3D Implants for Head, Face Injuries

Latest News
November 22, 2016
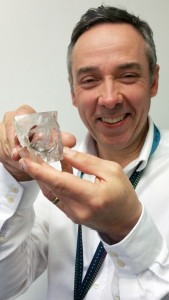
Creating implants for head or facial injuries is often time consuming and in some cases imperfect. CT scans can be used to create custom implants, but getting the implants manufactured can take a long time—longer than some patients can wait. 3D printing is an obvious solution, but for healthcare organizations not versed in design, these solutions may be too complex or expensive. Researchers in Wales have developed a 3D printing software to help doctors treat patients with head and face injuries using custom-fit titanium implants, and do so quickly and relatively cost effectively.
Morriston Hospital in Swansea is leading the ADEPT project—Additive-manufacture for Design-led Efficient Patient Treatment. The maxillofacial team at Morriston is working with PDR at Cardiff Metropolitan University, printer manufacturer Renishaw and additive manufacturing specialist LPW Technology.
The project was funded by Innovate UK and the Engineering and Physical Sciences Research Council.
“The software will enable maxillofacial surgeons and technicians to design a cranioplasty—where people have part of the skull missing and you want to repair that with a metal plate,” said Peter Llewelyn Evans, Morriston maxillofacial laboratory services manager. “Similarly, if someone has a fracture to the floor of the eye socket—what we call a blow-out fracture—perhaps from a punch or a fall, you can repair that with a custom-made metal plate.”
Traditionally, doctors use off-the-shelf implants that have to be bent and reshaped to fit the patient. In some cases, they send injury scan data to a third-party manufacturer for a custom implant, which can delay the arrival of the implant by weeks or months.
The ADEPT system allows doctors to quickly product an implant on site. Renishaw makes the 3D printers for the solution. According to Evans, the software and hardware operate as a single platform.
Physicians can use CT scan data to design the implant and then use that design for the 3D printing component. The printing process can begin immediately once the design is finalized.
The software is being tested and will move into a trial phase soon. The researchers and their partners presented the software at the Collaborate to Innovate Conference on November 17.
Source: Wales Online
Subscribe to our FREE magazine,
FREE email newsletters or both!Latest News
About the Author

Brian Albright is the editorial director of Digital Engineering. Contact him at [email protected].
Follow DE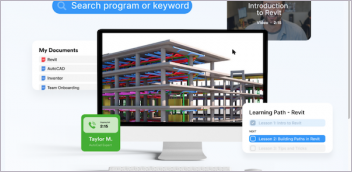

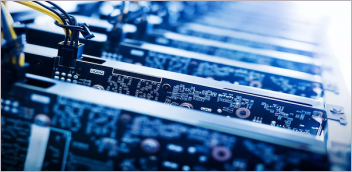
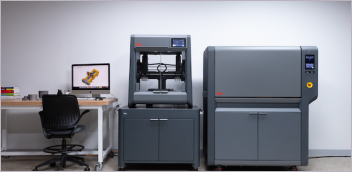