
Bedrich Benes, an associate professor of computer graphics at Purdue University and his collection of broken or improved 3D printed objects. Courtesy of Purdue University.
Latest News
September 19, 2012
Here’s an entirely plausible scenario involving a gift that was fabricated using additive manufacturing (AM). In the search for a unique gift, a tech-savvy customer goes online and searches through a website like Shapeways. He finds something interesting, modifies it to taste and orders the final product.
A short time later the gift arrives in the mail. The piece came out as our fictional customer had intended and he prepares to wrap it. As he’s packing it back up to wrap the object, he accidentally squeezes just a little too hard and part of the gift snaps off. Now he either has to repeat the entire process or try and repair the damage himself (which isn’t always possible).
That sounds like a bummer to me. Where professional designers take into account areas of a build that have a potential for easy breakage, amateurs aren’t likely to think about it. If this is someone’s first experience with AM, they are less likely to turn to the technology in the future and might also start telling his friends that 3D printed objects are garbage.
Researchers at Purdue University, working in tandem with the Advanced Technology Labs of Adobe, have created a program that identifies potential structural weaknesses in a design created for 3D printing and automatically makes changes to improve the durability of the object. The results of this research, led by Bedrich Benes, an associate professor of computer graphics, was presented in the paper, “Stress Relief: Improving Structural Strength of 3D Printable Objects” at SIGGRAPH 2012.
“I have an entire zoo of broken 3D printed objects in my office,” said Benes “It [the program] runs a structural analysis, finds the problematic part and then automatically picks one of the three possible solutions.”
The solutions mentioned by Benes are hollowing, thickening, or strut insertion. The program continues to analyze models even after making changes, working until it is satisfied with the structural integrity of the design. As an added bonus, the changes can also sometimes save on material costs.
“We not only make the objects structurally better, but we also make them much more inexpensive,” said Radomir Mech, senior research manager from Adobe’s Advanced Technology Labs. “We have demonstrated a weight and cost savings of 80%.”
Though designed for hobbyists, it seems to me that small companies that make frequent use of 3D printing could also benefit from using the program. It won’t take the place of advanced simulation and analysis software or physical testing, but it’s a start step in the right direction. The Purdue team plans on continuing its research efforts to examine how the AM process affects the structural strength of objects. They may also broaden the scope of the research to include 3D printed objects with moving parts.
Below you’ll find a short video that demonstrates the benefits of the program.
Source: Purdue University
Subscribe to our FREE magazine,
FREE email newsletters or both!Latest News
About the Author
John NewmanJohn Newman is a Digital Engineering contributor who focuses on 3D printing. Contact him via [email protected] and read his posts on Rapid Ready Technology.
Follow DE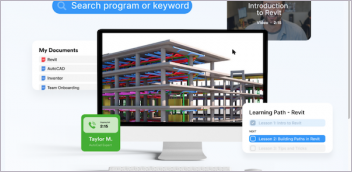

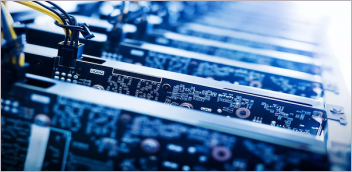
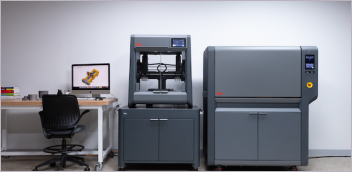