Point-Counterpoint: Additive vs. Subtractive Rapid Prototyping
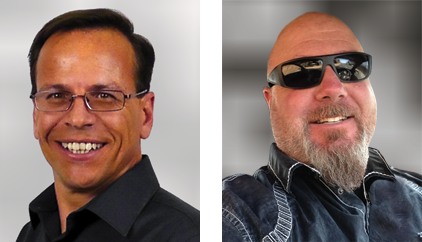
For additive technologies: Todd Grimm, founder and president of T. A. Grimm & Associates, Inc. (left). For subtractive technologies: Anthony Graves, Autodesk product manager for HSMWorks (right).
Latest News
September 3, 2013
As Desktop Engineering’s Senior Editor Kenneth Wong illustrates in “A New Look at Subtractive Prototyping,” there is plenty of room in upfront design engineering for both additive and subtractive rapid prototyping technologies. To have a little fun pointing out the strengths and weaknesses of both technologies, we decided to pit Todd Grimm (representing additive) against Anthony Graves (representing subtractive) in this point-counterpoint arena. While both Grimm and Graves see the value in using both approaches, we asked them to pick a side and come out swinging.
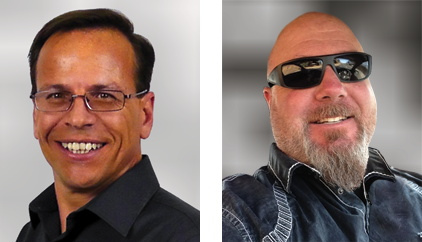
Point: Additive manufacturing is capable of making complex, intricate and delicate parts and products that subtractive techniques cannot.
Todd Grimm: What is impractical or impossible with subtractive manufacturing is encouraged with additive manufacturing. Instead of reviewing a design to decide if it is possible and how to approach the machining operations, additive manufacturing allows you to print virtually anything that the mind can conceive.
In the impossible category, additive manufacturing can reproduce internal, S-shaped channels; deep, narrow slots; tall, thin walls; and deep undercuts. And that is just the tip of the iceberg. There is no need to contemplate how to reproduce complex, intricate or delicate features. They are simply a given with additive manufacturing.
In the impractical category, include all the design features that add excessive time and cost to the machining operation. With additive manufacturing there is rarely a negotiation between design (complexity) and manufacturing (time). In the subtractive world, especially for prototypes, the question “Do you really need that?” is common.
In the additive manufacturing world, the time and cost equation is turned on its head. For example, adding features can actually decrease both. With subtractive manufacturing, every hole, pocket or slot increases time and cost. With additive manufacturing, they remove material, which decrease build time and material consumption.
Counterpoint: Subtractive manufacturing is capable of producing a high volume of finished parts.
Anthony Graves: While 3D Printing is almost always the go-to-technology when it comes to rapidly prototyping complex parts and assemblies, there is simply no substitute for CNC machining when it comes to producing large volumes of parts out of metals, plastics, and wood. Very sophisticated multi-tasking CNC machines and horizontal machining centers designed for production machining are capable of producing thousands of parts a day.
Point: Subtractive manufacturing is faster than additive manufacturing, even for small runs.
Graves: Many parts produced today, even those with organic 3D surfaces, can be produced on CNC machines very quickly. As CAM software has evolved, more and more companies who once outsourced their machined parts are recognizing that they are able to produce parts in-house much faster when it comes to prototypes and even small production runs. The variety work holding options available today allows users to produce.
Counterpoint: Additive manufacturing requires little setup and can print multiple pieces simultaneously without intervention.
Grimm: Faster is subjective. If speaking of only the time spent cutting material, I agree that subtractive processes are generally, but not always faster. However, once we include all time, both productive and non-productive, the total elapsed time for additive manufacturing is hard to beat for one-offs and small batch production. Just minutes after a design is complete, the part(s) can be building…no CAM programming, no fixture making, no setups.
And once running, the process is automated and unattended. With subtractive processes, do you really trust your program enough to let a first run go unattended, or do you babysit the machine tool to watch for tool crashes? And how often do you have a single setup run? Even with an expensive 5-axis machine tool, you will need a second setup to make the bottom of the part.
Setups and machinist oversight means overnight and weekend runs of a machine tool aren’t going to happen unless you have staffing around the clock. So, it’s 4:45 p.m. on a Friday — with additive manufacturing, the part is complete the moment you walk in the door on Monday.
But let’s forget about all that and focus solely on multi-part runs, which are the hallmark of additive processes. You can put any combination of parts in a single run. Running in parallel, versus the serial subtractive approach, will always be faster and much more efficient.
Point: Additive manufacturing allows design engineers to quickly test multiple new ideas without waiting on a machine shop to ship a prototype.
Grimm: With additive manufacturing, two or more design revisions can be completed in less than a day. It is common practice to design, print, review, redesign and reprint a new concept in a single workday. This means that a design engineer will produce more iterations in a given period of time, leading to better designs.
That statement assumes a serial process (one revision at a time) and a centralized additive manufacturing operation that supports multiple design teams. But if we change the practice, the design process becomes even faster.
Put a desktop additive manufacturing equipment on a design engineer’s desk to make the process self-serve. Now there is no queue, no waiting for resources and no haggling to get a job expedited. Prototypes are cranked out as fast as the design ideas arise.
And what if the design engineer has two, three or four design ideas? With additive manufacturing, he/she can print them all at the same time and review them side-by-side to pick the best.
Counterpoint: Small subtractive manufacturing equipment can be used in-house, much like 3D printers, to produce prototypes on demand as well.
