Mission Accomplished: NASA Emails, 3D Prints Wrench Design in Space

Made In Space’s Zero-G 3D printer output the wrench aboard the International Space Station. Image Courtesy of Made In Space
Latest News
December 30, 2014
What does an astronaut do when they need a ratchet wrench during a mission aboard the International Space Station (ISS)? Turns out, they can now 3D print said wrench or any other similar part thanks to a recent experiment between NASA and Made in Space, a company contracted to build a 3D printer specifically designed for space operations.
NASA took delivery of a Made In Space 3D printer on the International Space Station in November and successfully output multiple replacement parts. This latest endeavor takes things a step further as the ratchet wrench was the first “uplink tool,” meaning the design file was emailed to the space station and printed on demand during the actual space mission.

The wrench, measuring 4.48 in. long by 1.29 in. wide, was designed by Made In Space and output on its zero-gravity printer by depositing 104 layers of plastic in four hours. Made In Space engineers created a 3D model of the wrench in Autodesk Inventor, converted it to G-code, and later emailed it through NASA’s Huntsville Operations Center to the ISS team for output — a first in a design workflow that NASA hopes will become routine, especially for longer journeys like those to Mars.
Prior to this experiment, all objects 3D printed in space has been previously been printed on the exact same printer before launch to increase the chances of success, according to a Made In Space blog post. Additionally, backup files of all the 3D printed models have been available on an SD card that was launched into space with the Zero-G printer.

“E-mailing a part to space opens up space to everyone around the world,” said Aaron Kemmer, Made In Space CEO and co-founder. “Just a few months ago, if you wanted to have something in space, the only way to get it there was by launching it on a rocket, which could take months, or even years. Now, with a few clicks of a mouse and an e-mail, anyone can have their item in space, in a matter of minutes.”
Typically, it takes months — or even years — to get replacement or resupply equipment to space and there is a rigorous review process required before any item can be shipped to the station. This experiment, which tested the ability to transmit a file in email to the space station, could dramatically alter that process, allowing space teams to resupply items that were previously impossible, Kemmer said.
Before any of this can become mainstream, NASA is doing rigorous testing to explore how a microgravity environment impacts how objects are designed and built in space. Using the Made In Space printer, the team produced objects from 13 different designs in space, most preprogrammed into the printer before it departed Earth.
The plan calls for those objects to be compared against comparable objects made on the ground with the same printer, to explore the effects of microgravity on the 3D printing process and the finished printed parts. The team will put the objects through structural and mechanical testing as part of the comparison of samples.
Once testing is complete, NASA hopes to routinely 3D print science equipment in space, rather than having to conduct resupply launch missions. According to Made In Space, this type of technology will translate into lower costs for experiments, faster design iteration and a safer, better experience for crew members.
Yet Kemmer said the real impact comes when it’s time for human space exploration beyond the Earth’s orbit. “The Made In Space vision is to make human beings a multi-planetary species,” he explained. “Me and my co-founders created the company because we realized space has a supply chain problem — it’s really difficult to get things from A to B in space.”
Check out this video to hear more about NASA’s vision for 3D printing and how emailing designs to space can be a game changer.
Subscribe to our FREE magazine,
FREE email newsletters or both!Latest News
About the Author

Beth Stackpole is a contributing editor to Digital Engineering. Send e-mail about this article to [email protected].
Follow DE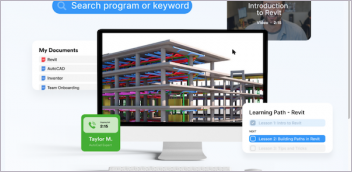

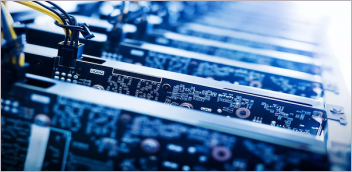
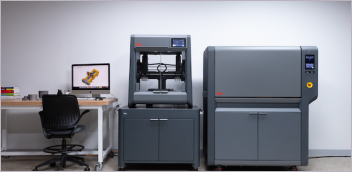