Rapid Ready Roundup: Aerospace AM, 3D Printing in the Cloud and Bobbleheads

Airbus’ vision of the future, featuring 3D printing. Courtesy of Airbus.
Latest News
July 12, 2012
In the course of my diligent efforts to keep you good people up to date on the state of additive manufacturing, I come across many interesting news items. I’ll gather them up every so often and present them in a Rapid Ready Roundup (like this one). You can find the last Roundup here.
I recently took a look at how additive manufacturing (AM) and the aerospace industry are interacting, but I’ve since come across more interesting information to pass along. Airbus is talking about using large-scale AM in the aerospace business.
Cabin designer Bastian Schafer has spent the last couple of years developing a concept plane that would be entirely fabricated using 3D printing. This idea would require a printer on a scale yet to be seen for AM technology and isn’t likely to happen soon. Schafer plans on leveraging AM to build smaller parts for planes now, and slowly ramp up to (perhaps) hanger-sized 3D printers by 2050.
Materials are one of the roadblocks to building an entire plane using AM. Schafer’s design requires materials that don’t yet exist, including transparent aluminum (that might make Star Trek fans smile). Airbus might solve some of its material dilemmas by taking a page from Objet’s multi-material capabilities to build parts to fill its requirements.
GE has already embraced AM and is conducting its own research into processes using metal. The company is currently using laser sintering to build complex geometries out of titanium as part of the production of jet engines. The objects created are 4 ft. strips that are bonded onto the leading edge of fan blades to assist airflow and deflect debris.
Creating the strips using traditional manufacturing methods required a minimum of 10 hours and resulted in losing nearly half of the titanium. The switch to AM to create the parts saves the company around $25,000 per engine.
Moving from aerospace to architecture, 3D Model-to-Print (3DMTP) has launched a cloud-based service that, “automatically converts commonly-used architectural software files into 3D printable models.” This new service is the result of a three-year study. It uses algorithms to study the shape of the model and automatically fix any problems that might hinder printing.
“The solution that 3DMTP provides is one that has long been needed for our architectural customers,” states Kevin Carr, GM imaging division of Mastergraphics, a 3DMTP customer. “Not only does it save hours — even days — in the process of preparing 3D architectural design for 3D printing, it also significantly reduces the cost to prepare the designs, making 3D printing a more usable and affordable option for those wanting to make models of their architectural designs.”
Assuming all goes to plan, similar projects in other fields could expand the reach of AM by offering a way for people without CAD experience to create objects with relative ease.
Finally: Have you ever dreamed of having a bobblehead that immortalizes your features for all time? Headbobble.com is here to make that dream a reality. Creating your personalized bobblehead is a three-step process. Customers choose a body, send in a photo of their face and submit the order. Your likeness is then 3D printed, attached to the body you chose and shipped out. The service costs $90 and I can’t help but wonder if it was inspired by Eureka.
Below you’ll find a video that takes an in-depth look at AM and aerospace.
Sources: PRWeb, Forbes, Slate, Technology Review
Subscribe to our FREE magazine,
FREE email newsletters or both!Latest News
About the Author
John NewmanJohn Newman is a Digital Engineering contributor who focuses on 3D printing. Contact him via [email protected] and read his posts on Rapid Ready Technology.
Follow DE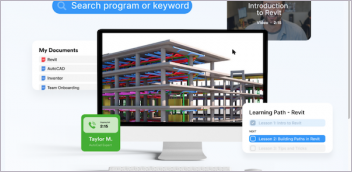

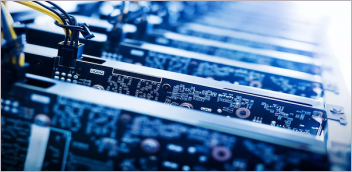
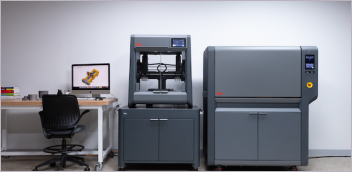