Latest News
December 21, 2012
The diet industry and the computer-aided engineering (CAE) segment are heading for a head-on collision, at least in their terminologies. They both share a similar objective too: Like Jenny Craig and WeightWatchers, CAE software programs are now on a quest to help you lose weight. To be precise, more and more of these software are introducing ways to help you shave off materials, or excess weight, from your design. (For more, see “The Twin Forces of Optimization & Inspiration” in December 2012 issue, now available online.)
NX 8.5, the latest release of Siemens PLM Software‘s premiere design and engineering suite, joins the weight-reduction craze with the debut of Topology Optimization. In this process, you begin by defining a region in your design—a specific block of geometry, most likely a part—you’d like to optimize. The idea is to see if you can redesign the part with less material, but still make sure it can withstand the anticipated loads and stresses.
The topology optimization tools are intended for designers, not specialists. Accordingly, NX 8.5 offers a guided approach to optimization. In order to identify where you can shave off materials, you must first understand the stress concentration. That calls for simulation. Now you can probably understand why optimization and simulation go hand in hand. The inputs required for optimization in NX are quite similar to those required for a simulation job: identifying fixed points, specifying loads, and so on. In fact, the optimization exercise is based primarily on a linear static analysis of loads and stresses on your part. The primary difference is, in optimization, you specify a target weight reduction: say, 30% of the current part’s weight.
Once you have the inputs in place, the software can solve the optimization scenario, just like it would a simulation task. In simple terms, the software is examining every element (or mesh) to see if it’s critical to counteract the load expected. If not, then that’s a candidate for weight reduction. If you’re running optimization on a complex part and need additional computing power (more than what’s available in your desktop or laptop), you may tap into a high-performance computing (HPC) server. NX 8.5 allows distributed computing in its simulation functions. Keep in mind that you need a mesh-model to optimize its weight or volume, so it works primarily on single parts. If your desire is to optimize an assembly (not a very likely scenario), you’ll have to somehow reduce the entire assembly into a mesh model to study it.
The outcome resembles—well, there’s no easy way to describe it in words—a jagged blob. That’s because the software doesn’t make aesthetic judgment when it singles out areas to shave off materials. It’s pure math, translated into geometry. It’s up to you to examine the proposed topology, then fashion a part that can be manufactured and also appeal to your target consumers. You can export the proposed shape as STL into your design environment.
The process of topology optimization in NX is quite similar to the process employed by Altair Engineering’s SolidThinking Inspire. (For a review and a video demo of Inspire, read this blog post.) It suggests certain standard protocols may be emerging from optimization. It points to a future where most designs will be lighter, produced with leaner, tighter topology. For the weight gain resulting from overeating during holidays, however, you may have to find optimized outcome in a gym near you.
Subscribe to our FREE magazine,
FREE email newsletters or both!Latest News
About the Author

Kenneth Wong is Digital Engineering’s resident blogger and senior editor. Email him at [email protected] or share your thoughts on this article at digitaleng.news/facebook.
Follow DE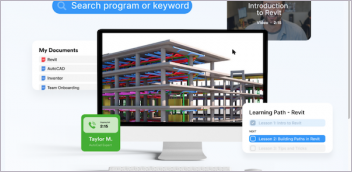

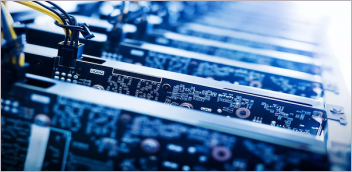
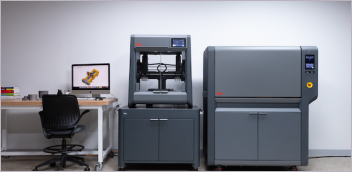