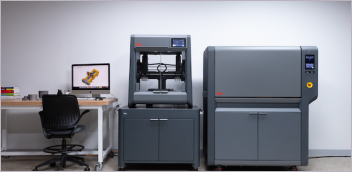