
The spike plate for this pair of New Balance track shoes was built using AM. Courtesy of EOS.
Latest News
December 10, 2014
It’s sometimes easy to forget that athletic competition spurs competition between the big businesses that want to sell you shoes and equipment. As with every competition, the competitors are always looking for an advantage. Sometimes that advantage is a celebrity endorsement, and sometimes it’s a technological breakthrough.
New Balance was founded in 1908 and is still based in Boston. The technology behind shoe design has changed radically in the 100-plus years the company has been in operation, and the newest technology pushes those changes even further. Additive manufacturing (AM) offers New Balance the chance to quickly and efficiently produce customized shoes for its team of elite athletes.

For those unfamiliar with track shoes, they differ from standard running shoes in a few areas. Track shoes tend to be lighter, and have spikes to improve traction. The spikes are mounted in spike plates that make up the bottom of a track shoe. The design and configuration of spike plates can have a large impact on a runner’s performance. New Balance has decided to use AM to produce custom plates for each athlete.
The custom design process begins by gathering data about how each runner moves on the track. New Balance collects each runner’s biomechanical data using a force plate, in-shoe sensors, and a motion-capture system worn by the runner. The data is analyzed to determine the best possible spike plate configuration for the runner, and the results are plugged into CAD to be printed on an EOSINT P 395, produced by EOS. The end result of the process is a track plate fit to each athlete, and at a 5% reduction in total weight as a bonus.
“There are so many great things that came out of this process, compared to the methods we used in the past to develop and manufacture products,” said Sean Murphy, senior manager of innovation and engineering at New Balance. “This is a totally unique situation where we come away with the runner’s data, generate multiple plates we feel will meet their needs, and actually provide several pairs of track spikes for them to try simultaneously. It’s great to be able to have them identify and respond to each different variation that we produce.”
So how have the shoes performed on the track? Kim Conley, a member of Team New Balance and a US Olympic runner, began testing the process with New Balance in 2012. Since then she’s run personal records in both the 3000m (8:44.11) and 5000m (15:08.61) while wearing the custom spike plates.
“My shoes are critical to my performance. They’re the most important piece of equipment I have,” said Conley. “As a professional runner, you obviously want the most effective and comfortable spike plates for competition. For me, these are the ones New Balance designed based on the curve running data their development team had collected. They provide better traction and less pressure on the outside of my foot, which allows me to focus on my race plan and not worry about my spike plates.”
Below you’ll find a video about New Balance’s 3D printing program.
Source: EOS
Subscribe to our FREE magazine,
FREE email newsletters or both!Latest News
About the Author
John NewmanJohn Newman is a Digital Engineering contributor who focuses on 3D printing. Contact him via [email protected] and read his posts on Rapid Ready Technology.
Follow DE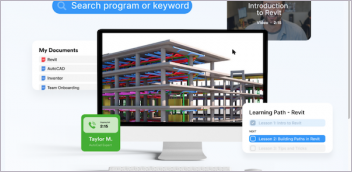

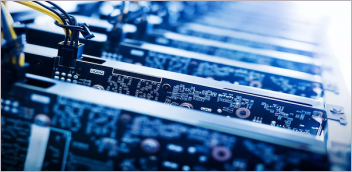
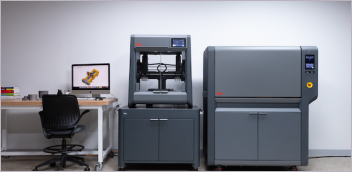