Rize One Brings Zero Post Processing to the 3D Printing Experience

The Rize One’s patented APD technology and Rizium One thermoplastic filament pair for a zero post processing 3D printing experience. Image Courtesy of Rize
Latest News
July 20, 2016
For all the hoopla over 3D printing’s blossoming role in product design, the reality is that the difficult and oftentimes, dirty, post-processing routines have limited the technology to certain use cases.
Rize Inc., a startup founded by former Objet and Zcorp 3D printing pioneers, has launched from stealth mode with a new 3D printer that stakes claim to being the first zero post-processing offering on the market. What does that mean exactly? Well, each 3D printing technology has its own set of hassles related to prepping parts once they’ve actually been printed. The need to remove support structures and deal with messy materials and powders is fairly universal across technologies, which makes many 3D printers not particularly well suited for office environments. In addition, the post-processing work is labor intensive, which injects unnecessary time into the overall design process.
Buoyed by a slew of patents, the Rize One aims for a different post processing paradigm — one that is easy and requires little to no hands-on intervention by users. The new 3D printer, the Rize One, is architected with patented Augmented Polymer Deposition (APD) technology, which integrates jetting and extrusion capabilities to allow the printer to do things more easily, including offering support for color and most significantly, easy support removal. Also key to its zero post-processing promise is the new Rizium One patented engineering- and medical-grade thermoplastic filament, which allows users to release a 3D printed part from the support structures quickly without requiring any subsequent filing or sanding work.

“There’s a lot of processes that go on after a part is printed that are really swept under the carpet and severely limit the use of 3D printing today,” says Frank Marangell, president and CEO of Rize. “It’s an easy concept — we put something between the support and materials that says ‘don’t stick to me,’” he says. “It pops right off and is amazingly simple.”
Rize One, which is in beta now and slated to ship later this year, is targeted to professional engineers and product designers, not hobbyists or home users. The printer is designed to be a more accessible platform for prototyping proof of concepts, doing fit and functional testing in real-world conditions, creating end-use productions parts and tooling, and as an alternative way to output manufacturing fixtures and jigs.
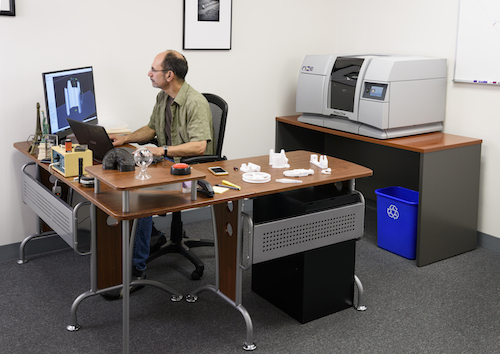
As part of the APD process, the printer’s print head channels jet the Release One repelling ink between the parts and the support structures, which helps release the bond between layers and makes support removal fast and clean. The same process also allows for real use of color while the precision ensures 3D printed text and images can be output on parts, Marangell says.
With zero post-processing work, the Rize One claims to reduce part turnaround time by 50% while cutting costs and improving part strength.
Reducing development time is particularly critical to expanding the use of 3D printing at Reebok, according to Gary Rabinovitz, additive manufacturing lab manager at the sporting goods giant. His lab has five additive manufacturing systems in house with only two people supporting them. “It makes it difficult to stay on track if we spend too much time on the post-processing steps,” he says. “We do hand off really good quality parts, but with a dedicated person to do the post processing, we could offer much more.”
An office-friendly system with no post processing like the Rize One would also get parts in the hands of those needing to make quick decisions much faster. “Reebok has been a part of the AM/3D printing community for the past 19 years and post processing has been the biggest issue for us,“Rabinovitz says. “The Rize One will certainly be a welcomed change.”
Watch this video to see how the Rize One’s zero post processing works:
Subscribe to our FREE magazine,
FREE email newsletters or both!Latest News
About the Author

Beth Stackpole is a contributing editor to Digital Engineering. Send e-mail about this article to [email protected].
Follow DE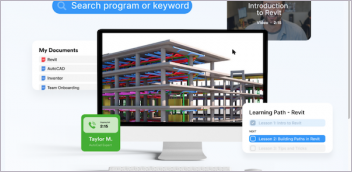

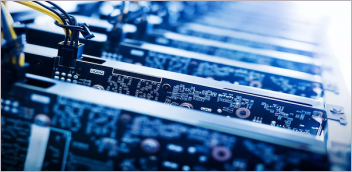
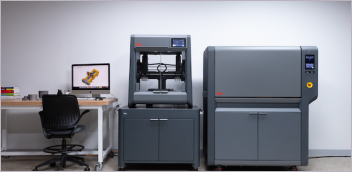