Graves: Depending on the complexity of the finished part or assembly, having the ability to machine parts in-house allows you to turn parts around faster and for less money than out-sourcing. It all depends on the type of part you are trying to produce and the job shops you have access to. And, unless you work specifically with a firm that specializes in rapid turn-around of machined parts, you will contend with the same market forces that drove you to purchase your own 3D printer in the first place; turn-around time, cost, and quality.
Point: Subtractive manufacturing techniques require less finishing than additive manufacturing techniques.
Graves: With today’s advanced CAM and machining technology there is usually zero work required after the machining process, with the sole exception being the occasional debur. Even large mold and die jobs that required a great deal of polishing and handwork in years past require little to no post-machining hand work. Today, most parts can be pulled off a machine, wiped off, and sent off to shipping, where they are sent directly to the customer or outside suppliers for additional processing like heat-treat, anodizing, etc.
Counterpoint: Secondary operations aren’t foreign to subtractive processes.
Grimm: At a cursory level, I grant that subtractive manufacturing makes parts with surface finishes and accuracies that match most product specifications. But secondary operations aren’t foreign to subtractive processes. Ever had to add post-machining grinding to match the product spec or do a deburring operation? Ever had to tweak mating parts in an assembly? Ever had to split a part, and then join the pieces to make shadowed or internal features?
With additive manufacturing, parts will never be split due to the complexities of the design. On the contrary, we promote combining multiple pieces from what has to be an assembly in the subtractive realm. This eliminates all of that secondary work.
Point: Subtractive equipment costs more than entry-level additive manufacturing equipment.
Grimm: Let’s assume a company is starting from scratch. It doesn’t’ have equipment, trained staff, facilities or supporting tools and equipment. In the world of additive manufacturing, companies can get started with a few thousand dollars, an electrical outlet and a day’s worth of operator training. With that tiny investment it can be cranking out models, prototypes, patterns and production parts.
As that company’s demand for additive manufacturing grows, a single trained operator can schedule, manage, oversee and run multiple machines.
Counterpoint: Desktop-sized and used milling/CNC machines are available at prices comparable to professional 3D printers.
Graves: Whether you are looking for an entry-level device for students, a prosumer level device for serious hobbyists and makers, or a full-on professional grade tool for prototyping or manufacturing, you can find a wide range 3D Printers and CNC machines for almost the exact same price. For example, most entry-level 3D printers run between $500 - $1500 for DIY quality and versatility. The same is true for your entry-level benchtop CNC milling machines. There are a wider variety of both devices found between the $5,000 and $15,000 price range. And, if you are looking for more versatility, flexibility, and performance, you can start your shopping around the $50,000 mark. With material, tooling, and accessories, you are looking at another $10,000 – regardless of whether we are talking about a 3D printer or a CNC machine. And, you can easily spend in the hundreds of thousands if your requirements are even more demanding.
Point: Material costs, variety and specifications are all benefits to subtractive manufacturing.
Graves: While today’s 3D printers are capable of producing amazingly intricate and durable parts from a wide variety of plastics – even in multiple colors, the machining process allows you to produce functional prototypes and finished parts in the widest range of metals, wood, and plastics. However, subtractive manufacturing should not be thought of as a replacement or alternative to additive manufacturing, but a complement. Having the right tool for the job is critical. Some parts and schedules and other factors dictate 3D printing be employed; others, CNC machining.
Counterpoint: Additive manufacturing techniques make use of a wide variety of materials, even multiple materials at once, and specifications are being standardized.
Grimm: I can’t argue cost. Yes, additive manufacturing materials are more expensive than those in bar or rod stock. That is one of the tradeoffs for a very fast, very efficient and very capable process.
But the statement on variety is erroneous. Additive manufacturing has more classes of material available than subtractive manufacturing. Are foundry sand, glass, building materials (e.g., concrete-like), electrical inks and biological materials candidates for subtractive manufacturing? How about rubber-like materials? All of these are possible with additive manufacturing. A review of all the material classes processed by additive manufacturing will prove that it actually offers a wider array of materials.
However, subtractive manufacturing does have the edge on the number of materials within each class and the number of options for a specific material. But as the years pass, we will see many more options. And I believe that we will also have materials that are unique to additive manufacturing; materials that can’t be machined, molded, cast or fabricated.
There is one other material advantage that we don’t have to wait for. Today, additive manufacturing can build a single part from multiple materials. So, if you want a rigid structure with rubber-like grips, you can just print it. Additive manufacturing has also created the concept of gradient materials: blending different materials at different ratios throughout a part. That is an unmatched capability.
What will help to accelerate new material development and adoption of gradient materials is standards. ASTM is actively working on these, and with them, we will have guidelines to qualify the characteristics and performance of additive manufacturing materials…guidelines that will facilitate more R&D and more adoption in the design and manufacturing communities.
More Information:
Subscribe to our FREE magazine,
FREE email newsletters or both!Latest News
About the Author

Jamie Gooch is the former editorial director of Digital Engineering.
Follow DE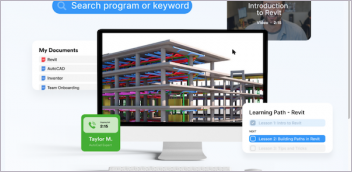

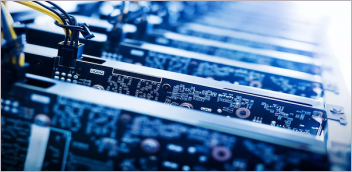
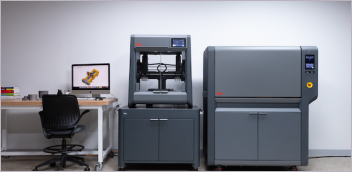