ESA Considers Moon Base Built Using Additive Manufacturing

Artist’s concept of what a 3D printed lunar base might look like. Courtesy of ESA.
Latest News
February 1, 2013
For people who look to the stars as the next great frontier of exploration, the moon figures prominently in their view. As exciting as a trip to Mars might be, returning to the moon is probably a more practical goal and could have a number of useful results. With all the scientific advances made since the last lunar landing, researchers could learn plenty about what it takes for humans to survive off-planet, just by hopping next door.
That kind of research does require a rather permanent presence, however, which means constructing a base of operations on the moon. Any construction on the moon raises some serious logistical questions. How do we get building materials to the site? Do we need to train construction workers as astronauts to build the base? And, most importantly, how much will all of that cost? It seems as though additive manufacturing (AM) may have the answers.
The European Space Agency (ESA) is investigating the possibility of using AM to construct a lunar base, using materials already in place. You may remember Rapid Ready reporting on an experiment that used crushed lunar rocks and a laser sintering process to build spare parts. The ESA wants to take that experiment a step further, and use lunar soil as fuel for the D-Shape process developed by Monolite UK.
Of course, you can’t just buy crushed moon rocks on eBay, so to test the theory, the D-Shape printer was fueled with basaltic rock mined from a volcano in central Italy that is 99.8% similar to lunar soil.
“First, we needed to mix the simulated lunar material with magnesium oxide. This turns it into ‘paper’ we can print with,” said Monolite founder Enrico Dini. “Then for our structural ‘ink’ we apply a binding salt which converts material to a stone-like solid. Our current printer builds at a rate of around 2 meters per hour, while our next-generation design should attain 3.5 meters per hour, completing an entire building in a week.”
The process was tested in a vacuum to simulate the lack of atmosphere on the moon. Researchers discovered D-Shape could work when the 3D printer nozzle was poked a couple of inches into the building material. The ESA has plenty of other challenges to overcome before this idea becomes a reality, but this presents a potential solution to the many logistical problems that might otherwise make lunar construction unfeasible or prohibitively expensive.
Below you’ll find a video that shows NASA’s 1986 experiment that investigated using lunar material to build a moon base.
Source: ESA
Subscribe to our FREE magazine,
FREE email newsletters or both!Latest News
About the Author
John NewmanJohn Newman is a Digital Engineering contributor who focuses on 3D printing. Contact him via [email protected] and read his posts on Rapid Ready Technology.
Follow DERelated Topics
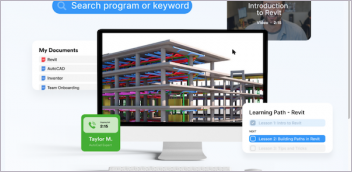

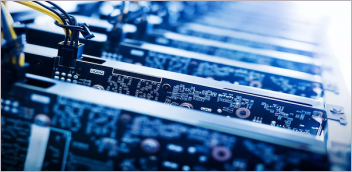
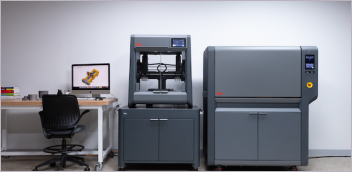